Apr 23 2015
The University of Tennessee Medical Center and DeRoyal Industries are partnering to bring an innovative supplies tracking system with the potential to revolutionize efficiency and patient safety in the operating room.
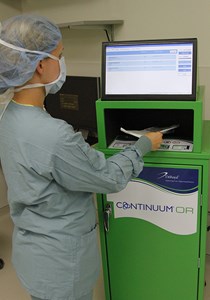
The system, Continuum® OR, created by DeRoyal and tested and refined at the medical center, uses radio frequency identification (RFID) technology to develop surgery procedure supply lists specific to each surgeon (doctor preference cards), improve inventory management and supply tracking, and enhance quality care.
"As in most facilities, the tracking of supplies was primarily a manual system often performed by clinical staff," said Brian C. DeBusk, Chief Executive Officer at DeRoyal Industries. "The new system serves to automate and drive accurate doctor preference card maintenance in a way that the manual process never could."
The average rate of items collected for a surgical procedure that are not used has been estimated to be as high 70 percent. As a result of the collaboration the medical center has seen improvements to operating room efficiencies and patient safety.
"Surgical supplies specifically associated with a surgical case are automatically tracked to the patient," said Becky Ashin, vice president of the Advanced Orthopaedic Center at The University of Tennessee Medical Center. "The orthopaedic operating rooms recognized a 99 percent read rate of supplies used in every case by putting supply packaging into this specially designed container. This allows us to accurately track supplies, reduce traffic in and out of operating rooms to retrieve needed supplies and improve recycling by separating bio hazardous waste,"
Ashin noted the next step is to expand the Continuum® OR project through the remainder of the year to 30 additional operating rooms. UT Medical Center also will begin tracking implants and instrument trays via RFID. The ongoing program will expand as additional benefits of having tagged supply items are identified.