Since manufacturers of medical equipment encounter constant pressures to balance cost and quality, pressure sensors present developers with contradictory requirements that can result in dangerous compromises. Pressure sensors pose a common reliability challenge that force manufacturers to depend on expensive ongoing maintenance and component replacement to work around the inherent short lifetime of the sensor. However, the stakes are still higher in medical applications, where these sensors have high accuracy and reliability requirements and where component failure can lead to safety risk.
Challenges
Despite the fact that the packaging of the sensor component is important in solving this issue, it is a challenge that has, until lately, eluded sensor manufacturers. A blood analyzer system is a typical use case. While this kind of medical application may not demand the pressure sensor to be operated in high temperatures or harsh fluids, even saline solution can eventually be corrosive, and the cleaning and sterilization process usually needs repeated contact with caustic chemicals such as bleach.
The main issue is that the adhesives that are employed to make the pressure seal and protect the sensor die and related circuitry ultimately soften in the surrounding fluid. The sensor circuitry is damaged, as soon as the seal breaks, thus creating a familiar reliability failure that can be high-priced if it causes a product recall or requires regular maintenance and replacement of the sensing subsystem.
Solution
An innovative new pressure sensor packaging approach creates an eutectic die bond on ceramic substrate using a gold-tin soldering alloy for a hermetic seal even in the presence of harsh fluids. When compared to the individual melting points, a gold-tin soldering bond with an 80:20 ratio makes an alloy with a much lower melting point, thus enhancing manufacturability while still retaining the benefits of both metals in severe environments. In addition, while this gold-tin solder is more expensive than adhesive, the cost differential is small in comparison to the considerable improvement in long-term maintenance costs and reliability.
.jpg)
The MSS100 sensor from Merit Sensor Systems employs back-side entry and eutectic die attach that protects sensor circuitry for cost-effective high reliability in medical applications.
Conclusion
Checking whether the pressure media comes in at the back side or top of the sensor is an additional aspect that needs to be considered while comparing sensor packaging approaches. The circuitry must be protected from corrosion or shorts if the pressure is on the top side of the sensor. This protection is usually achieved with a protective gel. However, a gel that is stiff enough to bear corrosive fluids is generally also stiff enough to cause stress to the MEMS element.
This may lead to intolerable sensing errors in most medical applications. On the contrary, back-side entry uncovers only the eutectic die attach, glass and silicon to the pressure medium—elements that have been proven to withstand this environment—with no accuracy concerns of top-side sensors.
For medical equipment, packaging for pressure sensing applications is crucial to remove regular compromises, enhance product lifetime reliability and lower ownership cost.
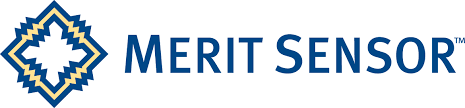
This information has been sourced, reviewed and adapted from materials provided by Merit Sensor.
For more information on this source, please visit Merit Sensor.