Many industrial and commercial products such as valves, radiators, container vessels, drums and storage tanks must be subjected to rigorous testing to exclude all possibility of leakage and ensure the product is of high quality. Other industrial processes that require testing for leakage include bonding, welding and gasketing. A commonly used technique for leak detection is pressure decay, because while more effective technologies involving the use of helium ions are available, they are also more cumbersome and involve the use of expensive devices.
Instead, the pressure decay technique, carried out with the use of a simple pressure sensor, is elegant in its simplicity. The test piece is pressurized to specification and then isolated from the source of pressure buildup. The pressure inside is then monitored and any decay in the pressure levels is probably due to a leak.
Two different transmitters may be used for this purpose, as discussed under the following headings – a gage transducer or a differential pressure transmitter.
Gage-type Transducers
As seen in Figure 1, a gage type transducer is fitted into the circuit including a pressure source (compressed air source, in this example) and the pressurized container to be tested (a plastic container in this instance). The container pressure is built up to 100 psi, following which the valve above the point of attachment of the transducer is closed to cut off the flow of compressed air. Thereafter, any leak is detected as a pressure decay within the container, if adequate time is provided.
.jpg)
The presence of small leaks is detectable by this method, though it occupies more time, up to several minutes if the leak is very small. Again, factors such as hysteresis, repeatability and nonlinearity make it impossible to detect a leak with sufficient precision unless the pressure has become less than 99 psi ((100 PSI – 1% TTL Error band).
Differential Pressure Transmitters
The inherent disadvantages of a gage transducer may be overcome by the use of a differential pressure transmitter as shown in Figure 2. In this setup, valves 1 and 2 are left open, following which the pressure source supplies pressure to the test system. Once the container and the transmitter are both pressurized to 100 psi, valve 2 is shut off. The pressure within the line on either side of the sensor is now at 100 psi and therefore the transmitter output is zero. At this point valve 1 is also closed off.
.jpg)
Now, if the container has any leakage, the line on the corresponding side of the transducer will start to show loss of pressure. For instance, if the transmitter has a range of 0-5” WC and the total error band is 1%, a pressure decay of 1% of 5” WC is sufficient for its detection by the transmitter, i.e., a drop of only 0.05” WC.
Comparing this to the first setup in which the pressure decay must reach 1 psi or 27.68” WC, it is obvious that the use of the differential pressure transmitter speeds up decay detection by 500 times, making the test that much faster.
However, it is true that this level of response time or sensitivity is not required for every application in which leak testing is used. Viatran has a wide range of solutions for all types and settings of leak detection. For more information or other help with this type of application, interested customers may contact a Viatran Applications Engineer.
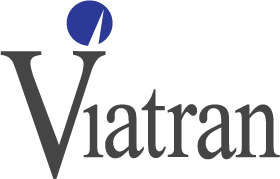
This information has been sourced, reviewed and adapted from materials provided by Viatran.
For more information on this source, please visit Viatran.