On February 3rd, 2023, at around 8:54 pm, an eastbound Norfolk Southern Railway freight train 32N derailed in East Palestine, Ohio. A total of 38 cars derailed, resulting in a subsequent fire that also damaged twelve additional cars.
Following the derailment, an explosion and fire occurred, leading the city council to declare a “state of emergency” on February 4th. Ohio Governor Mike DeWine further extended the evacuation area on February 6th.
The cause of this incident remains under investigation. The consequences are expected to be significant, with residents complaining of health problems and observing the impact on local wildlife, which has prompted them to initiate a class-action lawsuit against Norfolk Southern.
While immediate questions remain unanswered, the potential long-term repercussions of the derailment are concerning and could take years to mitigate.
By February 14th, the National Transportation Safety Board (NTSB) investigators had released their preliminary findings, which included the identification and examination of the specific railcar responsible for initiating the derailment.
According to the NTSB: “Surveillance video from a residence showed what appears to be a wheel bearing in the final stage of overheat failure moments before the derailment. The wheelset from the suspected railcar has been collected as evidence for metallurgical examination. The suspected overheated wheel bearing has been collected and will be examined by engineers from the NTSB Materials Laboratory in Washington, DC.”
What Typically Causes a Derailment?
The US freight rail network, spanning approximately 140,000 route miles, is the world’s largest and most cost-efficient freight system.
Although there has been a significant decrease in the number of derailments in the United States, rail traffic has also experienced a decline. In 2022, there were 1,000 derailments, indicating an increase in relative frequency.
According to researchers from the University of Illinois, two primary causes of train derailments are broken rails and bearing failures. Derailments resulting from bearing failures tend to occur more frequently in higher-track classes, where rail inspections are more frequent.
These bearing failures are more likely to transpire in bustling, densely populated areas.
Additionally, another Department of Transportation study conducted in 2022 revealed that nearly 20% of derailments were attributed to roller bearings overheating.
Surveillance footage of the East Palestine derailment seemed to capture video of the train’s wheel bearing overheating almost 20 miles away from where the train went off the tracks.
How Bad is a Derailment?
The evaluation of a train derailment’s severity often relies on assessing the financial damage incurred. This assessment can vary, taking into account factors like the cost difference between locomotives and freight railcars, as well as the variation in repair expenses for regular track versus special trackwork.
Another indicator of the physical impact of a train derailment is the number of cars involved. For instance, in derailments caused by bearing failures, around 55% of incidents resulted in the derailment of a single car.
On the other hand, derailments caused by broken rails or welds tend to involve a larger number of cars being derailed. Hence, it is important to understand the severity of derailments within each specific cause group.
What are Bearings, and How Do They Fail?
Bearings play a crucial role in trains and various other machines. They are essential components that need to meet strict requirements regarding load capacity, running accuracy, noise levels, friction, lifespan, and reliability.
At their core, bearings consist of rolling elements, such as balls or rollers, placed between two concentric, grooved rings. The relative motion of these rings enables the rolling elements to move with minimal resistance or sliding.
The concept of bearings can be traced back to ancient times when stones were used to facilitate the movement of logs. Today, bearing designs have evolved to support the complex drivetrains found in modern machinery.
