While optical dissolved oxygen (oDO) sensors require calibration, it is less frequent compared to polarographic versions.
New sensors (or new caps on existing sensors) need a two-point calibration in an air and air-free environment – preferably high purity-nitrogen (N5 purity; 99.999 %).
Optimal results from the zero-point calibration will be acquired using a calibration fixture with a chamber to hold the sensor and calibration gas – which, after three minutes of flow time, can purge all oxygen from the chamber. The fixture must permit the calibration gas to flow freely and at a constant flow rate, with no back pressure or leaks.
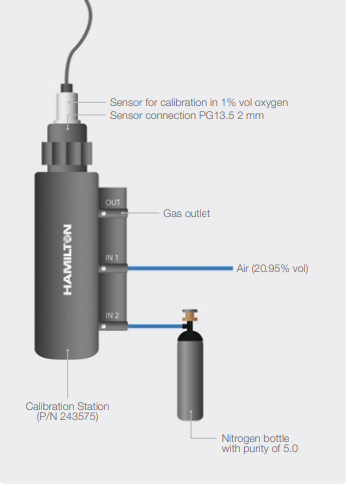
Figure 1. An example of a calibration station for use in working with DO sensors. Image Credit: Hamilton Process Analytics
The calibration procedure must account for external influences, such as temperature, pressure, and humidity. Internal temperature compensation should account for slow changes, but errors up to 3 % can occur if the temperature changes quickly.
The environment temperature must be stable prior to calibration to avoid these temperature-related errors. The temperature element is encompassed in the metal body of the sensor, which can result in errors up to 3 % if the sensor is over-handled before calibration.
Atmospheric pressure and humidity fluctuations at the measurement location must be accounted for. If not, there is a risk of a maximum potential error of up to 13.2 % for the air calibration point. The partial pressure of oxygen will fluctuate depending on the atmospheric pressure. Thus, to minimize the risk of error, the local atmospheric pressure must be accounted for during the air point calibration.
Increased humidity causes increased oxygen concentrations, particularly at higher ambient temperatures. To avoid this compounding error, the air point calibration must be executed in a water-saturated environment – by mounting the sensor above a beaker of water or wrapping the tip with a wet cloth. From this, the zero point calibration remains unaffected by pressure and humidity fluctuations, given the absence of oxygen.
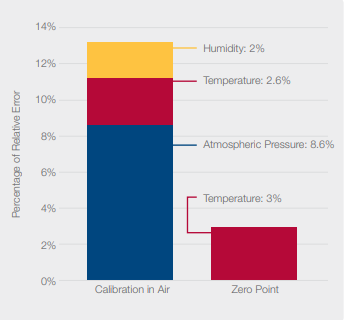
Figure 2. Up to 13.2% relative error can be found at the time of verification. Temperature, relative humidity at room temperature, and atmospheric pressure can all contribute to this error. Image Credit: Hamilton Process Analytics
To compensate for temperature, pressure, and humidity interferences, Hamilton’s ArcAir software has a built-in calibration walkthrough for oDO sensors – which contains inputs for atmospheric pressure and humidity.
The software automatically compensates for the local laboratory conditions inputted into the calibration walkthrough. If the local pressure and humidity are not being measured, they can often be estimated from outdoor conditions.
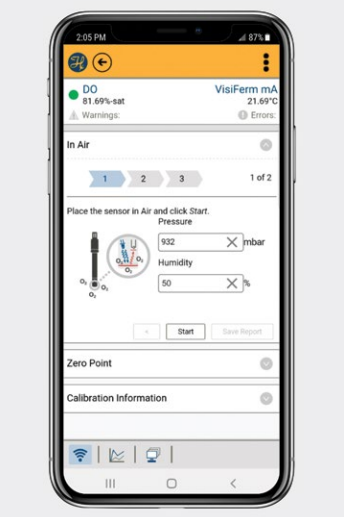
Figure 3. Example of the calibration wizard within ArcAir Software Version 3.2. Image Credit: Hamilton Process Analytics
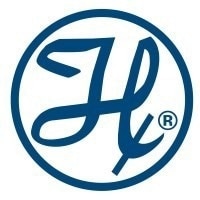
This information has been sourced, reviewed and adapted from materials provided by Hamilton Process Analytics.
For more information on this source, please visit Hamilton Process Analytics.