.jpg)
Linde ethylene plant in Al Jubail, Saudi Arabia. Image Credit: VEGA
The Thing that Came out of the Cold
Nowadays, steam crackers – which are facilities for producing olefins like ethylene - are amongst the most complex things which can be planned and realized in large-scale petrochemical plants. The raw materials of roughly 30% of all petrochemicals are produced in these facilities.
When these facilities are situated in the Siberian permafrost, the right combination of quality, experience, and expertise are particularly necessary in order to deal with extreme environmental conditions.
One of the largest ethylene plants on earth is situated in Western Siberia. From next year onwards, 350 individually manufactured VEGAFLEX 81 and 86 guided wave radar sensors will process pressures and measure levels in this plant.
.jpg)
The large order for Linde reached enormous proportions. Image Credit: VEGA
Intriguingly, each of the 350 instruments has a completely unique design. Every single customer requirement must be fulfilled in petrochemical plant engineering, inclusive of the smallest details. Nearly 300 of the 350 VEGAFLEX 81 and 86 sensors were manufactured in a bypass chamber as a complete system – already assembled, mounted and ready to operate. In addition, roughly 30 sensors will be used as special versions in high-pressure steam boilers.
The Challenge of Process Complexity
The Linde Group’s Engineering Division is one of the leading global suppliers of these complex plants. As such, they have the technical expertise to meet the challenges involved in their manufacture. For level and interface measurements, Linde Engineering is reliant upon guided wave radar sensors such as VEGAFLEX 81 and 86.
VEGAFLEX 86 sensors are used in all areas in which high pressures and extreme temperatures prevail. In situations in which an extended, maintenance-free service life is required, these sensors are ideally suited.
Courtesy of their automatic runtime correction system, they can provide accurate measurement data in the plant’s high-pressure boilers, wholly unaffected by the saturated steam conditions.
Ready-Made for Final Inspection
.jpg)
Image Credit: VEGA
Reliable monitoring of the liquid phases is required at all times during the processes in ethylene plants. The separation of process substances into product and carrier phases is reliably monitored continuously by VEGALFEX 81 sensors.
Each of the bypass versions in the Siberia project have been assembled and set in advance. This is to minimize effort and costs for freight, commissioning, and installation. All system components must exactly fit to each other, in order to pass their final inspection.
Robust Without Mechanical Components
For the completion of measuring tasks which are commonly required in petrochemical plants, guided wave radar sensors are robust and perfectly suited. Even when confronted by fluctuating product density, they can measure olefin levels here with a high degree of reliability during the cryogenic process stages.
Providing extra protection of process and personnel, there is an additional process seal inside the VEGAFLEX sensors known as the “Second Line of Defense.” The low maintenance requirements of guided wave radar units are also advantageous. The downtimes of the plant are nearly zero due to the fact that they operate without mechanical moving parts.
.jpg)
Linde ethylene plant in Al Jubail, Saudi Arabia. Image Credit: VEGA
The Challenge of Process Temperatures
.jpg)
VEGAFLEX 86, with its od and cable probes, enables reliable and maintenance-free measurement, independent of media properties. Image Credit: VEGA
Reliable, maintenance-free measurement, without media properties, is enabled by the cable and od probes of VEGAFLEX 86.
Enormous cracking furnaces are at the center of ethylene plants. In these, such hydrocarbons as petrol components and gases are thermally cracked – meaning they are broken down into simpler molecules - at high temperatures in externally heated pipes. Steam is generated in the higher part of the cracking furnace, where the material being cracked is preheated with flue gas at temperatures which can reach +1,300 °C.
The combustion chamber of the lower furnace section is where the actual cracking process takes place. In this chamber, long tubes are situated. These are manufactured from a special alloy in which the feed mixture is heated to roughly +850 °C using large, gas-fi red burners.
It is then thermally cracked. After this stage, the product mixture is stabilized by the extremely rapid cooling of the temperature, from roughly +850 °C to around +400 °C.
Environmental Challenges
VEGA had to focus carefully on the project’s difficult challenges during the production of the 350 VEGAFLEX sensors. The level detection which they supplied must be able to function reliably even at high fluctuating product temperatures and extreme process pressures, as well as ambient temperatures under -50 °C.
As well as the special designs required, ready-to-install, process-optimized solutions are also a crucial factor in order to guarantee success.
Clearly, meticulously timing is required in the delivery of any project supply to site. However, in this circumstance, the special climatic conditions of this area of the world required this speed more than the customer.
Typically, heavy, oversized transport ships are only able to access the site on which the complex plant is being built for 45 days of each year, as this is the only period in which the Tobol and Tura rivers are ice-free.
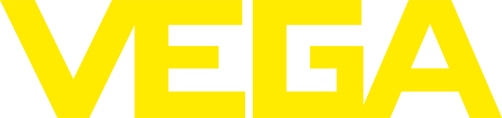
This information has been sourced, reviewed and adapted from materials provided by VEGA Grieshaber KG.
For more information on this source, please visit VEGA Grieshaber KG.