Many users in the industrial sector want to know the best way to calibrate their sensors to ensure optimal performance and longevity. While many sensors can be calibrated, this is not always straightforward with advanced sensor technology, especially during routine maintenance.
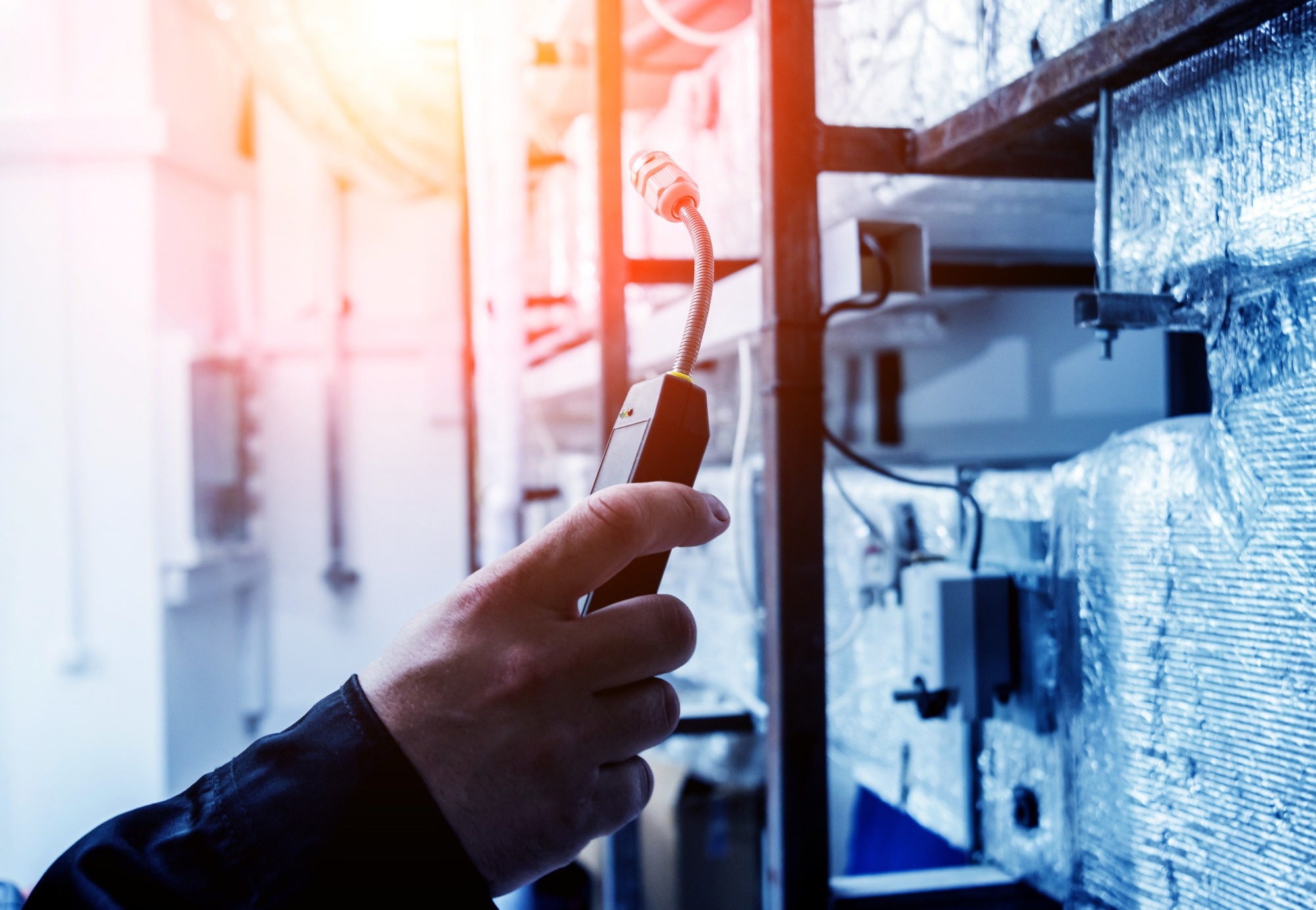
Image Credit: Roman Zaiets/Shutterstock.com
Calibrating sensors that are already in use can be complex and requires careful planning. This should be approached from two perspectives: both logistically and economically.
Sensor Calibration: Logistical Considerations
A commercial HVAC system designed to heat and cool a 10-story building offers a compelling case study for the logistical challenges of sensor calibration. This system is large and complex and requires several components to continue running at peak performance.
In this case, accessing a CO2 or temperature sensor would be challenging, as it is usually not feasible to shut down the system and remove the component. Retrieving any HVAC component typically requires careful planning, disassembly, and prompt replacement, followed by testing to ensure the system remains operational.
The sensor must also be replaced when it has been calibrated, potentially causing further disruption to the system. This process typically requires a lot of time and effort.
