In position sensitive detectors (PSD) the photocurrent is distributed between different cathode and anode contacts which allows determining the focus point of illumination on the sensor area. This is primarily used for monitoring relative changes in the position of a light spot on the detector.
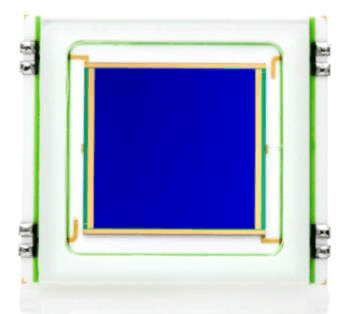
New application of First Sensor PSDs in the NuSTAR x-ray satellite
The x-ray satellite NuSTAR, launched in June 2012, is equipped with three DL400 PSDs from First Sensor. The DL400s area duolateral, two-dimensional PSDs with 400mm² active area. They are used for continuous alignment of the telescope optics with respect to the sensor unit. Optics and sensors in x-ray telescopes are separated by are large distance due to the long focal length of x-ray lenses. The 10m deployable mast in the NuSTAR satellite is characterized by low weight and low costs, yet it lacks the required buckling resistance for an optical system. Tilt and torsion of the optics with respect to the sensor are therefore monitored four times each second by three lasers. They are mounted to the optics unit and aligned to the PSDs which are placed on the sensor base. Every single DL400 detector has been measured and tested extensively by engineers of the Jet Propulsion Lab. Six out of seven components have been qualified for the highest demands of space application. A detailed description of the integration of First Sensor PSDs in the NuSTAR project can be found in the June 2012 issue of „IEEE Sensors Journal“ (Volume: 12, Issue: 6, Pages: 2006 – 2013).
Design
A PSD works like a normal photodiode where no circumferential surface contact is used, but several contacts at the edges of the device. For a one dimensional PSD an elongated photodiode is used being contacted only at the two narrow sides. The photocurrent, which is generated at a specific position by a small light spot, spreads over the detector area to the contacts. The resistance of the surface current is proportional to the distance; the current splits according to Kichhoff’s rules. The challenge in design and manufacturing of PSDs is to achieve both high linearity and high spatial resolution. Therefore a sophisticated technology is used for achieving a high and homogeneous surface resistivity over the whole detector area. Additionally, the optical area is optimized for a specific wavelength by an anti-reflective coating.
Spatial Resolution
One of the most frequently asked question regarding PSDs concerns the achievable spatial resolution. Here it has to be distinguished between absolute and relative accuracy. The absolute accuracy is limited by the homogeneity of the surface resistivity within the detector area. Depending on the application sometimes individual correction maps of each PSD need to be created.
Relative changes can be detected with much higher accuracy. The resolution is limited by stability, shape and halo of the light spot as well as the measurement equipment. It should be noted that the ratio of the currents equals the integrated center of illumination on the detector. A change of the spot shape, e.g. by fluctuation of laser modes, might have an impact on the measurement result. For resolutions in the sub-micron range there are high demands on the quality of the measurement equipment: For monitoring a change in spot position of 1μm on a 10mm PSD the currents need to be measured with accuracy better than 0.01%.
This can be achieved e.g. by phase sensitive amplifiers (lock-in amplifiers) in combination with pulsed light sources. Other limitations to the achievable resolution are given by the changes in dark current due to temperature drifts of the die or local heating due to the energy of the light spot. High thermal exposure levels due to illumination should be avoided in general.
Two dimensional PSDs
The principle of 1D-PSDs suggests using four instead of two electrodes on the surface to achieve 2D resolution. Unfortunately, those elongated contact strips also work as a current bridge. In case the current is generated on the right edge of such a PSD the charge carriers will not only flow along the detector surface but will also take a short cut over the right contact to reach the upper and lower electrodes. This leads to strong nonlinearities in the spatial resolution especially on the edges of the active area.
Therefore a “duolateral” design with two contact strips on the front side (anode: left, right) and two orthogonal contacts (cathode: top, down) on the back side of the die. The limits of relative and absolute spatial resolution in the duolateral design are similar to a 1D-PSD. First Sensor offers 2D-PSDs up to 20mm x 20mm active area, 1D-PSDs in 3.5mm and 7mm length, as well as customized sensor solutions.
Comparison with CMOS/CCD image sensors
For analyzing the position of a light spot an image sensor based on CMOS or CCD technology can be used as well. By the implementation of more or less complex algorithms also background signals can be reduced. Still, the costs for electronics and design are much higher compared to a PSD. Furthermore, even high resolution cameras will usually not show the same performance as a PSD regarding the lateral resolution.
Comparison with quadrant photodiodes
Quadrant photodiodes (QPs) are segmented in four quadrants with each giving its own photocurrent. QPs are used for precise alignment of a light spot on the center of the detector: The spot or detector is shifted until all four quadrants deliver the same photocurrent and equilibrium is achieved. On the other hand, a QP only allows an accurate adjustment to the center of the device. The intensity profile of a spot is in general very nonlinear, in case the spot moves out of the center one cannot deduce the amount of misalignment from the ratio of the currents. Still in contrast to PSDs, a quadrant detector is easier to produce and shows faster response speed due to a high conductive detector area. First Sensor also develops and manufactures a large variety of quadrant photodiodes in various sizes, packages and optimizations for different applications.
Contact First Sensor to help you find the optimal PSD or QP solution for your application.