Slow speed rotating machinery (typically, less than 300 RPM) is commonplace in many industrial applications, for example; cooling towers, hydro-electric turbines and wind power generation. To ensure this type of machinery and plant is functioning at optimal levels it’s essential to measure vibration, as much as it is a critical requirement for standard speed machinery applications.
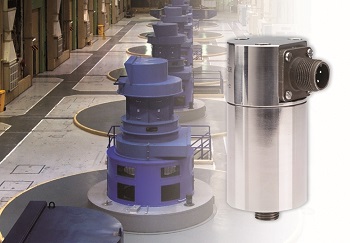
In all cases the focus should be; understand the dynamic behaviour, establish a baseline vibration performance, and then to detect the early onset of failure in rotating parts which if left un-checked has the potential to result in more serious damage affecting overall performance.
Whilst the use of accelerometers is common place on standard speed machinery (i.e. 1500 RPM) this becomes problematic at lower speeds as the absolute accelerations measured are much smaller in value for similar vibration displacements. Condition monitoring specialists SENSONICS have recognised the need for a sensor which can meet these requirements and has developed the VEL/GLF, a new LOW FREQUENCY VELOCITY VIBRATION SENSOR.
The VEL/GLF is an electro dynamic sensor which offers a superior performance compared to piezo-electric devices by combining high measurement sensitivity with a frequency response down to 0.5 Hz and is therefore ideally suited to measuring velocity vibration on equipment with speeds below 300 RPM.
The sensor offers a standard IEPE type interface to enable easy integration with existing plant protection and monitoring equipment. Furthermore, the VEL/GLF provides advantages over traditional piezo-electric based velocity vibration sensors which are susceptible to many forms of interference in low frequency applications that can result in spurious readings and alarms.
Typical causes include; base strain effects due to temperature changes amplified through the internal signal processing, high frequency and high g vibration events caused by auxiliary machine items resulting in transducer saturation and also mains voltage interference due to a combination or poor local plant earth and insufficient transducer internal isolation.
Thanks to its robust design, the VEL/GLF combats these effects, offering high noise immunity due to the low impedance electro dynamic nature of the sensor assembly. In addition to the filtering of high frequency events and since no electronic integration is required, the design is immune to the saturation problems that impair the reliability of piezoelectric devices.
Typical applications for the VEL/GLF will be found in cooling towers, hydroelectric and wind power generation, slow speed pumps and also structural monitoring.