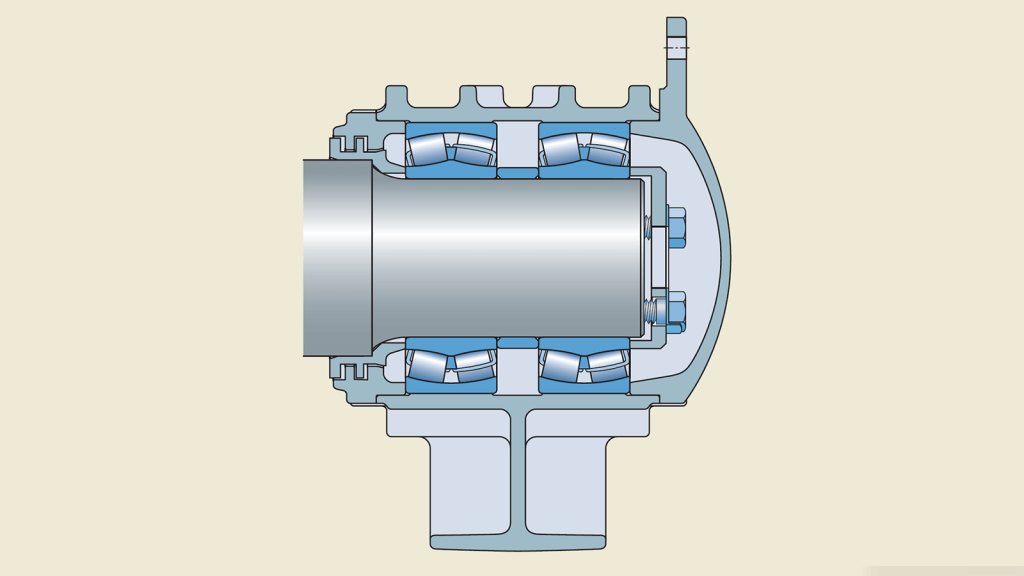
Typical axlebox bearing arrangement for 20-tonne axle payload. Image Credit: Teledyne Judson Technologies
Several factors can lead to bearing damage or failure. Due to the metal composition and high-speed rotation, bearings are subjected to extreme levels of heat and friction. Although most bearings manufactured today outlast their intended lifespan, they can still fail due to individual or combined factors, including:
- Material fatigue
- Lubrication problems
- Contamination due to ineffective seals
- Other, including improper handling/mounting/fits, or loads beyond specification
As trains, especially in the United States, have grown larger and heavier, the stresses exerted on both rails and their associated machinery have increased.
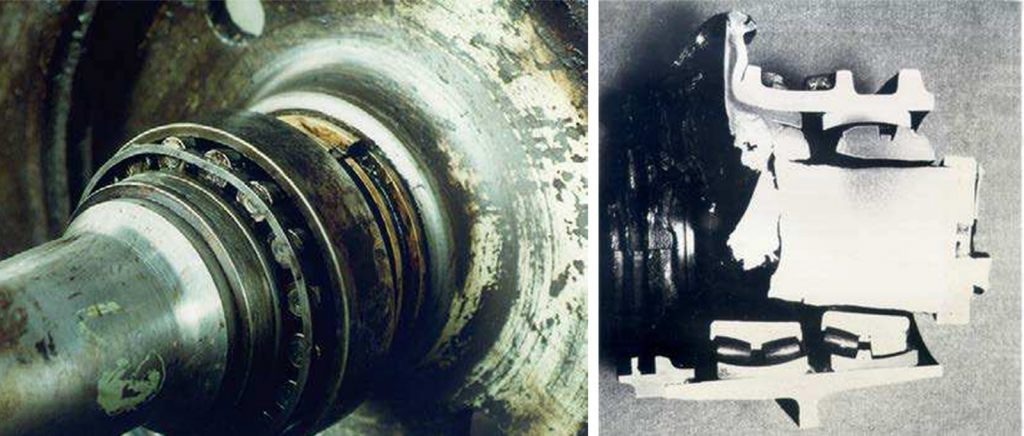
Left: Tapered roller bearing mounted on a railway wheel set. The cage was hit directly during mounting, resulting in permanent deformation. Right: Remains of a failed axle box (cut), as presented for the failure analysis. The outer ring of the inboard bearing was severely deformed. Based on the level of deformation, the metal reached a temperature well over 800 °C (1 470 °F). Image Credit: Teledyne Judson Technologies
Preventing Bearing Failure
Given the high stakes involved, preventing incidents is a top priority for both governmental and private entities.
To mitigate the risk of catastrophic train derailments, the United States has implemented bearing monitoring systems, which are used to identify problematic units and safely remove them from service.
Currently, the railroad industry employs two types of detection systems to monitor the health of freight railcar bearings during operation: acoustic detection systems and hot bearing detectors (HBD).