Sensor Calibration: Economic Considerations
The time and effort required to calibrate sensors will also have an economic impact.
Accessing sensors requires financial investment for the team or individual involved, and retrieving them often necessitates halting machinery or shutting down production processes. Regardless of the industry, production downtime invariably leads to financial losses.
Calibrating certain sensor types can be complex, and if done incorrectly, it can create a potentially expensive issue. It often requires an expert with specialized equipment, which is costly.
Advanced Sensor Calibration
Advanced sensor technology means that sensor calibration does not always have to be a consideration.
This is because advanced sensor technology tends to be designed and manufactured with accuracy at its core. These sensors often include features such as self-calibration or continuous monitoring to ensure ongoing peak performance with no manual recalibration requirements.
NDIR CO2 Sensor Calibration
Due to their functionality, NDIR CO2 sensors are widely considered the best option for monitoring CO2. These sensors have the capacity to continuously recalibrate themselves, or, in the rare instances that recalibration is required, this can be achieved quickly and easily using software tools.
Amphenol Advanced Sensors' single-channel NDIR CO2 sensors with ABC Logic technology, as well as their dual-channel CO2 sensors, provide this capability. However, dual-channel sensors will require field recalibration.
Humidity Sensor Calibration
Calibrating a humidity sensor typically necessitates a tightly controlled environment with highly specific temperature and water vapor pressure. It is extremely difficult to create a suitable microenvironment in the field or to manage these controlled conditions effectively.
The level of delicacy required can easily lead to a new set of issues, so in most applications, it is easier to simply replace a humidity sensor than attempt to recalibrate it.
Temperature Sensor Calibration
A thermistor cannot be calibrated, meaning that a temperature sensor cannot be calibrated. Thankfully, advanced temperature sensors boast a long life of up to 25-30 years with no loss of accuracy.
Pressure Sensor Calibration
There is a great deal of variation in terms of calibrating pressure sensors. Some can be calibrated, but this typically involves a sophisticated process that is very difficult to complete in the field. Other types of pressure sensors—for example, MEMS-based pressure sensors—cannot be calibrated at all.
The Alternative to Sensor Calibration
It is natural to be concerned about how sensor technology will work and remain accurate over its useful life. A sensor is only as effective as its calibration out of the box, so it is important to stay ahead of potential performance issues arising due to age or frequency of use.
There are three key solutions to this issue.
1. Invest in Advanced Sensor Technology from the Start
Advanced sensor technology, especially when customized for specific applications, requires a greater investment compared to off-the-shelf products. This is similar to how a luxury car model costs more than a base model.
Custom sensors are engineered to meet the exact demands of the application and ensure a suitable, useful life. They offer enhanced functionality, robustness, and accuracy, leading to reliable performance and minimal disruption.
As a result, they provide a better return on investment compared to generic sensors with shorter lifespans, lower accuracy, or reduced reliability.
2. Develop and Maintain a Replacement Schedule
No device will work forever; everything has a useful life, including advanced sensors. With this in mind, it is advisable to pre-emptively plan for sensors’ replacement before performance is impacted.
Users are advised to consider the sensor manufacturer's recommended lifespan for each sensor type before confirming a replacement timeline that factors in these deadlines.
It is important to regularly review and adjust the replacement schedule based on the sensors' actual performance in the field. Technological advancements may extend sensor lifespans, which could affect the timing of replacements.
It is also important to streamline the replacement process itself by organizing technical support and allocating appropriate budgets ahead of time. This is key to minimizing downtime and maintaining operational efficiency.
By maintaining a proactive replacement schedule, consistent, reliable data can be ensured, and systems can be maintained at peak performance without interrupting normal workflows.
3. Pay Close Attention to Warning Signs
There are instances where sensors do not last as long as intended, and this is an issue that can arise with any device or machine.
It is crucial to continuously monitor sensor performance and outputs, replacing them if unusual deviations or degradation are detected. Addressing issues caused by sensor malfunctions can be both costly and frustrating, making early detection and replacement essential.
Conclusion
Users of sensors need reassurance that the components in their products or processes continue to operate efficiently and effectively. While calibration is a necessary maintenance task for many types of technology, advanced sensor technology can significantly reduce or even eliminate the need for frequent calibration.
Acknowledgments
Produced from materials originally authored by Amphenol Sensors.
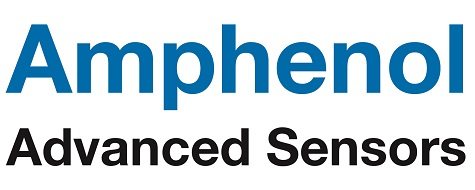
This information has been sourced, reviewed and adapted from materials provided by Amphenol Advanced Sensors.
For more information on this source, please visit Amphenol Advanced Sensors.