The scanner is mounted on top of the bin, measures and maps surfaces, send data via RS-485 or 4-20mA and the software records data and 3D map of contents as well as calculates level, volume and mass.
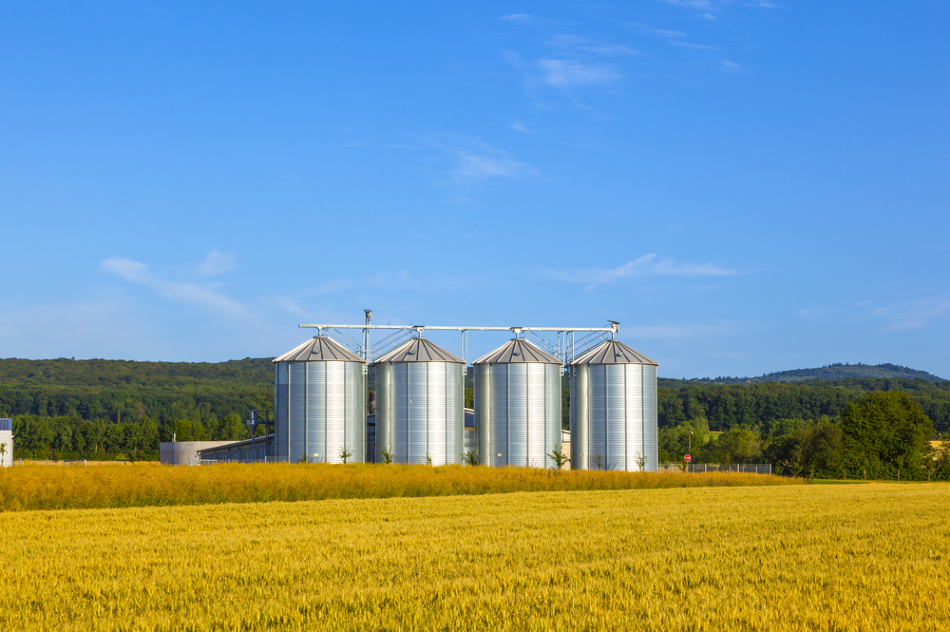
Image Credit: Shutterstock/travelview
Anatomy of a 3D Level Scanner
Figure 1 shows the anatomy of a 3D level scanner.
.jpg)
Figure 1. Anatomy of a 3D level scanner
The key features of a 3D level scanner are:
- Penetrates dust and requires minimal maintenance
- Self-cleaning with minimal routine maintenance required
- Sensor resists buildup of dust inside of transducer
- Works where other technologies are unreliable or have failed
.jpg)
Figure 2. Sensors inside stay clean in dusty environments
.jpg)
Figure 3. Flour mill installation
3D Differences from Conventional Level Measurement Sensors
The difference between 3D scanners and conventional level measurement sensors are:
- Reliable in dusty environments
- Accounts for uneven material surfaces
- Detects sidewall buildup
- Provides visualization of material surface
- Improves inventory accuracy
- Estimates material volume
- Appropriate for very large bins
Radar Sensor Shortfalls
Disadvantages of radar sensors are:
- Only a few models with high GHz perform reliably in dusty environments
- Measures level only at a single point in large vessel, does not take into account uneven topography
- Provides level only at one measurement point, but not volume
- No visual of material in the silo to detect high and low spots
- Costly, time-consuming maintenance or air purge needed for cleaning
- Can only view level of one vessel at a time – must view each sensor separately
Selecting the Right 3D Scanner
How to select the right 3D scanner is shown in table below.
Model |
S |
M |
MV |
MVL |
Bin Height |
Up to 200’ |
Up to 200’ |
Up to 200’ |
Up to 200’ |
Bin Diameter |
Up to 14’ |
Up to 45’ |
Up to 45’ |
Unlimited. Number of units determined per application. |
Beam Angle |
30° |
70° |
70° |
70° for each scanner |
3D Visual |
No |
No |
Yes |
Yes |
Output Data |
Average distance |
Estimated volume plus minimum, maximum, and average distance |
3D visual, estimated volume plus minimum, maximum, and average distance |
3D visual, estimated volume plus minimum, maximum, and average distance |
Best Application |
Tall, narrow bins with little or no corrugation |
Wide bins, taller than they are wide |
Wider bins, taller than they are wide |
Very wide bins |
All models can be used in silos with a larger diameter than specified, but with decreased accuracies as the beam angle will not span the entire surface of the material. |
Multiple Point Measurement Means Better Accuracy
Multiple point measurement eliminates guesswork and inaccurate readings. It is capable of measuring uneven topography that randomly forms inside bins. It accounts for cone up, cone down, or material buildup along bin sides. It detects irregular surfaces caused by multiple fill and empty sites. It determines absolute surface level values, volume and mass inside a bin. Operations can buy and sell commodities at the right time.