The first system utilizes wayside microphones to detect and alert conductors of potential high-risk defects.
The second system, HBD, is positioned alongside the rail tracks and employs non-contact infrared (IR) sensors to measure the temperature of various components, including train bearings and axles, as they pass over these detectors.
By utilizing radio signals, the HBD system notifies rail crews of any overheated components.
However, according to the NTSB’s report on the East Palestine derailment, a hot-box detector notified the crew of the issue just a few moments before the train derailed, meaning that it was too late for the crew to react:
“Train 32N was operating with a dynamic brake application as the train passed a wayside defect detector on the east side of Palestine, Ohio, at milepost (MP) 49.81.4. The wayside defect detector, or hot bearing detector (HBD), transmitted a critical audible alarm message instructing the crew to slow and stop the train to inspect a hot axle.”
Accurately measuring the temperature of a rapidly moving, intricate device poses a significant challenge. Within a mere 10 milliseconds, a train traveling 40 miles per hour covers approximately 8 inches, roughly the width of a bearing.
Factors like rust or discoloration can impede surface measurements, making it difficult to gauge the true condition of the bearings. Particularly in the early stages of defect development, HBD systems have shown inefficiency in accurately determining bearing health.
Several variables, such as bearing class and the location of IR scanning, can greatly impact the accuracy of the HBD temperature data. Consequently, the HBD system may either underestimate or overestimate the operating temperature of rail bearings.
In the case of overestimation, a bearing that is actually in good condition may be flagged as defective and consequently removed from service. Upon inspection, if no defects or issues are found, the bearing is labeled as “non-verified.”
In a study performed from 2001 to 2007, Amsted Rail found that nearly 40% of bearings flagged by HBD and removed from service were classified as ‘non-verified.’
If an HBD underpredicts the temperature of a bearing that is running hot, and an alarm is not triggered, catastrophic bearing failure may occur.
The same researchers also found that from 2009 to 2018, wayside HBDs failed to detect 151 defective bearings throughout the United States and Canada, all of which led to catastrophic derailments.
What Can Be Done? More and Better Sensing
HBDs, the most prevalent bearing health monitoring system utilized in the US, boast a network of over 6,000 devices spanning the nation’s railways. These devices are positioned at approximately 25-mile intervals along the railroad, as outlined in a report by the Federal Railroad Administration (FRA).
Their implementation has resulted in a noteworthy 59% decrease in train accidents caused by axle- and bearing-related factors since 1990, as confirmed by a 2017 study conducted by the Association of American Railroads.
During the passage of each freight car, the HBDs scan the surface temperature of the bearings and ambient temperature. Should the discrepancy between the two surpass a predetermined threshold set by the railroad company, an alarm is triggered.
Hotbox sensors are used in high-speed rail systems outside the United States. In Switzerland, these sensors play a pivotal role in safeguarding the country’s extensive tunnels, where they are positioned every 30 km (19 miles).
Even a minor distance can yield significant outcomes. The NTSB’s initial report on the East Palestine derailment includes a remark regarding the utilization of a hot bearing detector, commonly referred to as a “hotbox” detector:
On the Fort Wayne Line of the Keystone Division, NS has equipped their rail network with HBD systems to assess the temperature conditions of wheel bearings while en route. The function of the HBD is to detect overheated bearings and provide audible real-time warnings to train crews. Train 32N passed three HBD systems on its trip before the derailment. At MP 79.9, the suspect bearing from the 23rd car had a recorded temperature of 38 °F above ambient temperature. When train 32N passed the next HBD, at MP 69.01, the bearing’s recorded temperature was 103 °F above ambient. The third HBD, at MP 49.81, recorded the suspect bearing’s temperature at 253 °F above ambient.
A recent paper published in 2022 by the Department of Transportation highlights the positive impact of new technologies and enhanced imaging techniques for rail trucks and wheels combined with wayside detection systems. These advancements are yielding improved outcomes.
Data from the Federal Railroad Administration’s Accident and Incident database reveals a reduction in the number of equipment and vehicle components with potential safety concerns.
