By Kalwinder KaurUpdated on Mar 21 2019
Modern vehicles heavily rely on automotive safety units and the electronic components that are used to control these systems. This article focuses on two types of control units: the Accelerator Pedal Position Sensor (APP) and the Throttle Position Sensor (TPS).
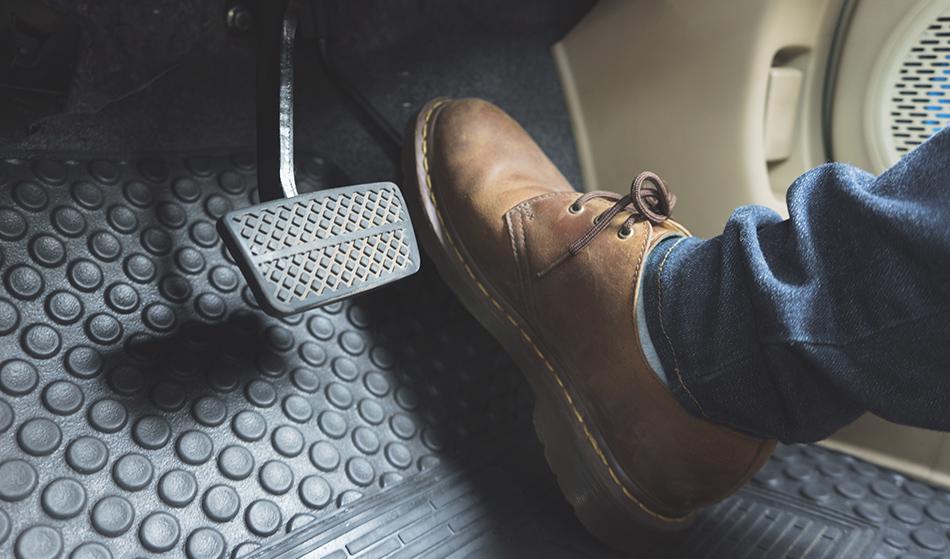
Image Credits: JimAK_Photo/shutterstock.com
Accelerator Pedal Position (APP) Sensor
The ability to accelerate smoothly down the road and avoid poor acceleration while using an adequate amount of energy is attributed to the accelerator pedal position (APP) sensor. The accelerator pedal position sensor, which is fixed to the throttle body of the 'electronic throttle control system with intelligence' (ETCSi), monitors the position of the throttle pedal.
The accelerator pedal position sensor is also involved in converting the acceleration movement when the pedal is pressed into an electronic signal, which then initiates throttle body control either as opening or closing movements.
The accelerator position information is transferred to the throttle actuator control (TAC) module and the powertrain control module (PCM). The APP sensor comprises two individual sensors, with both sensors designed to have individual sensor return wiring. Each sensor has a varying voltage range.
The PCM system receives and processes the electrical signals from the ACC sensors, along with signals from the direct current (DC) motor, which sets the throttle plate through a throttle cable. When the driver presses down on the accelerator pedal, the pressure rotates the throttle plate inside the throttle body, which opens a passage inside this unit to allow for airflow.
As the air travels through the throttle passage to the intake manifold, it activates airflow sensors that manipulate the engine control unit and force fuel into the fluid injector system.
The accelerator pedal position sensor system is typically referred to as the ‘drive by wire’ system and, as mentioned, delivers information to the engine control module systems about both the accelerator pedal position and the pressure and speed on the gas pedal.
As explained in the video below, the APP sensor is also associated with other modes of action in an automated system, one of which includes the reverse mode. During this mode of action, the PCM changes the acceleration pattern of an automated vehicle when in the reverse position.
Accelerator Pedal Position Sensor
Video credit: ADPTraining/YouTube.com
The sensor that makes up the APP sensor unit is called a potentiometer (mounted on the accelerator pedal). In some sensors, there is also a second and third sensor to make up the APP sensor unit. In terms of a hierarchical system, the first sensor is the main input to the full throttle. If there is a discrepancy between either the output voltage signal by the potentiometers monitoring the pedal position or the sensor itself, the PCM unit will reduce the performance of the vehicle, thereby setting the APP unit into a 'limp-home-mode'.
The signals generated by each of the potentiometers are different. While one of the potentiometers will relay a voltage signal (varying between 0 and 5 volts) to the PCM unit about the position of the pedal, the second and third sensor both behave as a back-up unit. During the movement of a vehicle, the PCM unit is continuously comparing the output by all three potentiometers of the APP sensor system.
Failure of the APP sensor will most commonly result from continuous exposure to high heat levels because of its location on the floorboard, which is adjacent to the vehicle firewall. Although APP sensors will typically maintain adequate functionality throughout the lifespan of the vehicle, they will occasionally need to be replaced. Alternative sensors for the APP that have been shown to show similar properties and functions include resistive, magnetic and inductive sensors.
Throttle Position Sensor (TPS)
The electrical circuitry to both the APP and TPS sensors is the same. Just like the APP sensor, the TPS sensor unit is mounted on the throttle body and converts the throttle body butterfly valve angle position into a voltage signal, which is transferred to the PCM unit. The main purpose of the TPS is to monitor whether the throttle valve or blade, is in the open position, which can be indicated by how far the accelerator pedal has been pushed down.
Furthermore, the TBS also controls how much air is flowing into an engine. For example, when the engine’s intake manifold is opened, more air will flow in, whereas a closed intake manifold will prohibit much air from flowing into the system. The engine control unit obtains information from the TPS in the form of a voltage signal to determine the throttle valve position and allow for air-fuel ratio correction and fuel cut control to be achieved. Similar to the APP unit, the TPS unit is also comprised of three components, each of which is in the form of wires.
The circuitry to the TPS unit involves this unit receiving 5 volts from the PCM unit. During movement of a vehicle, the signal delivered to the TPS is in the range of 3.5–4.7 volts; a value range that indicates that the throttle valve is in the open position.
A closed-throttle position switch informs the PCM unit that the accelerator pedal is free, which indicates that the driver has removed his/her foot from the pedal device.
References and Further Reading
Grainger R. (2008). Mazda MX-5 Miata 1.8: Enthusiast Workshop Manual. UK, Dorset: Veloce Publishing.
Erjavec J. (2010). Automotive Technology: A Systems Approach. USA, New York: Delmar Cengage Learning.
Pickerill K. (2010). Automotive Engine Performance. USA, New York: Delmar, Cengage Learning.
Hatch ST. (2012). Computerized Engine Controls. USA, New York: Delmar, Cengage Learning.
“Choosing the Right Automotive Sensor for Throttle Control” - ElectronicDesign
Disclaimer: The views expressed here are those of the author expressed in their private capacity and do not necessarily represent the views of AZoM.com Limited T/A AZoNetwork the owner and operator of this website. This disclaimer forms part of the Terms and conditions of use of this website.