By Samudrapom DamReviewed by Susha Cheriyedath, M.Sc.Updated on Nov 6 2024
Piezoelectric sensing is a popular sensing method that utilizes the piezoelectric effect to efficiently measure changes in dynamic forces like force, acceleration, or pressure by converting them to an electrical charge. Piezoelectric sensors convert these applied physical parameters into electrical signals without an external voltage/current source. These sensors are suitable for everyday objects as they are small and highly sensitive.1,2
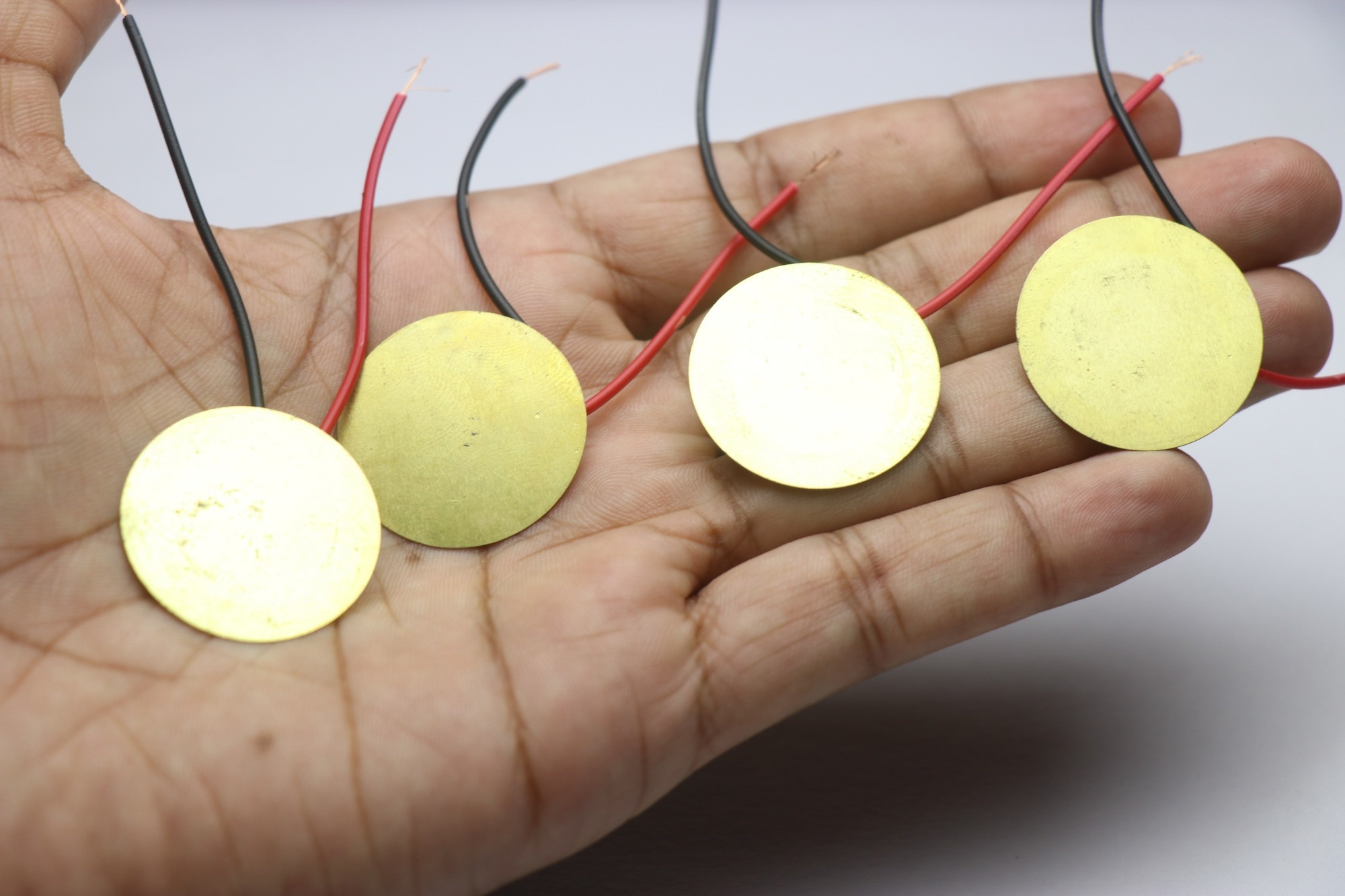
Image Credit: Pixel Enforcer/Shutterstock.com
Functional Principle
Piezoelectric sensors operate on the principle that certain materials can generate an electric charge in response to mechanical stress—a phenomenon known as the piezoelectric effect. This effect enables sensors to detect and measure changes in pressure, acceleration, and force, translating them into an electrical signal.
