Table of Contents
Introduction
Flow Rate Determination
Measurement Principle
Radar Technologies
Radar Meter System
Hybrid Flow Measurement
Extended Measurement Range: Flood Sensor
Redundant Measurement for Increased Accuracy
Summary
Introduction
The radar measurement technique plays an increasingly significant role in the wastewater and water field. This is specifically revealed by the "Metering outside of the medium" trend. Flow measurement by means of radar, which allows contactless measurements, has become a key focal point. It features a broad range of applications and thus is a useful stable measurement system for several applications with part filled pipes or canals in the wastewater and water field.
.jpg)
Figure 1. Hybrid measurement system.
Flow Rate Determination
When it comes to monitoring wastewater or water volumes, flow rates determination is indispensable for many processes. However, to ensure continuous flow determination, a measurement system that enables optimal velocity detection is required for the according application. The radar measurement technique enables contactless flow velocity metering. Hence, it is perfect for applications with strong sedimentation on the bottom of the channel, or if sensors cannot be installed on the bottom of the channel or within the medium because of several reasons.
The radar metering, in contrast to other measurement systems, entails the advantage that it is largely independent from the properties of the measurement medium such as viscosity, temperature, density or conductivity. Furthermore, the microwave-based technique stands out from the crowd of other flow measurement techniques due to easy installation and low maintenance.
Measurement Principle
Radar sensors are set up outside of or above the measurement medium. A signal with a certain frequency is sent out by the radar sensor. This signal is reflected when it impinges on the water surface. Once the signal is reflected from the water surface, a frequency shift is produced. The radar sensor detects the reflected signal, which will be evaluated through the Doppler principle.
.jpg)
Figure 2. Schematic drawing: Radar measurement principle.
Wave formation on the water surface is the precondition for the radar method. The sensor measures the waves’ movement and thus the surface velocity of the water. A single velocity is selectively measured on the water surface. With the help of NIVUS’ hydraulic COSP model, it is possible to calculate the average flow velocity from selective single velocity. An additional level sensor which allows the determination of the wetted area A is used to measure the flow level. Flow Q is calculated from the wetted area A and the average velocity
as follows:
Q =
x A
Q = Flow rate
= Average velocity
A = Wetted area
Formula 1: General flow rate calculation
Radar Technologies
A difference is made between pulse radar units and continuous-wave radar units. Pulse radar units release high-frequency impulse signals at high power. The radar sensor, once reflected, receives the signal as echo. Before an echo has been received, new signals will not be transmitted.
Continuous-wave radar units (CW radar units) transmit continuous signals. Hence, reflected signals are received permanently which enables to permanently measure velocities, for example, in the wastewater and water field. Utilizing the radar technology, NIVUS depend on the latter method for flow measurement.
Radar Meter System
The standard radar metering system consists of the new NivuFlow 550 transmitter, a radar flow velocity sensor (optionally with Ex zone 1 approval) and a level sensor. Both sensors give the measured data for the transmitter which in turn calculates the flow Q by considering hydraulic models.
.jpg)
Figure 3. Complete radar measurement system: OFR radar sensor, level sensor type i-Series (left) and NivuFlow 550 transmitter.
System set-up and installation can be performed quickly and easily, because all measurement place parameters can be directly set on the transmitter. Therefore, additional hardware or software is not needed.
In a WWTP, inlet sewer flow volume and flow velocity have to be determined and logged. The measurement is used as control measurement in order to prevent flooding the treatment plant. The customer demanded a contactless low-maintenance system because of partially high dirt loads and hence sedimentation was expected on the bottom of the channel. Due to this set-up, for example, a water-ultrasonic sensor on the bottom of the channel was not desired. A radar meter was the most perfect measurement system for this measurement site, because all conditions were met.
.jpg)
Figure 4. Application example WWTP inlet sewer.
Hybrid Flow Measurement
NIVUS is the only provider who offers a hybrid measurement system for flow measurement apart from pure radar meter systems. This hybrid system is an extension of the radar measurement system. In addition to flow velocity detection using radar, the flow velocity is also detected by employing ultrasonic cross correlation. Therefore, the measurement system is supplied with the NivuFlow 7550 hybrid transmitter, two flow velocity sensors and one level sensor.
.jpg)
Figure 5. Hybrid measurement system: v-sensor 1 OFR radar sensor, level sensor i-Sensor, v-sensor 2 POA sensor, NivuFlow 7550 hybrid transmitter.
The transmitter completes or combines the measured flow velocities by achieving the average flow velocity. Depending on the filling level and the sensor installation positions, there are two important applications for the hybrid meter system: hybrid metering as redundant measurement to improve accuracy and hybrid metering as an extended measurement range, for example, during flood conditions.
Extended Measurement Range: Flood Sensor
Standard discharge measurement situation:
The ultrasonic wedge sensor is fixed firmly on the pipe ceiling. In this system configuration, typically only the radar sensor measures the flow velocity.
.jpg)
Figure 6. Hybrid measurement system; Standard discharge measurement situation.
High level measurement situation:
Set-up slightly out of the channel crest, the ultrasonic sensor starts to measure shortly before the flood situation is reached based on the installation point. In this situation, the ultrasonic sensor and the radar sensor measure parallel. The example shown in the below image has a very small range of measurement because the ultrasonic sensor is fixed firmly to the ceiling and starts to measure only before the dead zone is reached. Depending on the local flow velocities identified by the ultrasonic sensor, the hydraulic model can be improved for the entire measurement situation.
Flood measurement situation:
Once the sensor’s dead zone is reached, measuring is not possible any more with the radar sensor. From this point on, the ultrasonic sensor completely takes over the measurement task.
.jpg)
Figure 7. Hybrid measurement flood condition.
A reliable measurement is assured over the entire range of measurement because the level during such situations is measured by means of the ultrasonic sensor’s pressure cell.
Redundant Measurement for Increased Accuracy
In this hybrid measurement approach, the ultrasonic sensor is set-up below the minimum filling level. Therefore, a redundant flow velocity measurement using ultrasound is performed continuously in parallel to radar metering. Local velocities in up to 16 layers are detected by the ultrasonic cross correlation sensor. It is possible to develop an accurate hydraulic model of the measurement situation in combination with the flow velocities established by the radar sensor. Based on this model, the flow rates and the average flow velocity can be determined very accurately.
.jpg)
Figure 8. Redundant flow metering.
Summary
In the past few years, flow metering employing radar systems is increasingly becoming popular. Radar measurement systems stand out for a broad range of uses in numerous part-filled applications. Due to the ease of maintenance and contactless measurement, radar metering is specifically suitable for applications that feature sedimentation or dirt loads even if it is not possible to set-up sensors inside the medium. The use of radar technology for flow measurement is accomplished through the options offered by hybrid measurement systems, thanks to extending the measurement or increasing the accuracy.
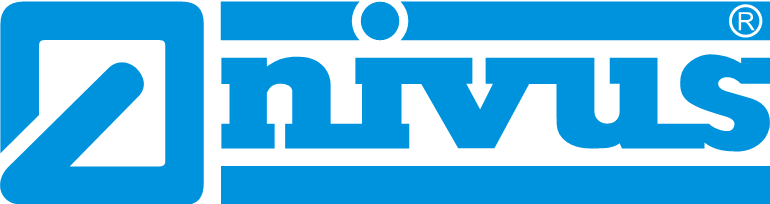
This information has been sourced, reviewed and adapted from materials provided by NIVUS GmbH.
For more information on this source, please visit NIVUS GmbH.