The complexity of automobile systems increases each year. Manufacturers are working towards producing enhanced braking force and performance in more compact and lighter packages.
In addition, the demand for smooth, vibration-free braking systems has also increased. Smooth braking systems must be manufactured under tighter tolerances, and need to perform under extreme operating conditions. As a result, manufacturers need to carry out thorough inspection and further enhance rotor performance techniques.
Problem of Existing Braking Systems
Inconsistencies in the manufacture of brake rotors results in variations in thickness and run out. Hence, it is necessary to check and rectify these irregularities to produce a vibration-free reliable system. This can be accomplished through dynamic measurements of the rotor. A non-contact measurement probe is generally used in conventional capacitance methods to monitor the distance between the electrically grounded target and the probe.
However, rotating targets usually feature an intermittent, uncertain or nonexistent ground path that induce drift, instability, undesirable noise and minimizes the measurement accuracy.
The Solution for Braking Inconsistencies
The unique "Push-Pull" capacitance measurement system from the MTI Instruments shown in Figure 1 eliminates the need for a grounded target. It uses two probes, built into the structure, that operate simultaneously to finish the ground path. One probe pulls the current out of the brake rotor while the other pushes current in. This mechanism leads to the generation of a "clean", consistent electrical sensing path.
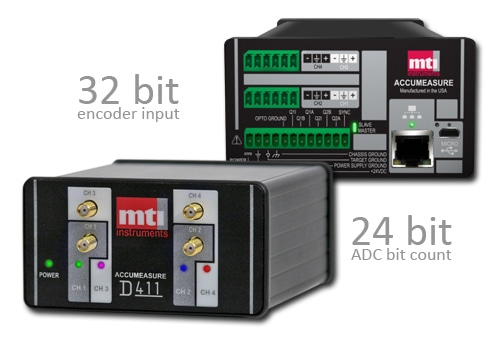
Figure 1. "Push-Pull" capacitance measurement system
Conclusion
The results of tests carried out with a standard capacitance probe were compared to those of the Push-Pull technology.
The amplifiers and fixture used in the test are shown in the Figure 2. The output of each probe was analyzed using a PC while rotating the rotor. The PC is directly connected to the digital amplifier. Figure 3 shows the results of the test. The results can also be logged in a data file and observed in real-time. The results show that the Push-Pull technology yields a much cleaner output signal. In addition, the resolution was better than 0.5 µm at a measurement range of 1.5 mm.
Other products from MTI Instruments include high precision laser and fiber-optic systems with frequency response to 500 kHz and resolution to 0.04 µin (1 nm).
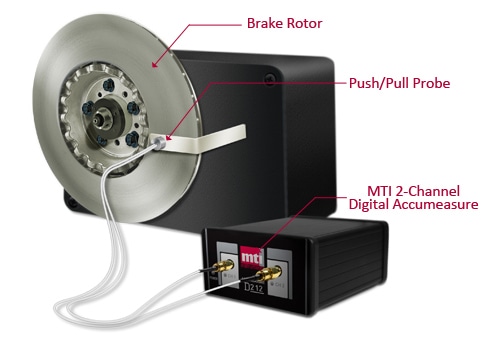
Figure 2. Amplifiers and fixture used in the test
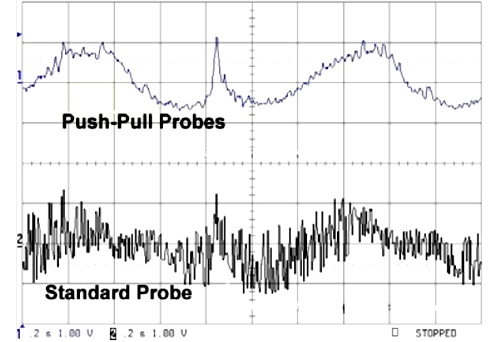
Figure 3. Results of the test
About MTI Instruments
MTI Instruments is a worldwide leader in the design, manufacture and engineering of non-contact measurement systems and sensors.
MTI’s main products consist of computerized general gauging instruments for position, displacement, thickness and vibration applications based on laser triangulation, fiber-optic and capacitance measurement technologies.
The Semiconductor Products sensor group manufactures manual, semi-automated and fully automated wafer characterization tools designed to measure wafer thickness, total thickness variation (TTV), bow, warp and flatness of semi-insulating and semiconducting materials.
MTI’s Aviation Balancing Instruments group provides state-of-the-art portable balancing and vibration analysis systems for turboprop and jet aircraft engines.
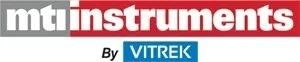
This information has been sourced, reviewed and adapted from materials provided by MTI Instruments.
For more information on this source, please visit MTI Instruments.