Marchwood power station can only live up to its reputation as one of the UK’s most efficient power plants when the steam quality is ideal. An unstable level measurement caused the engineering team some typical problems, and the issue was resolved only after installing level measurement equipment from VEGA.
High efficiency is not always simple to achieve, particularly in the power-generating industry. The precisely calibrated equilibrium between steam pressure and temperature could shift due to minute temperature and pressure variations, losing important reliability and effectiveness.
This situation in a power plant close to Southampton necessitated the operator’s search for a more reliable and precise level measuring method. The technology already in place included a highly complicated but standard method for detecting condensate in this type of plant.
In Marchwood Industrial Park, next to the River Test, Marchwood Power runs a natural gas-fired, combined-cycle power plant. A facility that generates 900 MW of power for the national grid costs £380 million to build. That would provide close to one million homes. It is one of the UK’s most efficient power plants.
Pressure Instrumentation by VEGA Makes the Difference
The measurement technology used by VEGA, which is housed deep inside the facility, helps to contribute to the high degree of reliability. The steam exhaust from the steam turbine condenses in the condenser vessel just below the steam turbine, where it is warmed, vaporized, and then fed back into the steam turbine. In this step of the process, the condenser’s level control must be reliable and precise.
If the level is too high, the liquid could enter the turbine and do significant damage. To maximize the condensing process and the turbine’s operational efficiency, the condensate must be kept at a consistent level while maintaining optimal back pressure and vacuum.
When the system was first developed and commissioned, three differential pressure transmitters were installed in a 2-out-of-3 selection circuit. The DP system’s low-pressure (LP) leg required a constant top-up from a condensate pot.
This occurred due to the condenser’s vacuum emptying the LP leg, leading to the level reading mistakes. The key challenge to prevent faults in the system was maintaining a steady supply of condensate to the level system employing a series of valves and rotameters.
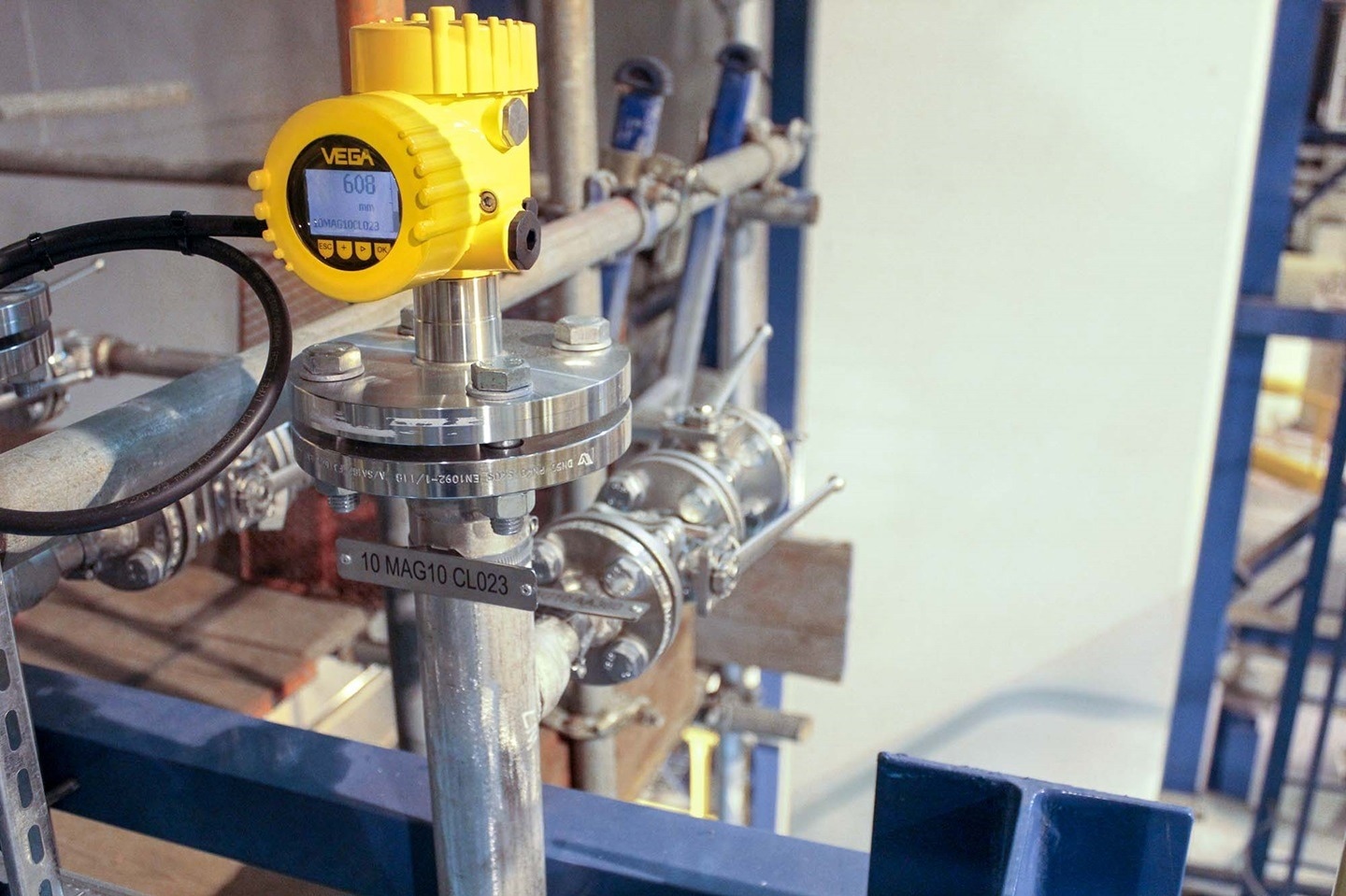
50 mm-diameter bypass tubes with shut-off valves at the top and bottom. Image Credit: VEGA Grieshaber KG
