.jpg)
Drinking water is the most important food of all. Its preparation requires complex processes. (Image credit: Cozine/Shutterstock)
Of all drinks, drinking water is the most important. Complex processes are required in its preparation. Ozone is frequently added to drinking water during treatment in order to disinfect and oxidize it. Ozone must be produced and added to the water on site, adhering to stringent safety regulations, as it is highly reactive.
VEGA Pressure Transmitters
The pressure transmitters provided by VEGA make a vital contribution to the continued processing of drinking water of the highest quality.
One of Germany’s largest water supplies, and traditionally one of the furthest-reaching, is Baden-Württemberg’s water supply system. Approximately 90 million cubic meters of drinking water is supplied by this system each year to roughly 250 cities and municipalities.
During the management of the regional water supply, a high level of top quality security is pivotal.
At the start of the 20th century, the central Neckar region’s population was already expanding quickly alongside the progression of industrialization. An extremely far-sighted plan at this time was to transport drinking water to Stuttgart via the city of Ulm and the Remstal from the Danube valley. This system laid the basis of the regional water supply.
Treatment of Drinking Water
In plants where river water is converted to drinking water, a raw water pump is used to draw water directly from the river. A pressure pipe is then used to transport water from the pumping station to the waterworks and the treatment facilities therein.
As much as 2,300 liters of river water can be converted into drinking water every second during peak periods. State-of-the-art technology is required in order to inject highly active oxygen (ozone) for oxidation and disinfection during the process of drinking water treatment.
Dissolved and particulate organic matter is oxidized by Ozone, which inactivates or kills existing microorganisms. When molecular oxygen (O2) is decomposed into individual oxygen atoms (O) by any form of energy, ozone is always formed as these atoms react with molecular oxygen (O2).
This can occur via lightning strikes or UV radiation, as well as high-voltage electrical discharges. Ozone is produced, transported, and added to the water on site. As a result of its high reactivity, this is done in compliance with stringent safety regulations.
Pressurized Reactors
Pressurized reactors are used during the actual production process, in which oxygen is converted into ozone via the application of electrical energy. Following this, the gas mixture produced flows into an ozone collecting pipe. The maximum ozone concentration is about 180 g/Nm³ at an operating pressure of 1.3 bar.
.jpg)
Ozone generators ensure the production of safe drinking water. Image Credit: VEGA
Ozone is fed into the water using injectors, while the tiny ozone bubbles are evenly distributed throughout the volume of the water by mixers. The water is kept in large containers for a few minutes, during which time disinfection and oxidation occur.
.jpg)
Measuring point with VEGABAR 82 and “Second Line of Defense.” Image Credit: VEGA
VEGABAR 82
In order to ensure the absolute safety and reliability of the pressure measurement in the ozone collection pipe, and during other important measuring points, VEGABAR 82 was used by the engineering department.
This pressure transmitter has a ceramic CERTEC® measuring cell and a “Second Line of Defense.” This is an additional separation process which operates via a gas-tight feedthrough system above the process connection.
Even though the measuring cell is permanently ozone-resistant, an extra layer of protection against ozone leakage from the pipeline via the pressure transmitter is provided by this second line of defense.
A vital part is consequently played by VEGABAR 82 in the safe generation of ozone, as well as the continued production of drinking water of the highest quality.
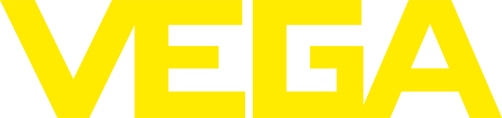
This information has been sourced, reviewed and adapted from materials provided by VEGA Grieshaber KG.
For more information on this source, please visit VEGA Grieshaber KG.