Recent advances in electromyography (EMG) sensor technology have drawn attention because the technology enables stable, long-term control of wearable robots without being impacted by perspiration or dead skin.
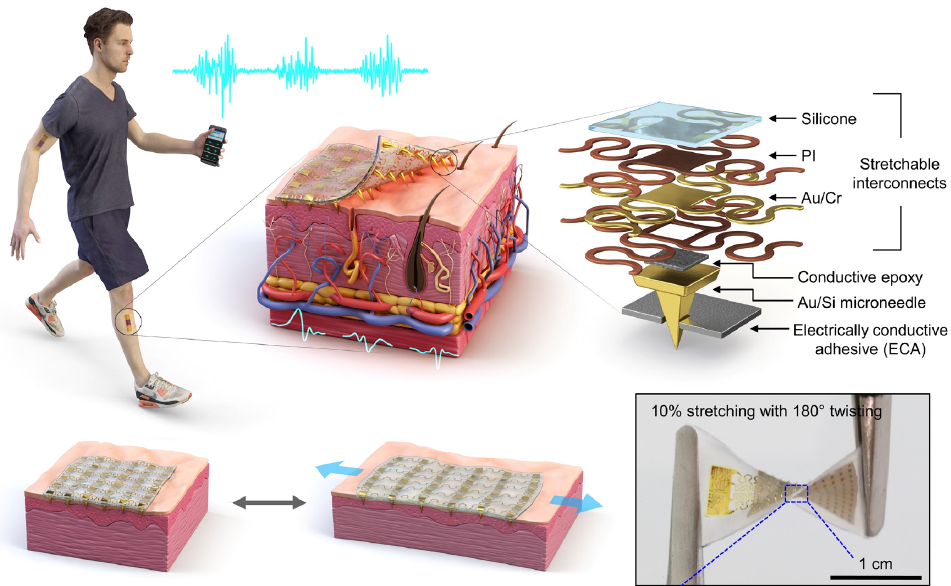
Design and working concept of the Stretchable microNeedle Adhesive Patch (SNAP). (A) Schematic illustration showing the overall system configuration and application of SNAP. (B) Exploded view schematic diagram of a SNAP, consisting of stretchable serpentine interconnects, Au-coated Si microneedle, and ECA made of Ag flakes–silicone composite. (C) Optical images showing high mechanical compliance of SNAP. Image Credit: KAIST
A range of rehabilitation therapies for the elderly and individuals recuperating from stroke or trauma employ wearable robots as medical equipment.
On January 23rd, 2024, a collaborative research team headed by Professors Jae-Woong Jung of the KAIST School of Electrical Engineering (EE) and Jung Kim of the KAIST Department of Mechanical Engineering (ME) announced that they had effectively created a stretchable and adhesive microneedle sensor that is capable of high-level electrical physiological signal detection that is independent of the user’s skin condition.
To utilize wearable robots in rehabilitation therapy, they need a wearable electrophysiological sensor that provides accurate electromyography readings. Unfortunately, the signal quality of current sensors frequently deteriorates over time and is heavily influenced by the skin conditions of the user.
Furthermore, because the contact surface cannot keep up with the skin's deformation, the sensor's higher mechanical hardness produces noise. The dependable, long-term control of wearable robots is restricted by these flaws.
However, because the newly developed technology uses a stretchable, adhesive conducting substrate integrated with microneedle arrays that can easily penetrate the stratum corneum without causing discomfort, it is anticipated to allow for long-term and high-quality EMG measurements.
The sensor’s exceptional performance is expected to enable stable control of wearable robots for an extended duration, irrespective of the wearer's fluctuating skin conditions, and eliminate the requirement for a preparatory step involving the removal of perspiration and dead skin cells from the skin's surface.
The researchers integrated microneedles into a soft silicon polymer substrate to create a stretchable and adhesive microneedle sensor. The high electrical resistance stratum corneum is penetrated by the hard microneedles.
Because of this, the sensor can efficiently reduce skin contact resistance and produce electrophysiological signals of excellent quality even in the presence of contamination. Simultaneously, the adhesive and soft conducting substrate can conform to the surface of the skin, allowing it to stretch with the wearer’s movements. This minimizes movement noise and ensures a comfortable fit.
The research team used a wearable robot in a motion assistance experiment to confirm the new patch's usability. The microneedle patch was affixed to the user’s leg so that it could detect the electrical signals produced by the muscle. The wearable robot was then able to assist the wearer in lifting a heavy object more easily because the sensor had transmitted the intention it had detected.
The developed stretchable and adhesive microneedle sensor can stability detect EMG signals without being affected by the state of a user’s skin. Through this, we will be able to control wearable robots with higher precision and stability, which will help the rehabilitation of patients who use robots.
Jae-Woong Jung, Professor and Lead Researcher, KAIST
The study, authored by co-first authors Heesoo Kim and Juhyun Lee, Ph.D. candidates in the KAIST School of EE, was published in Science Advances.
The National Research Foundation of Korea's Bio-signal Sensor Integrated Technology Development Project, the Step 4 BK21 Project, and the Electronic Medicinal Technology Development Project provided funding for this study.
Journal Reference
Jung, J., et al. (2024) Skin-preparation-free, stretchable microneedle adhesive patches for reliable electrophysiological sensing and exoskeleton robot control. Science Advances. doi.org10.1126/sciadv.adk5260.