Future human space exploration requires a safe living environment for astronauts. That is why a robust structural health monitoring (SHM) process is imperative to ensure equipment safety, particularly for the inflatable habitat structures that are the most cost-efficient solution to the astronauts’ living space needs.
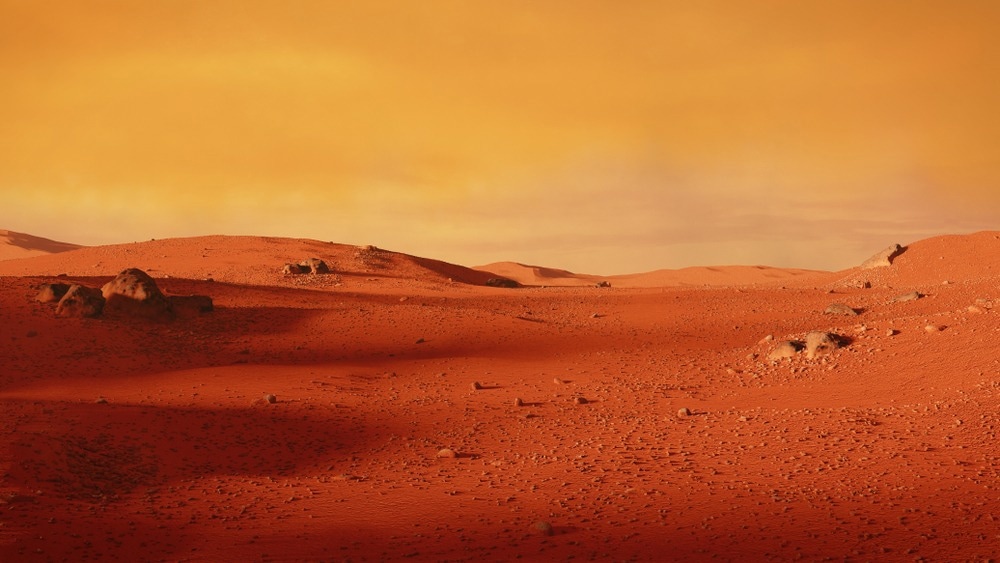
Image Credit: Dotted Yeti/Shutterstock.com
A novel approach is moving away from conventional SHM testing methods in favor of using sensors embedded in the flexible structural restraint webbing layers. The sensors can collect data on stress, strain, creep, and impacts of micro meteorites throughout the inflatable habitat’s lifecycle. The embedded fiber optic sensors were woven into VECTRAN™ webbing and then later integrated into an inflatable test article that was tested at NASA Johnson Space Center for potential use in future inflatable habitat structures for NASA Lunar Gateway and Mars missions. [1]
New approach sought for structural health monitoring in space
In 2007, Bally Ribbon Mills (BRM) began working with Luna Innovations, Inc., an American developer and manufacturer of fiber-optics- and terahertz-based technology products for aerospace. Luna’s NASA contact had suggested the partnership to provide a demonstration sample that could show the capabilities of Luna’s technology, which focuses on integrating high-definition fiber optic sensors (HD-FOS) into a three-dimensional woven carbon structure used in composites. The project was undertaken as part of the Small Business Innovation Research (SBIR) program, a competitive awards-based research and development program that helps small businesses explore their technological potential and provides the incentive to profit from its commercialization. [2]
The project aimed to demonstrate the integration of optical fiber sensing technology into composites to monitor the vacuum assisted resin transfer molding (VARTM) process. The team designed a composite cantilever beam with three-dimensional carbon fiber reinforcement that was fabricated with embedded optical sensing fibers. Bally Ribbon Mills wove the carbon fiber preform with warp, fill, and Z-axis reinforcing fiber. During the preform weaving process, BRM added optical fiber bobbins to the weaving loom and determined the necessary processes to integrate fiber optic strain sensors into the weave.
BRM successfully wove the material and passed it along to Luna. Fast-forward 15 years, and Luna came back to collaborate with BRM on a NASA multi-phase grant award examining whether the embedded sensor technology could survive all the required manufacturing processes for use in inflatable habitat structures being developed for upcoming space missions. During this phase, the focus is on integrating fiber optic sensors into Vectran webbing for inflatable space habitat SHM. The approach uses sensors to capture data throughout an object’s lifecycle.
The data collected from “smart webbing” could be used for many applications:
- Optimizing process control by using data to increase quality, efficiency, and effectiveness.
- Centralizing reporting by characterizing operational norms and preventing false alarms, as well as gaining the ability to access information from anywhere.
While the space habitat SHM application focuses on strain measurement, examples of the kind of data that might be measured include:
- Strain
- Wear and tear, fatigue, aging, structural health, safety
- Temperature
- Material joints, process control, safety
- Intrusion detection, process control, safety
- Vessel Pressure
- Flow rate, quality (contamination, transmitted material formulation), volumes
For the space habitat SHM application, the long-term goal was to be able to measure stress, strain, and temperature, as well as pinpoint the location of important events. For example, if a micro meteorite hits the shell fabric and causes a point source stress, scientists could know where it hit and be able to gauge the potential for failure.
