In-situ monitoring of processes in harsh environments demands the development of novel high-performance sensors. Polymer-derived ceramics (PDCs) thin-film sensors are highly suitable for real-time temperature or pressure monitoring in nuclear reactors, gas turbine engines, and spacecraft under extreme operating conditions, such as high-temperature, fluctuating pressure, high radiation flux, and oxidative or corrosive environment.
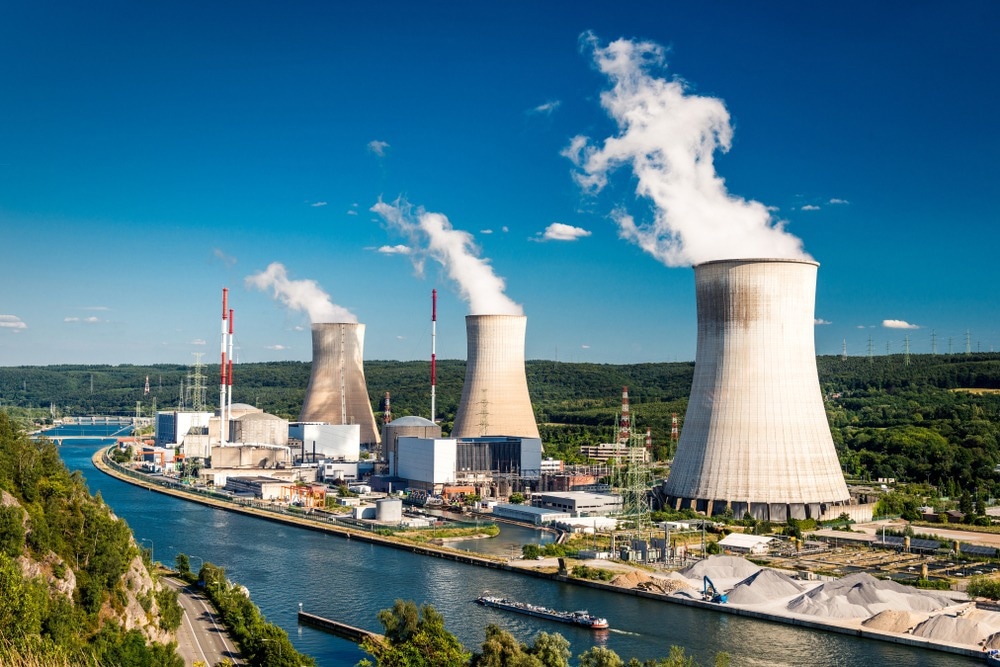
Image Credit: engel.ac/Shutterstock.com
Micro-electro-mechanical devices, such as pressure, temperature, strain, acceleration, and flow sensors, are essential for many harsh-environment applications. Harsh environments include elevated pressure, high temperature, corrosive and erosive atmosphere, or electromagnetic and particle radiation that can hinder the operation of the device.
These conditions are typically present in combustion chambers, chemical reactors, spacecraft propulsion systems, underwater vessels, and nuclear reactors. In recent years, there has been a growing demand for developing miniaturized pressure, temperature, and heat flow sensors with fast response times and low cost for in-situ real-time monitoring of processes in nuclear power plants and next-generation gas turbine engines.
Such sensors must operate reliably at temperatures of 300-800 °C, pressures exceeding 100 bars, and in the presence of ionizing radiation.
Ceramics Sensors for Harsh Environments
Pressure, temperature, and strain sensors based on conventional Si-based ceramics, such as SiC or Si3N4, exhibit high thermal conductivity, excellent mechanical stability, and oxidation resistance to temperatures exceeding 1000 °C without loss of functionality. However, such devices are mainly manufactured via powder sintering or chemical or physical vapor deposition methods, which require elevated processing temperatures and are unsuitable for manufacturing complex-shaped ceramic components. The ceramics' brittleness limits the possibilities for downstream machining of the sensor's components.
Novel Polymer-Derived Ceramic Technology
The PDC technology, where ceramic materials are derived from preceramic polymer precursors, is emerging as a strong alternative to conventional ceramic synthesis and manufacturing technologies. The PDC approach involves fabricating ceramic components from synthetic Si-polymer precursors that undergo cross-linking followed by pyrolysis.
