Advanced industrial sensor technology is constantly evolving to meet the demands of a wide range of applications. These sophisticated and versatile sensors support devices and their operators in doing their jobs effectively, but their complexity can lead to some confusion around their traits and operation.
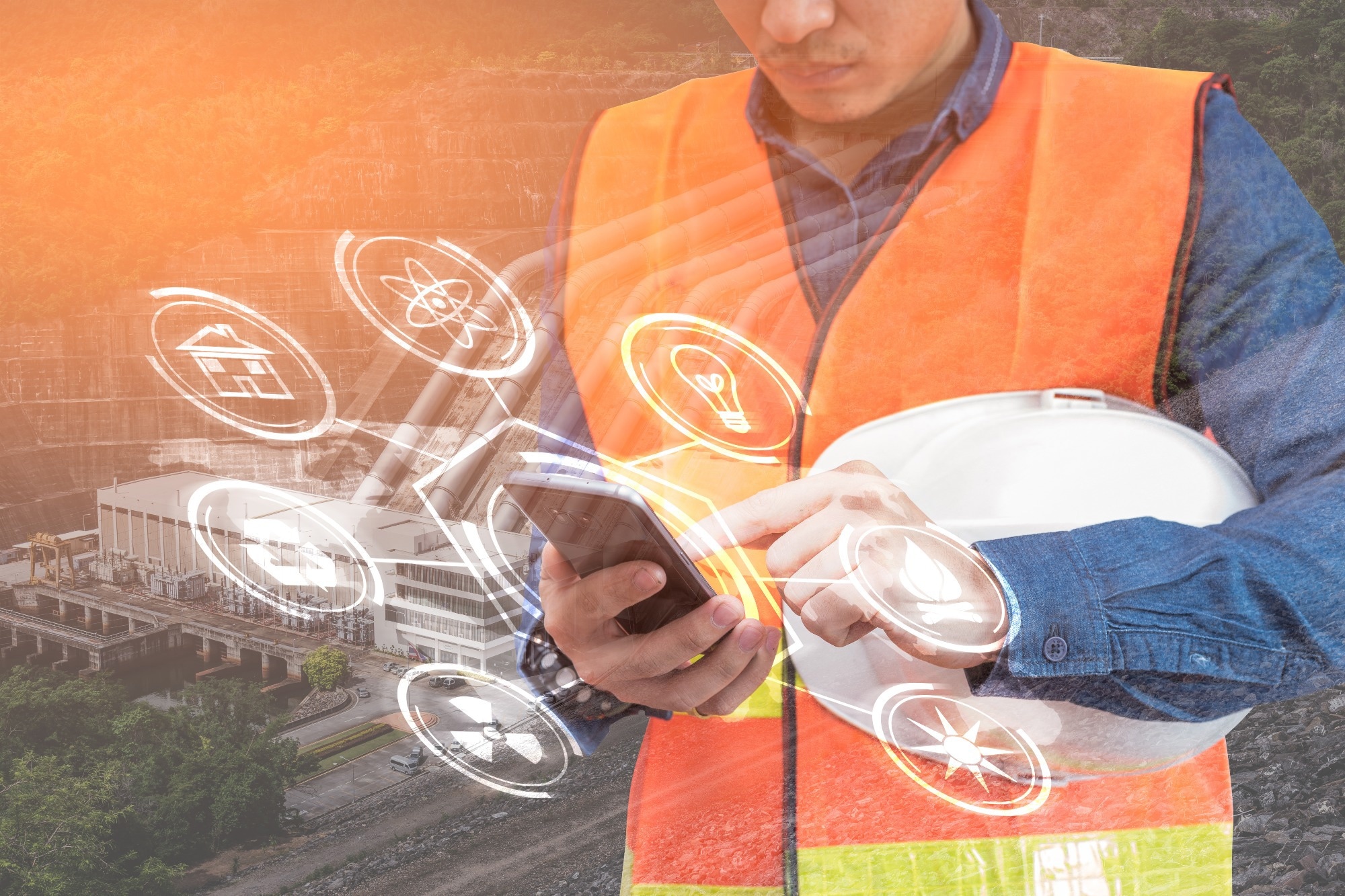
Image Credit: TimeStopper69/Shutterstock.com
To that end, this article features a list of the most frequently asked questions about industrial sensors, along with their answers.
1. What contaminants could adversely affect humidity and gas sensors’ operation?
While advanced sensor technology is exceptionally sophisticated, these devices are not completely immune to the impact of contaminants on their functionality.
Humidity and gas sensors like CO2 and O2 sensors are sensitive to certain contaminants, which can potentially affect their design and application.
Volatile Organic Compounds (VOCs)
Many gas sensors - most notably those designed to detect specific gases - can suffer from cross-sensitivity errors when exposed to VOCs. For example, these compounds include chemicals such solvents and cleaning agents; and hydrocarbons emitted from lacquers, paints, and building materials.