With this selection circuit, a single measured value can differ. However, when two measured values diverge and go beyond the tolerances, a defect is signaled, and appropriate measures are taken.
This intricate setup frequently caused one of the three DP transmitters to produce inaccurate level measurements. Therefore, there was a constant high chance of a fault occurring.
This could affect the system’s availability because if all three differential pressure transmitters showed a different measured value, this would prompt a preventative shutdown if it is not fixed.
The challenge
Due to this application's interconnected rotameters, condensate tanks, valves, and pipes, using a differential pressure gauge is quite difficult. Maintaining the level of the condensate in the pots and the LP piping along with the calibration of the differential pressure transmitters required sophisticated and time-consuming system upkeep.
Marchwood Power needed a new solution as a result that would be more precise, reliable, and require less maintenance, eventually increasing plant availability. Additionally, they wished to keep employing the 2-out-of-3 selection circuit for safety.
Precise Measurement Results in Bypass Tubes with VEGAFLEX 81
Three VEGAFLEX 81 guided wave radar transmitters can be fitted in 50 mm-diameter bypass tubes with shut-off valves at the top and bottom of the company installed more interconnecting pipes from the condenser, according to VEGA’s recommendation.
The major benefit of guided wave radar technology is that it has been clearly shown to be fully independent of temperature, pressure, and vacuum. The bypass tubes, where the measuring range is slightly over 1.7 m, the pressure ranges from 25 mBar Abs to atmospheric, and the temperature is always below 40 °C, feature no measuring problems.
With approval for direct boiler level control and the ability to endure temperatures of up to 450 °C and 400 bar, the VEGAFLEX 80 series can easily survive these circumstances and yet fulfill the standards for automated/unmanned operation as specified by EN12952-11:2007 and EN12953-9:2007 (also as a limiting device in redundancy).

Inter-connecting pipes from the condenser with three VEGAFLEX 81 guided wave radar transmitters in bypass tubes. Image Credit: VEGA Grieshaber KG
The instruments only needed to be connected and set up once they had been put into the bypass chambers. Using the PACTware software, the Marchwood Power engineers were able to complete the commissioning themselves. The advantage is that they could save exact records of the sensor adjustment and promptly obtain feedback on the configuration.
