Providing an accurate, simple, economical solution to the measurement of natural gas for industry, the ST75A and ST51A Thermal Flow Meters from Fluid Components International (FCI) offer all the advantages of thermal mass flow sensing technology including accuracy, reliability, low maintenance, long life and low-life cycle costs.
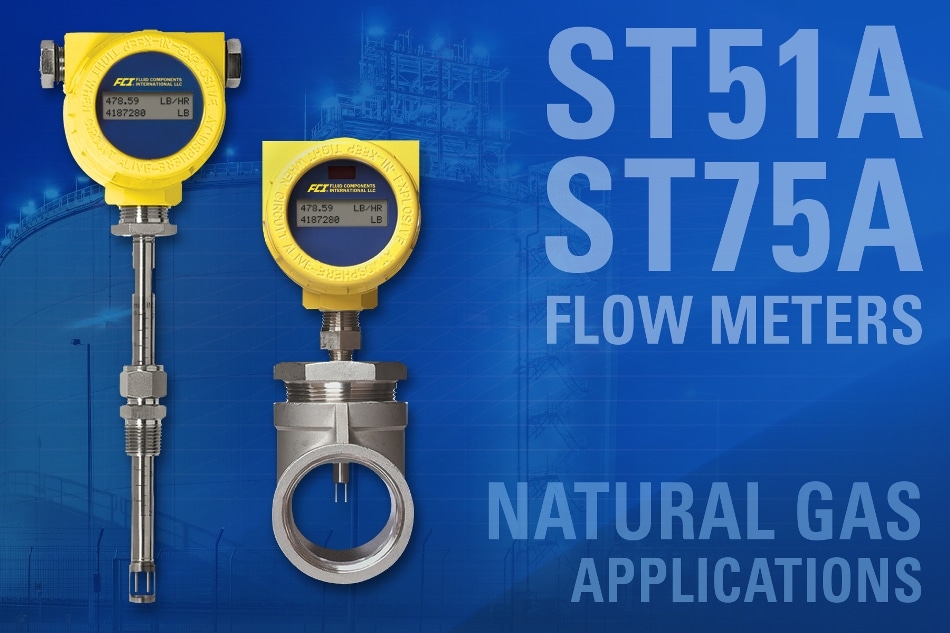
Natural gas is the feed stock source for butane, ethane and propane, as well as a component in the production of ammonia and methanol. The production of antifreeze, fabrics, fertilizer, plastics and pharmaceutical depend on it. Industrial process and manufacturing equipment requiring or involving natural gas include burners, boilers, co-gen engines, dryers, feed lines, generators, HVAC systems, ovens, sub-metering systems and more. After industry, electric power generation is the next largest consumer of clean-burning natural gas.
FCI’s inline ST75A Flow Meter is ideal for the measurement of natural gas, other industrial specialty gases and air in line sizes from 0.25 to 2 inches. It features a solid-state thermal dispersion mass flow sensing element with platinum RTD’s in equal mass thermowells for years of accurate, trouble-free service. It can be calibrated to measure gases over a wide flow range from 0.04 to 559 SCFM (0.07 to 950 NCMH), depending on line size.
For variable plant demand cycles due to small batch or other continuous process production requirements, the ST75A Flow Meter is factory preset to 100:1 turndowns. It features highly dependable accuracy to ±1% of reading with ±0.5% repeatability. Engineers and technicians can depend on this meter for precise flow control of gases to ensure high quality end-products from batch or continuous processes or in manufacturing operations.
The rugged design of the ST75A Meter’s flow element features no-moving parts for superior reliability. This unique design provides extra confidence where process safety is a big concern with other types of meter technologies, which rely on movable parts that can break over time in high turndown applications.
The Model ST75A flow meters are designed with a choice of mounting configurations.
They feature a full digital display and are also available with optional transmitter remote mounting capabilities for hazardous plant environments. The remote transmitter can be mounted up to 100 feet (30 meters) away from its thermal mass flow sensor in piping or ductwork and connected via two 0.50-inch FNPT or M conduit connections.
The ST75A flow meter’s fully scalable dual 4-20mA standard outputs are user assignable to flow rate and/or temperature and a 0-1kHz pulse output of total flow. Modbus or two-way HART bus communications are available. The instrument can be ordered for input power with either 18 to 36 Vdc or 85 to 265 Vac
The ST75A Flow Meter withstands process temperatures from 0 to 250°F (-18 to 121°C). It operates at pressures up to 240 psig [16.5 bar (g)] with a standard t-fitting (NPT female) process connection. With a tube process connection for 0.25 inch lines, the meter withstands 600 psig [41 bar (g)].
For larger natural gas line sizes of 2.5 to 24 inches (63 to 610 mm), the insertion style ST51A Flow Meter is designed for accurate, repeatable flow measurement of natural gas, biogas, air, compressed air or nitrogen. It also features FCI’s proven no-moving parts thermal dispersion mass flow sensing element with standard accuracy of ± 2% reading, ± 0.5% full scale. It measures flow over a range of 0.3 to 400 SFPS (0,08 to 122 MPS).
The full-featured ST51A’s electronics are housed in a rugged, IP67 rated enclosure and the entire instrument includes a SIL rating with global HazEx approvals. The instrument comes standard with dual 4-20 mA, NAMUR NE43 complaint outputs and a 500 Hz pulse output. It also features Modbus or HART communications. The transmitter/electronics can be integrally mounted with the flow element (probe) or be remote mounted up to 100 feet (30 m) away.
Fluid Components International is a global company committed to meeting the needs of its customers through innovative solutions for the most challenging requirements for sensing, and measuring flow, pressure and temperature of gases.