The method enables rapid manufacturing of a wide range of high-performance non-oxide ceramic devices that are impossible to create with conventional ceramic fabrication methods.
Typically, silicon-based PDC materials are produced via thermal pyrolysis of cross-linked Si-polymer precursors containing light elements, such as C, H, O, N, or B, and exhibit similar mechanical and mechanical properties chemical properties to the conventional powder-based ceramics.
As previous studies have demonstrated, the morphology, microstructure, thermal stability, and high-temperature behavior of the synthesized PDC materials can be modified by incorporating different types of hetero-elements into the Si-based precursors at the molecular level.
The conductivity, temperature resistance, and radiation hardness of the PDC materials can be enhanced by tuning the elemental composition of the ceramics, which makes the technology particularly suitable for monitoring parameters, such as temperature, pressure, heat flow, and mechanical strain, in nuclear reactors.
Unique Properties of PDC
Due to their unique structure of PDC, which typically consists of the amorphous matrix phase and free-carbon phase, PDCs exhibit many outstanding characteristics, even in high-temperature environments, such as oxidation and creep resistance, semiconducting properties, and piezoresistive response. In addition, the PDCs are better suited (compared to conventional ceramics) for processing and fabrication using more energy-efficient additive manufacturing technologies and thin film deposition processes.
PDCs for Temperature Sensing Applications
Recently, a research collaboration between the Delft University of Technology in the Netherlands and the Luoyang Institute of Science and Technology in China created a SiAlCN PDC material obtained by precursor pyrolysis at 1000 °C. The researchers used the novel material to fabricate a temperature sensor with an operating range from 25 to 1000 °C. The extensive testing of the SiAlCN sensor demonstrated excellent repeatability, higher sensitivity, and faster response than conventional thermocouples.
PDC Thin Films for Optimized Temperature and Strain Sensing
Further development of the PDC technology was a thin-film deposition process based on laser pyrolysis performed at ambient conditions (without a protective atmosphere), proposed by scientists from the Department of Mechanical and Electrical Engineering at Xiamen University, China.
Compared with traditional furnace pyrolysis, the laser pyrolysis method is faster and more flexible in achieving the desired shape and size of the sensing element. The new approach also enhances the graphitization of the free carbon in the PDC material, resulting in enhanced electrical conductivity (particularly beneficial for strain sensors).
Laser pyrolysis induces the transformation of the Si-polymer precursor into high-crystallinity SiC, while conventional pyrolysis yields amorphous SiCN with low conductivity. The operating temperature range for the thin film temperature sensors was from ambient to 800 °C, while the strain PDC sensor operated reliably at temperatures up to 600 °C.
The main advantage of the PDC thin-film sensors over conventional ceramic devices arises from the improved scalability and customization of the fabrication process, as all precursors/reagents are in a fluid phase. The researchers demonstrated the great potential of laser pyrolysis for the cost-efficient fabrication of custom-designed thin-film PDC sensors on various substrates, such as superalloys, low-melting-point metals, and even plastics.
References and Further Reading
Xu, L., at al. (2022) In Situ Laser Fabrication of Polymer-Derived Ceramic Composite Thin-Film Sensors for Harsh Environments. ACS Applied Materials & Interfaces, 14(10), pp. 12652-12661. https://doi.org/10.1021/acsami.1c24628
He, J., et al. (2022) Polymer-Derived Ceramics Technology: Characteristics, Procedure, Product Structures, and Properties, and Development of the Technology in High-Entropy Ceramics. Crystals, 12, p. 1292. https://doi.org/10.3390/cryst12091292
Shao, P., et al. (2022) Temperature-sensing performance of polymer-derived SiAlCN ceramics up to 1000 °C. Ceramics International, 48, pp. 25277-25283. https://doi.org/10.1016/j.ceramint.2022.05.192
Colombo, P., et al. (2010), Polymer-Derived Ceramics: 40 Years of Research and Innovation in Advanced Ceramics. Journal of the American Ceramic Society, 93, pp. 1805-1837. https://doi.org/10.1111/j.1551-2916.2010.03876.x
Disclaimer: The views expressed here are those of the author expressed in their private capacity and do not necessarily represent the views of AZoM.com Limited T/A AZoNetwork the owner and operator of this website. This disclaimer forms part of the Terms and conditions of use of this website.