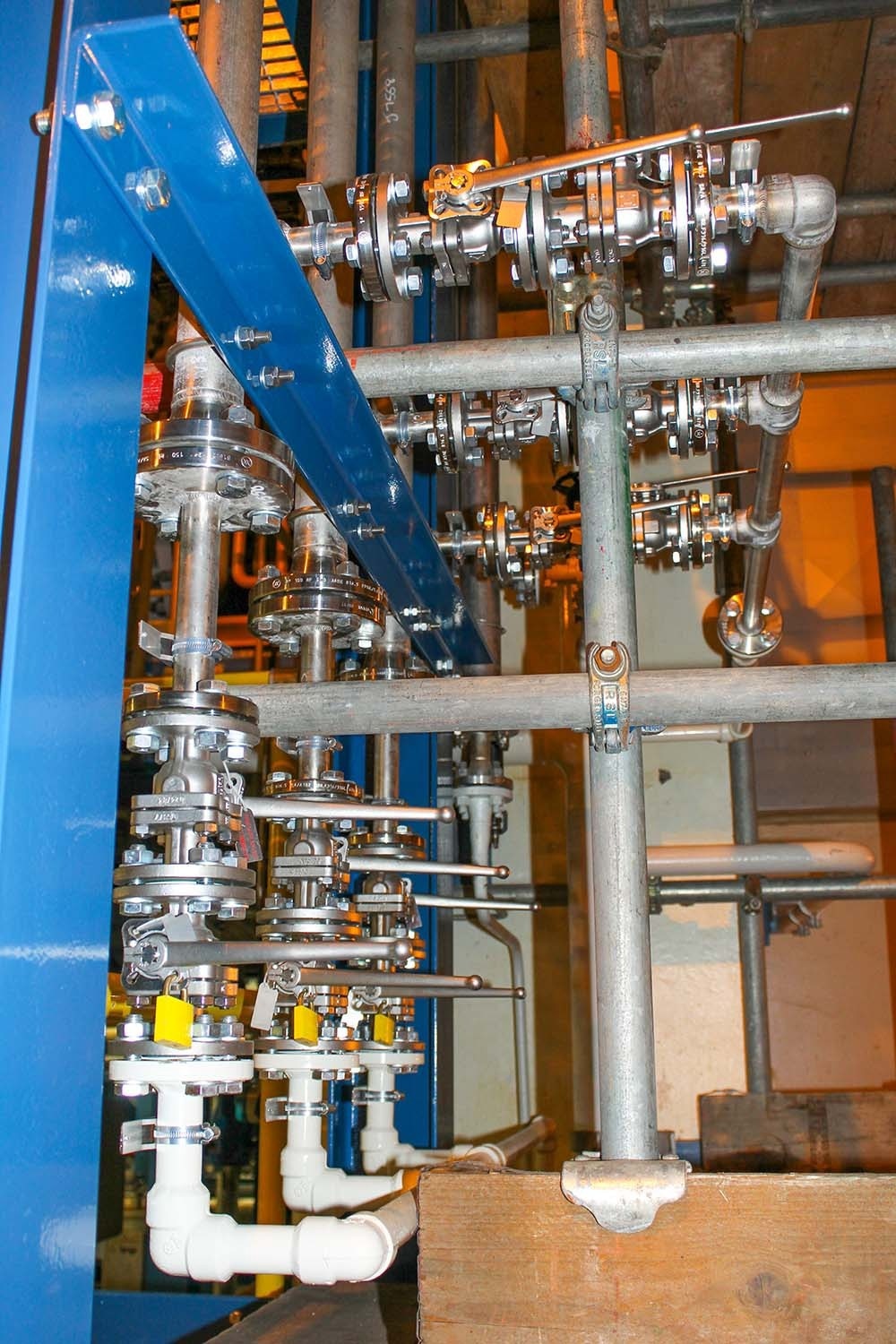
Image Credit: VEGA Grieshaber KG
In addition to lowering maintenance expenses, there were further benefits. The measurement device for gauging the level in the condenser that Marchwood Power had been seeking was reliable and above all simple. The overall expenses were found to be much lower than those of the original differential pressure transmitter system.
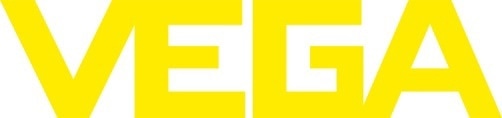
This information has been sourced, reviewed and adapted from materials provided by VEGA Grieshaber KG.
For more information on this source, please visit VEGA Grieshaber KG.