Piezoelectric materials, like crystals such as barium titanate and ceramics like lead zirconate titanate, are commonly used in these applications due to their sensitivity and responsiveness.
Two main types of pressure sensors—mechanical and electrical—are typically employed to measure piezoelectric effects:
-
Mechanical Sensors: These sensors incorporate a sensing element called a diaphragm, along with a rod, a three-terminal resistor (acting as a voltage divider), and a direct current voltage source. When pressure is applied, the diaphragm displaces the rod, which then activates the potentiometer. This interaction generates an output voltage proportional to the applied pressure.
-
Electrical Sensors: In this type, the diaphragm itself, typically made of a piezoelectric polymer such as polyvinylidene difluoride (PVDF), acts as both the sensing and transducing element. Unlike mechanical sensors, this setup directly converts the applied pressure into an electrical signal, bypassing the need for a potentiometer. This configuration allows for a more direct and simplified measurement process.
To accurately measure the piezoelectric effect, it is essential to understand how the piezoelectric crystal responds under stress. When subjected to mechanical force, the crystal exhibits an electric dipole moment due to the alignment of dipoles within its lattice structure. This polarization, typically measured in coulombs per cubic meter (Cm/m3), reflects the extent of dipole movement within the unit cell.
As mechanical stress reconfigures the dipole alignment in the crystal, it leads to a change in polarization, which is observed as piezoelectricity. By measuring these changes, piezoelectric sensors can effectively detect and quantify applied forces and pressures, making them highly valuable for applications requiring precision force measurements.
Sensor Technology: From Basics to Breakthroughs
Applications
Piezoelectric sensors are invaluable in a wide range of industrial applications, particularly for precise measurements in dynamic conditions and structural health monitoring. Key applications include.3,4
Pressure Sensors
Piezoelectric pressure sensors are ideal for measuring dynamic pressure changes, offering greater reliability and precision compared to traditional electromechanical sensors. These sensors excel in high-frequency response and can convert mechanical signals to electrical outputs directly, eliminating the need for mechanical components like diaphragms or bellows, making them a preferred choice in applications that require rapid, accurate pressure measurements.3
Engine Knock Sensors
In gasoline engines, uncontrolled detonation can cause severe damage, particularly under adverse conditions. Piezoelectric knock sensors detect the onset of detonation, giving engine control systems the opportunity to make real-time adjustments to prevent engine damage. By allowing these adjustments, piezoelectric sensors help maximize both engine efficiency and longevity.3
Sonar Equipment
SPiezoelectric transducers play a crucial role in sonar equipment, which relies on ultrasonic signals in the 50–200 kHz range for navigation and detection. The high power density and suitable frequency response of piezoelectric sensors make them ideal for transmitting and receiving these ultrasonic "pings." For example, a compact 4-inch transducer can handle more than 500 watts, enabling it to send powerful acoustic signals from a small device.3
Structural Health Monitoring
In structural health monitoring, piezoelectric sensors provide early warnings of potential issues, from micro-cracks in bridges to loose joints in aircraft. In electromechanical impedance (EMI)-based monitoring, piezoelectric sensors are embedded into or attached to the structure. They convert the mechanical response of the structure into an electric signal that reflects its current health. This signal is then processed to identify, locate, and characterize any damage.
Another method uses guided wave propagation, which is particularly valuable in large, critical structures like pipelines, aircraft, and pressure vessels. Here, piezoelectric sensors transmit and receive guided waves using modes like impact detection, thickness mode, pulse-echo, and pitch-catch to detect changes in the structure. Each mode is optimized for different types of damage detection, ensuring robust and reliable monitoring even in harsh environments.4
A Guide to Industrial Sensors and Automation Applications
Recent Advances
Flexible piezoelectric sensors offer exciting potential for biomedical devices, wearables, and electronic skin, but using these sensors for respiratory health monitoring brings specific challenges, such as achieving the correct level of sensitivity.5
A study in Sensors and Actuators A: Physical tackled this issue with a flexible, bionic-inspired piezoelectric sensor modeled after the fish lateral line. This design allows the sensor to wrap around cylindrical surfaces and detect forces as low as 0.0005 N, thanks to the piezoelectric properties of PVDF and its specialized structural design. The sensor showed impressive sensitivity at 0.24 V/N, with a fast response time of 4 milliseconds and strong repeatability over 4000 cycles.