Dust and Particulate Matter
The sensor elements of humidity and gas sensors can become clogged or covered by particles present in the air. This can potentially lead to inaccurate readings and slower response times. Routine cleaning and maintenance are required to ensure consistent and reliable performance.
Corrosive Gases
Sensors may degrade faster when exposed to corrosive gases such as chlorine, ammonia, and hydrogen sulfide. These gases can impair the sensor’s function by corroding the sensor elements or building up as films on the sensor's surface.
Moisture
Gas sensors are especially sensitive to excess moisture, which can lead to condensation on the sensor surface that triggers short circuits or erroneous readings. In the case of humidity sensors, extended periods of frost or condensation can alter the properties of the sensor materials, causing permanent damage to them.
2. What should be considered when selecting a sensor for a specific application?
Speaking to an advanced sensor engineer to discuss specific needs is always advisable, but decisions around sensor selection tend to include some key considerations. This is the case whether the sensor is required to measure temperature, pressure, gasses, humidity, or any other metric.
These considerations include:
- The nature of the application itself.
- The environment in which the sensor will operate.
- The expected temperature ranges within which the sensor should measure.
- The level of accuracy required from sensor readings.
- The speed at which readings must be acquired.
- The type of packaging or housing required by the sensor.
- The sensor’s circuit design.
- Whether the sensor’s output is analog or digital.
3. What are the various sensor communication protocols?
Commonly employed sensor communication protocols include:
BACNET
BACNET is a standardized protocol employed in a range of building automation and control systems (including sensors), enabling these to efficiently communicate and share data within a networked environment.
I2C (Inter-Integrated Circuit)
I2C is a protocol designed for low-speed peripherals, allowing the connection of processors or microcontrollers in a multi-master, multi-slave configuration. This particular protocol is designed to facilitate packet-switched communication in a single-ended, serial bus format. Addresses are used to manage multi-device communications.
Analog Outputs
Analog outputs provide a continuous signal, varying this single to represent different physical measurements. Many sensors make use of these outputs, directly reflecting the magnitude of a measured parameter as an electrical signal, for example, voltage in relation to temperature. This approach means that it is particularly easy to interface with analog input devices.
Modbus
Schneider Electric, formerly Modicon, developed the Modbus communication protocol. This protocol is commonly found in industrial environments and used for client-server communication between devices. Modbus offers simplicity in terms of deployment and maintenance across a range of network types.
CANbus (Controller Area Network)
The robust CANbus communication standard facilitates communication between devices and microcontrollers within vehicles or industrial systems. This protocol does not require a host computer, and it is especially notable for its high-speed communication potential, sophisticated error handling, and reliability.
LINbus (Local Interconnect Network)
LINbus is a cost-effective serial network protocol that is primarily used to manage communication between components in automotive applications. LINbus is a simpler alternative to CANbus, ideal for less complex tasks such as controlling windows, mirrors, and seats. LINbus operates over a single wire while offering speeds up to 20 kbps.
4. What is the difference between absolute and gauge pressure sensors?
Absolute pressure sensors measure pressure relative to a perfect vacuum. Absolute pressure can be understood as the total pressure at a point, as measured from zero or vacuum.
Absolute pressure measurements are essential where accurate pressure readings are needed regardless of atmospheric changes; for example, in scientific research applications, when measuring barometric pressure and altitudes, or in high-precision manufacturing applications.
Gauge pressure sensors measure pressure relative to atmospheric pressure, adjusting their readings according to changes in the ambient air pressure.
This measurement type is ideally suited to applications where the interaction with atmospheric air is critical, such as fluid tanks and pneumatic systems that are open to the atmosphere. Altitude or weather can impact gauge pressure readings, as these are dependent on the measurement site’s atmospheric pressure.
5. What is the difference between single-channel and dual-channel NDIR sensors?
Single-channel NDIR CO2 sensors measure CO2 using one wavelength. They are well suited for use in environments that routinely return to baseline CO2 levels after any changes in CO2 level, such as auditoriums or classrooms.
In contrast, dual-channel NDIR CO2 sensors use two wavelengths. One of these wavelengths is used as a reference, allowing them to maintain accuracy as CO2 levels change.
6. What is the difference between NTC and PTC thermistors?
In order to answer this question, it is necessary to understand how each type of thermistor functions and its most common applications.
NTC thermistors' resistance decreases as temperature increases. This negative correlation means that they are sensitive to temperature changes, particularly when used in colder conditions.
These thermistors are most commonly found in applications where precise temperature measurement is needed, such as electronic devices, medical instruments, and automotive sensors. NTC thermistors are also used in electrical circuits to help prevent overheating and in rechargeable batteries to monitor temperature and charge status.
PTC thermistors increase their resistance as temperature increases. These thermistors are typically employed as over-current protectors in circuits and as self-regulating heating elements.
