When it comes to managing inventory or determining the bin levels, milling operations present a number of challenges. It is possible that a single operation is used on bins of various sizes and construction and on different materials to measure. When choosing a tool for a specific bin, one should consider the material that is being determined; for instance, whether the surface of the material is uniform or irregular, the size of the tank, etc.
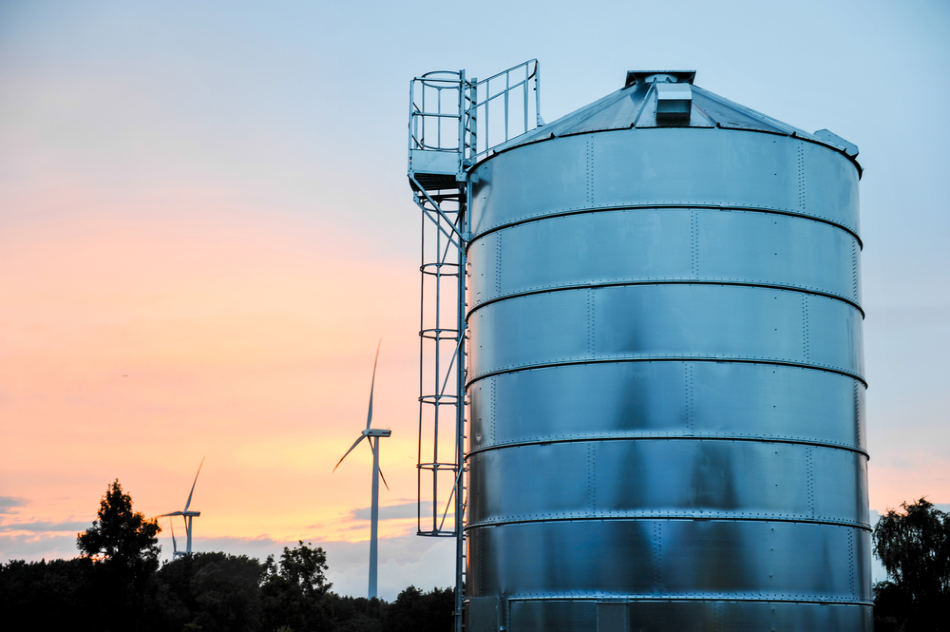
Image Credit: Shutterstock/Andrzej Wilusz
Bin Level Detection Device
A bin level detection device helps in managing inventory and improves safety for employees. It removes the requirement to ascend tanks to check levels and notifies operators when material reaches to a specific level in the bin. When there is no activity in the bin, the device offers a single measurement that can be repeated. It calculates the headroom in the tank so operators can easily find out the amount of space available in the tank.
.jpg)
.jpg)
Disadvantages of Bin Level Detection Device
It is commonly believed that a bin level precisely changes to mass and then converts to pounds. Granular materials, powders or pellets tend to shift, settle and compress in the tank. Certain sophisticated tools are available in the market that integrate compaction calculations within their software and to some extent compensate for the material behavior. However, a level measurement device cannot be used as a scale.
.jpg)
Rotary Level Indicators
Rotary Level Indicators are standard tools that are employed for low or high point level indication in silos, tanks and bins. When material reaches or falls away from the rotary paddle, a rotary sends an alert though a horn to an alarm panel. Users can easily operate the rotaries. When the device is utilized to notify that material has reached an elevated level while the bin is filling, the paddle continues to turn until the material in question reaches the paddle. When the paddle encounters resistance owing to the presence of material, it stops turning and gives out an alert.
Capacitance Probes
Capacitance probes are suitable for a variety of materials, including pellets, granules, powders and other slurry or solid materials. These probes can be employed to detect low, mid and high levels in hoppers, silos, bins, chutes, tanks etc., where material is kept, processed or released. The sensors can sense whether the material is present or absent by detecting a change in capacitance that occurs as a result of the variation between the air and the dielectric constant of the material stored in the tank. These sensors are capable of detecting even minute variations in capacitance.
Vibrating Level Sensors
A vibrating rod or vibrating level sensor is capable of detecting fluffy and lightweight materials such as flakes and powders. It can also be utilized for heavy materials such as pellets and grains. These are powerful sensors that are made of stainless steel and require only minimum maintenance. The sensor can be employed as a low, mid and high level alert device that can be positioned either on the base cone of a bin or on the top of a bin.
Bob-style Sensors
Bob-style sensors or weight and cable-based sensors are suitable for various applications as these devices are unaffected by temperature, dust, fumes, humidity or dielectric constant that can be found in the bin. A weight and cable-based sensor is cost-effective and provides precise and continuous level measurement.
For bins measuring approximately 180 ft in height, a bob-style sensor can be employed. However, the sensor is also employed in smaller bins measuring less than 40 ft in height. The principle of operation for bob-style sensors is quite simple. They operate by releasing a cable fitted with a weighted sensor probe that halts and pulls back when the probe touches the material. Users can take repeated measurements as the sensor probe moves downward and retracts, so as to ensure that each measurement is accurate.
3D Scanners
.jpg)
3D Scanner bin software.
Unlike radar devices that calculate one point and measure a single distance, a 3D scanner takes measurements from various points in the bin and utilizes these points to assess the material volume in the bin. It is a dust-penetrating bin volume measurement device that maps the bin’s topography to generate a computerized profile of contents in the bin. When the material surface of the bin is irregular, sampling measurements from various points allows the 3DLevelScanner to measure bin volume for solids and powders with more accuracy than other single point measurement devices.
Conclusion
A point level device can be used to know if a bin is full or empty. For determining bin level, such as headroom, percentage full or distance to product, a 3D device or bob-style sensor can be used. A non-contact device can be utilized to meet the regulatory environment demands it. However, certain non-contact devices, such as a radar perform in unreliably dusty conditions. To sum up, various technologies are available for bin level controls that range from a few hundred to a few thousand dollars.
.bmp)
This information has been sourced, reviewed and adapted from materials provided by BinMaster.
For more information on this source, please visit BinMaster.