During this project, BRM integrated Luna fiber optic sensors into Vectran webbing. The BRM materials served as woven optical carriers, which are critical in applications that experience high strain. Carriers add reinforcement to fiber optic sensors and prevent high strain from being transferred directly to the fiber. Sensors are woven into the carrier and then embedded into a material. The carriers serve as component parts in the eventual construction of assemblies that capture and transmit information to a downstream computing technology. The weaving technology enables the measurement and conversion of information to knowledge and/or action.
The resulting benefits include the ability to take corrective action based on improved monitoring capability; the actuation of human/machine involvement; the transformation of connected objects; and ultimately the fuller automation of manufacturing processes, and the integration of non-destructive inspection tools.
Overcoming webbing manufacturing process challenges
Manufacturing webbing with embedded sensors comes with two main challenges. The first is ensuring the sensor is not damaged during the weaving process. A loom’s primary machine motion manipulates the warp and weft yarns in an alternating pattern and exerts high tension and abrasion forces on the yarn. The sensor must also survive the same motions. BRM minimized the effects of the weaving processes on the sensor by placing it in a specific location within the weave structure where the sensor’s interaction with adjacent yarns is lessened. The sensor is constructed of a fiber optic glass core with a protective polymer coating. This fiber is relatively brittle and will be damaged when conforming to a tight radius. The allowable radius varies based on the diameter of the core fiber optic material, but the benchmark is ½-inch radius. Therefore, during the weaving process BRM had to minimize bending radii of the sensor to prevent damage.
The second challenge is to ensure that the weave design is precise enough to place sensor ingresses and egresses in the proper locations within the surface of the weave structure. Weaving is a process with many variables and only moderate controls; it is not possible to achieve metal machine tolerances. This means there is always a bit of trial and error when dealing with the integration of a sensor in a specific location. In this case, the BRM team wove start-up samples based on a benchtop analysis of weave design, checked the samples after weaving, and then made adjustments to ensure accurate compliance with sensor location specifications.
Testing the sensor for continuity
Luna Innovations tested the fiber optic sensors woven into the flexible structural restraint layer webbings on an inflatable test article with a diameter of 0.61 meters (2 feet) fabricated from Vectran, a manufactured filament fiber with a liquid-crystal polymer chemistry. Experiments successfully demonstrated creep sensing, pressure sensing, and detection of damage location and magnitude. For example, the Luna team performed tests simulating micro meteoroid and orbital debris damage on panels of instrumented webbings, which demonstrated successful detection of the event and location.
A one-third scale, 2.74 meter diameter (9 feet) inflatable with embedded structural health sensors was used for creep and burst testing at NASA’s Johnson Space Center. A habitat containing the smart webbing was inflated and measurements are being recorded at regular intervals for a total period of about 2 months. Measuring the long-term creep of the habitat system is important to the safety and viability of the inflatable habitat program. All materials, when exposed to stress over time, will creep or elongate. Vectran itself resists creep, but it is difficult to calculate the actual amount of creep in the habitat system because of the wide variety of materials and different layers being used in its construction.
NASA is performing the testing to validate the bench-top engineering and design of the habitat’s structural components
While the goal is to complete the project by 2023, the need to orchestrate raw material supply, component procurement, manufacturing, assembly, testing, test-facilities scheduling, and funding means that timing predictions are definitely subject to change. Based on previous success with the prior phases and benchmarks, BRM is currently contracted to produce the next set of “sensorized” webbing.
“BRM’s work in developing the manufacturing processes necessary to integrate fiber optic strain sensors into the fabric weave was key to our success and is helping to move the technology into the future,” says Matthew Davis, Luna’s R&D Director, Lightwave Division. “We rely on their skills and are excited about working in partnership with them to extend the innovative approach into other SHM applications.” One example is a Navy Phase II SBIR effort in which Luna and BRM are integrating fiber into the harness a fighter pilot might wear.
As Davis explains, “Webbing textiles are critical to many personnel safety systems in U.S. Navy aircraft, but there are currently no viable non-destructive techniques to detect when the load strength has degraded to an unsafe level. With BRM’s assistance, we are integrating this technology, which enables accurate assessment of the load capabilities for nylon, polyester, and Kevlar structures during their service life.”
Structural health monitoring is critical for the future
Ensuring the safety of long duration human habitation in space or on other planets will depend on structural health monitoring. The new sensor-based technique for monitoring the health of the flexible soft goods restraints on inflatable living structures shows great promise. If the embedded sensing technology proves to be successful, it could be included in future space mission habitation structures, including the Lunar Gateway or Mars missions.