Food Processing
Challenge
Challenges of food processing were better stability and accuracy, primary interest is headroom distance, requires a desired 3D visualization, material prone to rat-holing and buildup and the old equipment was not working properly.
Proposed Solution
MV scanners were installed on all 21 tanks and all the tanks were monitored by 3DMultivision software.
Benefits
The benefits were more precise headroom, mapping and visualization for material prone to buildup and rat-holing, ability to monitor multiple bins with one solution and to improve inventory accuracy for very large silos.
Improve Inventory Accuracy for Very Large Silos
Two or more scanners were installed in a single vessel. Multiple scanners continuously measure and map material surface. It covers a greater surface area for more measurement points for greater accuracy. Software combines data from multiple scanners to provide a single 3D visual image. It is useful in large grain bins such as 105’, 130’ or million bushel bins. Scanner No 1 was mounted near the center of the bin.
Grain Storage
Challenges
The challenges are:
- Large 105’ diameter bin
- Contains dusty corn
- Concerned with employee safety
Solution
The solution is
- MVL model with 3D visualization
- 3DMultiVision software
Benefits
The benefits are:
- Improved volume accuracy
- More frequent, more reliable data
- Network viewing by multiple users
- No more climbing
Site-Wide Inventory Management from a Single Screen
The features of site-wide inventory management form a single screen are:
- View all bins at once – no tedious “one-at-a-time” opening of new window for each bin
- Set alerts for high or low status for each vessel
- One click access for a detailed bin view
- Suitable for a network of mixed scanner models
- Data is stored in a database and accessed on Local Area Network (LAN)
- Multiple users from multiple departments can access data base
- Customize views for just the tanks and data needed by each user
- Historical reports for managers, purchasing and financial use
Monitoring Corn and DDG Silos
.jpg)
Figure 4. Monitoring corn and DDG silos
Historical Reporting
.jpg)
Figure 5. Historical reporting
Ethanol Plant
Picture Scanners are installed on all four large silos.
Challenges
The challenges faced in the ethanol plant are extremely dusty corn bins, large bins with uneven topography, greater accuracy required and levels of multiple bins need to be monitored.
Solution
The solution is MVL-2 systems on 75’ diameter concrete silos and 105’ diameter steel bins, MV 3DLevelScanners on DDG concrete silos and MultiVision software
Benefits
The benefits are working in dusty environment, tracks level during fill and empty, improved inventory accuracy, ability to monitor levels of all bins in real time and optional neck extensions. The scanner can clear obstructions that may interfere with acoustic signals. The transducers assembly is lowered below obstacles, through a thick roof, or on a raised socket. Kits available in 2’, 4’, 6’, and 10’ lengths with either galvanized or stainless steel pipe. Performance is without signal degradation or special structural alterations or adapters.
Storage
Challenge
Challenges include a large concrete silo with obstructions in top of bin, very wide, large silos and desired better accuracy in dust.
Solution
The solution is a neck extension to clear structure and installing an MVL model with two scanners and 3D visualization.
Benefits
The benefits are improved volume accuracy using two scanners to cover surface, non-contact technology requires minimal maintenance and a safer work environment for employees
Angled Mounting Adapters
While using angled mounting adapters:
- Scanners must be mounted in an optimal location to provide the greatest level of accuracy
- Use when installation in desired location isn’t possible or must use existing hole
- Points transducers in desirable direction to improve coverage of the material surface
- Supports angles of either 10° or 20°
- Use only when mounting scanner in most desirable location is not possible
Teflon-Coated Sensors
Benefits of Teflon-coated sensors are that it resists buildup inside transducers in extremely dusty environments. It ensures performance in powdered, granular or solid materials generating excessive dust when bin is filling or active. It significantly extends the maintenance cycle by reducing need to clean device after prolonged periods of use. It reduces need to climb tall silos enhancing safety and saving time.
Soybean Meal Processing
In a soybean meal processing application, transducers were becoming blocked and needed to be cleaned every week. Since installing the Teflon-coated transducers, sensors have not been blocked. Slick, self-cleaning surface requires minimal maintenance.
Similar Applications
Similar applications include the following:
- Food processors in industries such as baking, pasta, and sugar
- When non-contact technology is a requirement
- Any material that is prone to clinging
MVL 3D Level Sensor System for Inventory Management — BinMaster

This information has been sourced, reviewed and adapted from materials provided by BinMaster.
For more information on this source, please visit BinMaster.