This bionic sensor is fine-tuned to monitor various respiratory states, such as deep breaths, coughs, and even apnea, thanks to a carefully designed circuitry setup. This level of detail opens up real possibilities for using it as a wearable device in respiratory health applications.5
However, high-performance piezoelectric sensors often face limitations in flexibility due to material brittleness. Current manufacturing processes, like high-temperature sintering, also make it tough to produce these sensors on flexible substrates.6
An alternative approach, highlighted in a recent Nano Energy study, used 10 nm barium titanate nanocubes self-assembled on glass fiber fabric (GFF). This method avoided high temperatures, maintaining the GFF’s flexibility and mechanical strength. These sensors demonstrated high sensitivity (101.09 nA/kPa and 3.31 V/kPa) across a 0–10 N force range and a response time of just 19 milliseconds. Additionally, they maintained performance after 3000 bending cycles, showcasing the potential to recognize patterns, such as handwriting or keyboard use.
On the industry side, companies like Morgan Advanced Materials, Honeywell International Inc., and APC International Ltd. are at the forefront, pushing the boundaries of piezoelectric sensor technology. Morgan is enhancing sensor materials for tougher, longer-lasting performance; Honeywell focuses on integrating sensors into healthcare and industrial devices; and APC is developing flexible, customized sensors for wearables. These innovations keep them competitive across sectors, from medical devices to consumer electronics.
Future Outlook
All in all, piezoelectric sensors have become indispensable across applications like structural health monitoring, engine knock detection, and wearable devices. Moving forward, R&D efforts will need to prioritize advancements in flexibility, sensitivity, and durability to keep pace with expanding demands.
The integration of advanced materials and nanotechnology holds particular promise, opening up the possibility for innovative sensor designs tailored to flexible electronics and other emerging applications. With technology advancing rapidly, piezoelectric sensors are set to be key players in the next generation of sensing and measurement solutions.
Advancements in Sensor Technology: What to Expect by 2030
Reference and Further Reading
- Kim, K., Kim, J., Jiang, X., Kim, T. (2021). Static force measurement using piezoelectric sensors. Journal of Sensors, 2021(1), 6664200. DOI: 10.1155/2021/6664200, https://onlinelibrary.wiley.com/doi/full/10.1155/2021/6664200
- Lin, G., Peng, W., Gao, J., Wahlen, A., Tong, Z. (2023). Functional naturally derived materials to improve the environment: Chemical structures, modifications, applications, and future perspectives. Advances in Bioenergy, 8, 93-144. DOI: 10.1016/bs.aibe.2023.02.001, https://www.sciencedirect.com/science/article/abs/pii/S2468012523000032
- Sekhar, B. C. et al. (2021). Piezoelectricity and its applications. Multifunctional Ferroelectric Materials, 71(1). DOI: 10.5772/intechopen.96154, https://www.intechopen.com/chapters/77225
- Ju, M. et al. (2023). Piezoelectric materials and sensors for structural health monitoring: fundamental aspects, current status, and future perspectives. Sensors, 23(1), 543. DOI: 10.3390/s23010543, https://www.mdpi.com/1424-8220/23/1/543
- Yuan, Y. et al. (2022). Highly sensitive and wearable bionic piezoelectric sensor for human respiratory monitoring. Sensors and Actuators A: Physical, 345, 113818. DOI: 10.1016/j.sna.2022.113818, https://www.sciencedirect.com/science/article/abs/pii/S0924424722004538
- Zhou, P., Zheng, Z., Wang, B., Guo, Y. (2022). Self-powered flexible piezoelectric sensors based on self-assembled 10 nm BaTiO₃ nanocubes on glass fiber fabric. Nano Energy, 99, 107400. DOI: 10.1016/j.nanoen.2022.107400, https://www.sciencedirect.com/science/article/abs/pii/S2211285522004785
- Vetelino, J., Reghu, A. (2011). Introduction to Sensors. https://digitalcommons.library.umaine.edu/fac_monographs/24/
Disclaimer: The views expressed here are those of the author expressed in their private capacity and do not necessarily represent the views of AZoM.com Limited T/A AZoNetwork the owner and operator of this website. This disclaimer forms part of the Terms and conditions of use of this website.