Jun 20 2014
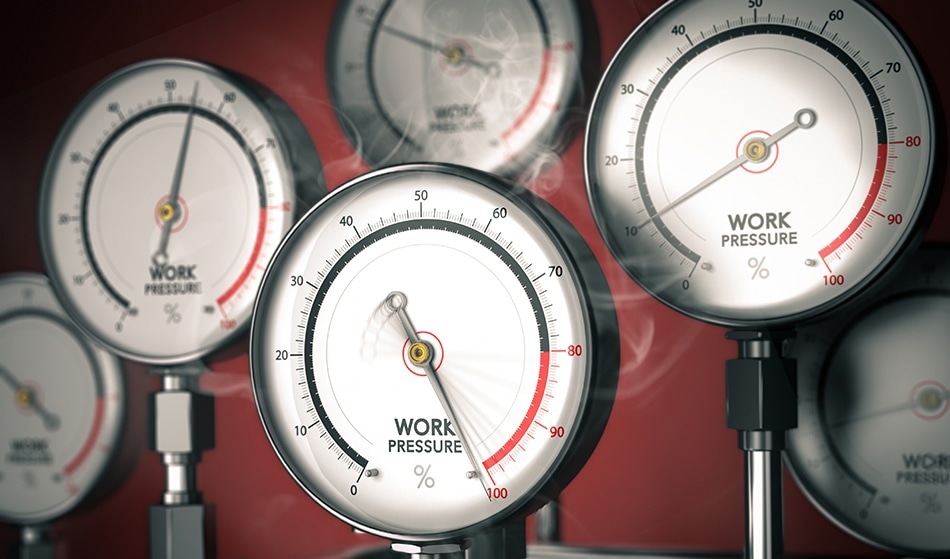
Image Credits: Olivier Le Moal/shutterstock.com
A strain gauge is a device that shows variable electrical resistance when exposed to external forces or strain. There are many different types, such as semiconductor strain gauges, wire strain gauges, and foil strain gauges. Most strain gauges are foil types with different forms and shapes to suit several different applications. They were invented in 1938 by American electrical and mechanical engineers Edward E Simmons and Arthur Claude Ruge.
Strain gauges also serve the purpose of measuring torsion, compression, and static or dynamic elongation of a body when directly attached to it.
Basic Principle of Strain Gauge Measurements
The length of any metal wire increases with the application of force. The strain developed in the wire increases when the wire exerts continuous force. Consider L1 as the original length of the wire and L2 as the length of the wire after the application of force. Now, the strain in the wire is given by the formula:
ε = (L2 – L1)/L1
While carrying out strain measurements, the strain gauge is linked to a Wheatstone bridge circuit. The circuit consists of a combination of two gauges, (i.e., half bridge), four gauges, (i.e., full bridge), or a single gauge (i.e., quarter bridge). The half and quarter bridges are provided with precision resistors.
The Wheatstone bridge is provided with a stable DC power supply and a signal conditioning circuit. When a force or stress is applied to the attached strain gauge, a change in resistance takes place which leaves the bridge circuit unbalanced. As a result, a signal output is produced, which is a function of the amount of stress applied. The generated signal is then amplified by the signal conditioning circuit depending on the application.
The relationship between the change in resistance and strain is measured by a quantity called the gauge factor.
Applications
The major applications of strain gauge are listed below:
- Measurement of quantities such as torsion force, shear stress, pressure, deflection and vibrations
- Measurement of the magnitude of an applied tensile or compressive force in load cells used in scales, weighbridges, and hoppers
- Monitoring constructional structures such as buildings and bridges
- Other industries, such as power generation, medical, oil, and gas, aerospace, and automotive.
- Incorporation into pressure sensors
- Incorporation into microelectromechanical systems (MEMS) devices to measure strains at microscale from pressure, sound or acceleration
- Mercury-in-rubber strain gauges can be used to measure blood flow in a limb or appendage.
- New applications using composite nanoparticle conductors: these have high gauge factors and low energy consumption.
Sources and Further Reading
This article was updated on 30th May, 2019.