In an ideal world, the exact custom sensor required for a medical device application would be well-stocked by a sensor manufacturer. However, healthcare-related custom sensor technology takes time to conceptualize, design, and manufacture at scale.
![[Timeline] The Journey of Creating Custom Sensor Technology for Healthcare](https://www.azosensors.com/images/Article_Images/ImageForArticle_3091_17243107480136367.png)
Image Credit: Amphenol Advanced Sensors
This article discusses the steps taken to produce custom sensors for OEM medical devices.
Overview
Creating a customized sensor solution takes a lot of time. Additionally, due to the uniqueness of most OEM medical device sensors, developing novel solutions essentially starts from scratch.
Generally, there are seven steps to developing a custom medical sensor:
- Initial consultation
- Drawing exchange
- Quoting
- Prototype development
- Sample performance review
- Product qualification/certification testing
- Full production
Initial Consultation
The initial and most critical step in creating a custom sensor is the initial consultation, during which the details of the required sensor and its application are discussed with the manufacturer. This may include elements such as:
- Sensor application: What will the sensor be used for, and how will it be used?
- Sensitivity requirements: While accuracy is critical, the level of precision required can vary depending on the intended application.
- Temperature range: To ensure the sensor functions effectively at all expected temperatures.
- Environmental considerations: Moisture, dust, and other environmental factors that could affect the sensor.
- Connectivity: Will data transmission be wired or wireless?
- Intended lifespan: Is the sensor intended to be disposable or reusable, and if the latter, how long is the device required to operate?
- Special design considerations: Factors such as material selection, size, and housing.
Drawing Exchange
After the initial consultation, the design team will understand the final product and distill this vision down to an engineering drawing. The client will then review this drawing, and in almost all cases, the design will go through several iterations as it is refined.
In addition to the sensor's dimensions, the client will be required to review factors such as material selection, wiring diagrams, and other finer points of the sensor's assembly.
Quoting
Once a design has been finalized, the sensor manufacturer will draw up a quote, which should include a breakdown of:
- Unit cost at volume
- Prototyping costs
- Shipment logistics
- Turnaround time (relative to the size of the order)
- Tooling cost considerations
- Non-recurring engineering fees (if applicable)
Prototype Development
During the prototype development phase, the client receives their first visualization of a real final product. The manufacturer will use the CAD, BOM, and other product documents from the design phase to create physical prototypes, allowing the client to interact with a physical version of their product before committing to production.
With these initial samples, the client can examine critical-to-quality elements, such as the biocompatible materials employed, or conduct preliminary tests for functionality and performance, allowing for further adjustments before the product is finalized.
Sample Performance Review
Similarly to the previous stage, the client reviews the sample for performance, functionality, and quality, but at a much more detailed level. Elements to evaluate include:
- Accuracy in detecting and measuring data
- Consistency and reliability of the sensor's performance over time
- Durability against the rigors of real-world use without breaking or malfunctioning
- Ease of use and user-friendliness, ensuring the sensor is intuitive and straightforward for medical professionals to use
- Size and fit of the device for its intended application
While it is possible to change the sensor after this stage, such changes will drastically impact the project's timeline and budget.
Product Qualification/Certification Testing
The product qualification and certification testing stage is another layer of review, qualification, and certification testing designed to prove the sensor's ability to function safely and accurately in its intended environment.
This type of testing ensures that the medical device meets all applicable national, international, and industry standards set by the FDA, CE, or the EU's MDD.
This is often completed by independent third parties who review a wide variety of elements, including:
- Radiofrequency emissions
- Electromagnetic compatibility
- Environmental conditions (including temperature and humidity resistance)
- Materials safety/biocompatibility
- Power usage and efficiency
Documentation and reporting processes are also critical components of the product certification process.
Manufacturers must provide extensive documentation and data to demonstrate that their prototype medical sensors meet all necessary standards and regulations. This includes detailed technical files, user manuals, labeling information and other data that demonstrate compliance with regulatory requirements.
Full Production
Once all testing is complete, the manufacturer will produce the sensors according to a pre-agreed quality, quantity, and timeline.
During full production, manufacturers continuously monitor the manufacturing processes for product consistency and quality control purposes, ensuring that the high-quality medical sensing solution meets all regulatory requirements and customer expectations.
Development Timeline
In general, the process outlined in this article takes about a year and a half to complete; however, this can be affected by several factors.
A client's readiness will affect the time it takes to develop a sensor. Clients will usually know many key details about their required sensor, such as sensitivity, size, and intended lifespan. However, when clients are in the early stages of product development and are not clear on the specific requirements of their sensor, development will take longer.
Supply chain conditions can significantly impact development time, as demonstrated during the COVID-19 pandemic. No supply chain is impervious to outside factors causing disruptions, such as severe weather.
Meeting compliance requirements so that medical sensors are approved for use can take time. Depending on the client's location, this can mean extra rounds of testing and evaluation or, in some cases, travel to the testing facility or having an inspector come on-site.
Conclusions
While creating a custom sensor for an OEM medical device does not happen overnight, it is essential to ensure device performance meets expectations. Working with a sensor manufacturer to develop a custom sensor solution ensures that the final product can withstand the application's demands.
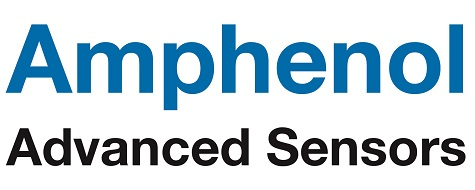
This information has been sourced, reviewed and adapted from materials provided by Amphenol Advanced Sensors.
For more information on this source, please visit Amphenol Advanced Sensors.