The Dencytee Arc monitors optical density (OD) in a broad range of processes, detecting both live and deceased cells, as well as any debris or particles that obstruct light. The observed optical density directly corresponds to the total number of cells in the solution.
Dencytee Arc is primarily used in yeast and bacterial systems and can also be employed in non-adherent mammalian applications, working alongside the Incyte Arc viable cell density sensor.
The measurement of viable cell density using Incyte Arc can be paired with total cell density from Dencytee Arc to estimate viability within a given process.
Measurement Modes and Units for Offline Correlation
The distinctive dual-mode total cell density sensor comes equipped with four predefined offline correlation models, all accessible through the ArcAir software:
Source: Hamilton Process Analytics
Name of the default offline correlation model |
Unit |
Comment |
Transmission |
AU |
- Only a transmission signal is used
- Usage of reflection signal is suppressed
|
Reflection |
Arb. Unit |
- Only reflection signal is used
- Usage of transmission signal is suppressed
|
CDW Yeast |
g/L |
Baker’s yeast in a stirred tank |
Turbidity Std |
NTU |
Formazine equivalent standard |
The transmission mode utilizes the light passing through the cell solution to the front detector, yielding a signal in AU (absorption units). This mode serves as a suitable starting point and is most fitting for processes with low cell density.
The reflection mode relies on the light reflected off cells in the solution to the back detector, generating a signal in Arb. Unit (arbitrary units). This mode is recommended in cases where other measurement modes produce a noisy signal or an inadequate fit to the offline data.
The CDW (cell dry weight) Yeast mode utilizes both transmitted and reflected light to determine the signal in g/L. This is the optimal choice for offline correlation when working with baker’s yeast in a stirred tank environment, particularly for high cell-density processes.
The Turbidity Std mode also combines transmitted and reflected light to establish the signal as NTU (Nephelometric Turbidity Units). NTU, also known as the Formazine Turbidity Unit, is the preferred option when performing offline correlation using a Formazine equivalent standard.
In addition to these, six custom offline correlation models can employ any of the supported units listed below. If other units are desired, the "Arbitrary Unit" option can be selected.
Source: Hamilton Process Analytics
Unit |
Definition |
Comment |
Arb. Unit |
Arbitrary Unit |
Relative unit. If the desired unit is not available, it is recommended to select this unit |
AU |
Absorption Unit |
Typical unit used to describe turbidity |
CFU |
Colony Forming Units |
|
E6 cells/mL |
Million Cells per Milliliter |
|
g/L |
Gram per Liter |
To differentiate between wet or dry weight, modify the correlation model name |
NTU |
Nephelometric Turbidity Unit |
Corresponding to FTU (Formazine Turbidity Unit), used as a Turbidity standard |
OD |
Optical Density |
|
PCV |
Packed Cell Volume |
|
The modeling units can be selected from the current offline analysis.
If the desired unit is not available, default to Arbitrary Units. Use Absorption Units to depict solution turbidity. Employ Colony Forming Units for systems that gauge cell density by counting colonies on plates. For systems measuring viability through trypan blue staining and microscopy, utilize Million cells per Milliliter.
In cases where cells are monitored by weight (wet or dry), choose Gram per Liter. Opt for Nephelometric Turbidity Units only if the correlation model was established using the Formazine equivalent standard.
Opt for Optical Density for unitless measurement of light passage through a solution, often done offline with cuvettes and a spectrophotometer. Packed Cell Volume is suitable for systems where cells are centrifuged from solution into a measured packed volume.
Once a model is chosen, ArcAir software guides the offline correlation modeling process.
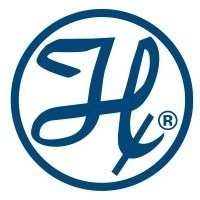
This information has been sourced, reviewed and adapted from materials provided by Hamilton Process Analytics.
For more information on this source, please visit Hamilton Process Analytics.