PTC thermistors are useful in applications such as hair dryers or space heaters where it is necessary to prevent overheating for safety reasons. They also have the capacity to reset themselves as they cool down, in contrast with fuses, which require replacement after a single use.
The key difference between NTC and PTC thermistors lies in their application.
NTC thermistors are suitable for more precise temperature measurements due to their rapid response to temperature changes and sensitivity. In contrast, PTC thermistors are more suited to applications requiring a sharp increase in resistance at a specific temperature to trigger a protective mechanism.
NTC thermistors are ideally suited to applications requiring continuous temperature monitoring, while PTC thermistors are useful in safety-focused applications involving temperature thresholds.
7. Are there any specific issues with battery-powered devices?
Battery-powered devices come with their own set of challenges, but these can be managed.
For instance, in situations where a steady power supply is not available, like with portable gadgets, it is possible to design advanced sensors that make the most of their limited power. This typically involves fine-tuning how the device uses power and how often it takes measurements to maximize battery life, all while ensuring accuracy and reliability.
Of course, it is important to remember that batteries do not last forever, so any device relying on batteries will eventually need a replacement.
8. How should sensors be calibrated?
In the most general sense, advanced sensor technology should not require recalibration after its initial installation, particularly when working with custom advanced sensor technology. This is because custom advanced sensor technology has been designed to accommodate the specific needs of the application.
By the time it needs to be recalibrated, the sensor will likely be at the end of its useful life. At this point, the sensor should be replaced outright.
Sensor calibration is difficult and requires a lot of controls to ensure it is done correctly, particularly when done in the field. This is not always possible at the point of application.
There are exceptions, however. Some sensors can - and should - be routinely recalibrated on a schedule; for example, sensors used in indoor growing applications must be recalibrated after each growing season.
Regardless of the application in question, it is advisable to seek input from an advanced sensor manufacturer to confirm the sensor technology required, as well as its lifespan and maintenance schedule.
9. What is the best way to communicate with a T9602 Harsh Environment Humidity and Temperature Sensor?
The ChipCap 2 Application Guide is available for T9602 sensor, which provides full guidance on communicating with the sensor.
10. What is a beta in the context of thermistors?
A beta can be understood as a ratio that determines the slope of a resistance curve.
A thermistor’s resistance curve is a graphical representation that shows how the resistance of the thermistor alters in line with temperature. This curve is key to using and understanding thermistors because it assists users in predicting their behavior in specific thermal environments.
A typical resistance curve involves a number of elements.
- The shape of the curve: The shape of the curve for NTC thermistors generally displays a steep drop in resistance as temperature increases. The shape of the curve for PTC thermistors, however, generally displays an increase in resistance as temperature rises above a specific threshold.
- Temperature coefficient: The curve highlights the thermistor’s temperature coefficient. This is negative for NTCs (because resistance decreases alongside an increase in temperature) and positive for PTCs (because resistance increases alongside an increase in temperature).
- Calibration: The curve will be used to calibrate the thermistor in practical applications, therefore ensuring accurate control or temperature measurements. This also facilitates the conversion of resistance readings into precise temperature values.
- Sensitivity: The curve’s steepness at any given point can show the thermistor’s sensitivity, with a steeper slope indicating higher sensitivity to changes in temperature at that specific range.
11. What is a thermistor resistance table?
A thermistor’s resistance table is a detailed chart that lists specific resistance values at different temperatures. This table is useful for interpreting a thermistor's resistance readings and deriving the corresponding temperature measurements.
A resistance table includes a number of useful functions.
- Tabulated data: The table will generally feature columns with temperature values shown alongside their corresponding resistance values. A precise resistance value will be determined through calibration for each temperature point.
- Ease of use: Rather than using complex curves or equations to calculate the temperature from resistance, users can directly look up or interpolate values in the table in order to locate the temperature associated with a measured resistance.
- Precision and application: These tables are vital in applications that necessitate precise temperature monitoring and control. They are also key when it comes to preventing errors that could arise from manual approximations or calculations.
- Customization: Resistance tables can be tailored to different types of thermistors or application needs. This allows them to provide relevant data over the temperature range related to the device’s specific operational environment.
A thermistor manufacturer should be able to provide appropriate resistance table datasheets or technical documentation.
Acknowledgments
Produced from materials originally authored by Amphenol Sensors.
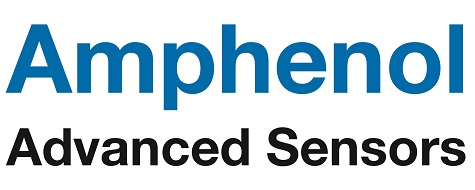
This information has been sourced, reviewed and adapted from materials provided by Amphenol Advanced Sensors.
For more information on this source, please visit Amphenol Advanced Sensors.