Sep 13 2012
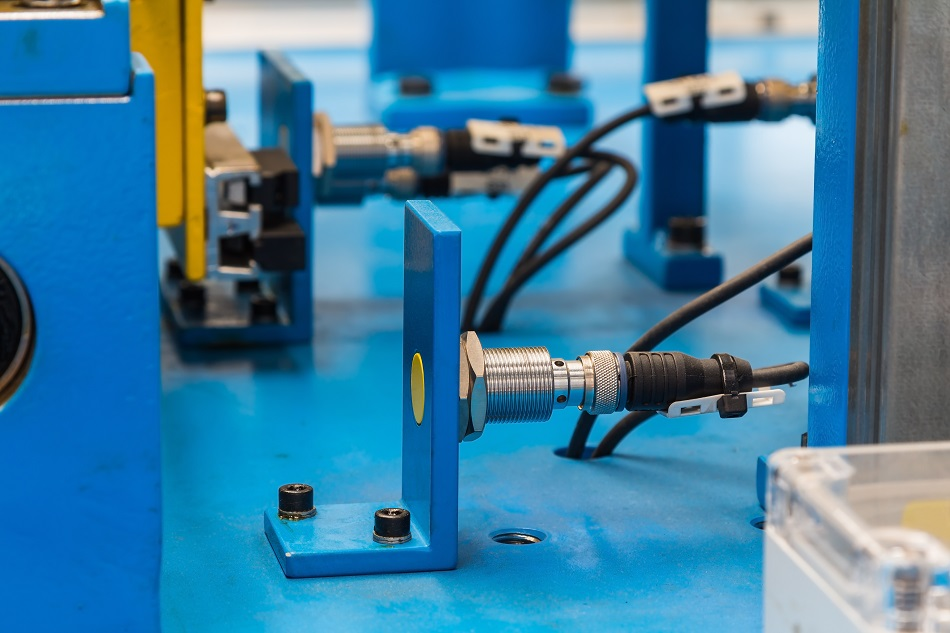
Image Credit: Matee Nuserm/Shutterstock.com
The purpose of a proximity sensor is to detect how far something is from the sensor device without having any physical contact with it. The measurement of how far an object sits from the sensor is based on a range from 0.0 to the maximum value of 1.0 in increments. The maximum distance sensed by a proximity sensor is termed a normal range.
A proximity sensor generates an electromagnetic field or uses infrared radiation to emit a beam of light followed by measurements of change in the variation of a returning signal. The two main types of proximity sensors are capacitive and inductive, though magnetic laser, photoelectric, and ultrasonic proximity sensors are also used.
Capacitive Sensors
Capacitive sensing technology can be described as a coupling mechanism that can detect proximity, displacement, and acceleration of an object. The capacitive sensor will sense the face of a conductive object (also known as a conductive target).
A capacitive sensor’s performance is based on the air gap between the sensor and the target object. The conditions between the capacitive sensor and the target are going to affect the sensor’s sensitivity. For example, in an environment contaminated with dust particles, spray fluids, or metal chips, the vacuum environment is likely to be compromised (a capacitive sensor works well in a vacuum environment).
Fundamentally a capacitive sensor consists of two metal plates with material between them, the material being air. The general idea is to have one metal plate acting as the capacitive sensor and the other metal plate being the target. The change in capacitance (i.e., the electrical property) between the two metal plates is introduced with an alternating electrical field and the change in the electrical field reflects the distance between the sensor and the target. Figure 1 is a diagram that displays the structural principle of a capacitive sensor.
Figure 1. Structural principle to a capacitive sensor. Source: Wilson J.S. (2005). Sensor Technology Handbook. UK, Oxford: Elsevier Inc.
A standard proximity sensor is made up of four parts: a coil and ferrite core, an oscillator, a circuit that behaves like a converter, and a device to deliver the output. Figure 2 simplifies the electrical pathway involved in a proximity sensor from the target through to the output.
Figure 2. Functional operation of a capacitive proximity sensor. Source: Proximity Sensors. Reference Information. Danaher Speciality Products.
In this diagram, the radiofrequency field is generated by the oscillator, shaped and manipulated by the coil and core elements to the capacitive sensor. Interaction of the target with a sensing plate occurs if the target is positioned within a certain range which forces a change in the capacitance level as a result of varying levels of density, conductivity, and humidity. Change in capacitance activates the oscillator, lowering its amplitude in response to this change, which triggers a direct electrical current to a detector element that activates the sensor output signal.
Inductive Sensors
Once the target becomes traceable by the radio frequency field, an electrical current is generated as a reflection of a change in the magnetic field and the oscillator lowers the amplitude. The amplitude change forces a change in the electrical current to a direct current wave, which is compared against the reference level forcing the output signal to activate (figure 3).
Figure 3. Functional operation of a capacitive proximity sensor. Source: Proximity Sensors. Reference Information. Danaher Speciality Products.
Targeting an Object
Identifying the target by the capacitive sensor is the most challenging stage in this process. The design idea here is to create a sensor surface that is smaller than the diameter of the target surface area so that a rated range can be achieved by the sensor. Generally, manufacturers tend to create a standardized design. The sensing range changes as a direct reflection of a change in the dimensions of the diameter of the target surface area.
For many sensors, a large air gap is required between the target zone and the capacitive sensor. To achieve this gap, an unshielded sensor is used that projects out of the body to the capacitive sensor to allow a sensing range 3 to 50 percent higher in resolution. The maximum range of the inductive sensor is a third in size compared to the diameter of the sensing face. The inductive sensor will measure a range against a mild steel target.
Sources and Further Reading
- Proximity Sensors. Reference Information. Danaher Speciality Products.
- Wilson J.S. (2005). Sensor Technology Handbook. UK, Oxford: Elsevier Inc.
- Komatinenti S, MacLean D. Pro Android 4. Proximity Sensors
This article was updated on 12th February, 2020.