This can be attributed to the effective implementation of detectors, as failure to identify and rectify such issues on time can lead to unsafe operations, including derailments.
A trend analysis of the detector installations’ growth and the number of relevant derailment cause codes showed a strong correlation.
The increase in the number of installations shows a definite impact in reducing the number of derailments related to overheated bearings and poorly steered trucks. Effective detection of these defects has led the railroads and equipment owners to monitor their fleets and schedule maintenance to correct these issues.
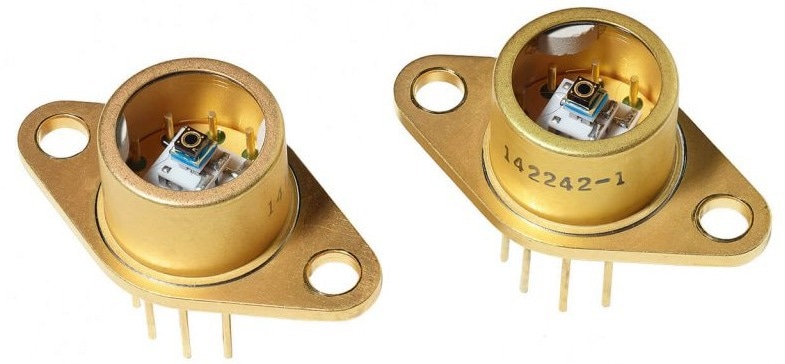
Mercury cadmium telluride sensors (HgCdTe)Thermal Sensors from Teledyne Judson. Image Credit: Teledyne Judson Technologies
An example of more accurate thermal imaging could come from mercury cadmium telluride sensors (HgCdTe), which can be much more sensitive than microbolometers, between a factor of three to as much as ten, depending on how the system is designed.
This advancement enables more precise temperature measurements and facilitates multi-location testing, resulting in a more sophisticated dataset that addresses the issues of under and over-prediction encountered in the past.
The analysis also highlights areas where further progress in detection technology can enhance equipment performance and promote operational safety in the railroad industry. For instance, broken rim failures, a leading cause of costly derailments, are yet to be adequately addressed by the sector.
While some progress has been made to demonstrate the available technology, widespread implementation of more accurate sensors could significantly reduce derailments.
Increasing the number of detectors can also be beneficial. By spacing the detectors farther apart, it allows for early detection of overheating in axle bearings, which, if left unattended, can lead to disintegration.
Presently, the Federal Railroad Administration does not impose federal regulations mandating the use of heat detectors and health-monitoring sensors.
The railroads and regulators have established criteria for detector placement based on rail type, speed limits, and accessibility for inspection and maintenance, aiming to improve safety outcomes. Implementing a standardized requirement could further enhance overall safety measures.
To prevent derailments, the agency has the authority to mandate rail companies to deploy heat sensors known as hot-box detectors, which can alert train crews about overheated bearings before accidents occur. Notably, these sensors are currently not subject to federal regulations.
The D.O.T. can also mandate railroads’ participation in a currently voluntary and unevenly used system that lets rail workers and railroads report near misses as they occur, helping regulators track risky practices in the future.
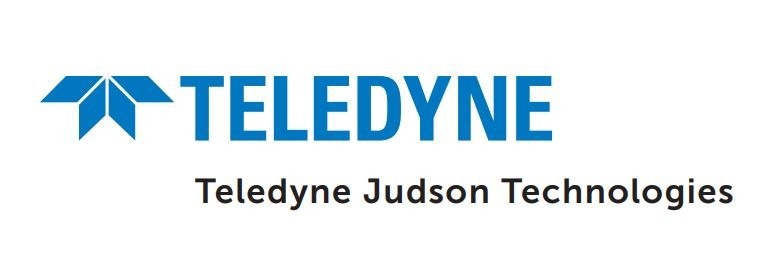
This information has been sourced, reviewed and adapted from materials provided by Teledyne Judson Technologies.
For more information on this source, please visit Teledyne Judson Technologies.