The decision to install and implement a gas detection system within a facility should be congratulated as it is a huge step in the correct direction towards increasing the overall safety of the facility and its workers.
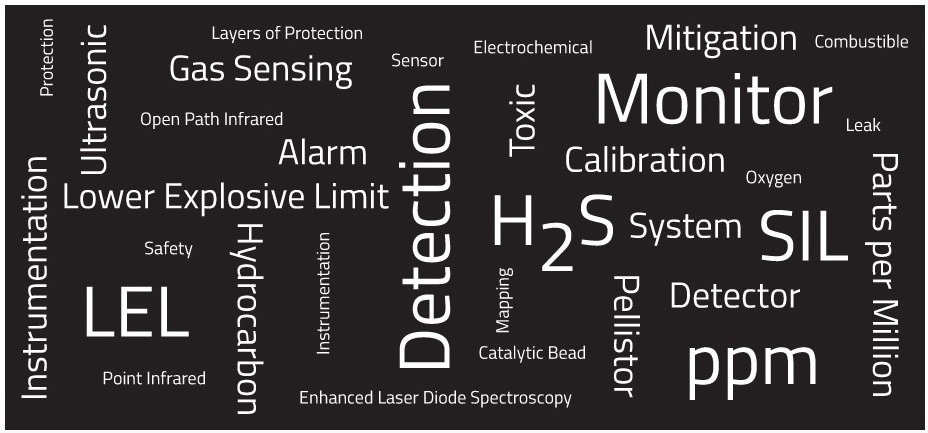
The next part of the process is choosing the correct technology to meet the requirements of the application. While this may seem like a daunting task, it can be enjoyable when there are industry experts present who can assist the customer in understanding exactly what is needed, and why.
If the customer is intent on undertaking some initial research, a beneficial starting point is to understand the technologies available. It is also important to understand which technologies may be considered over others, in regards to the location or reason for installation.
Using a multifaceted approach to find a detection system will increase the chances of reducing risk, as no single technology is the solution for every application. First of all, the available options must be understood.
This article has been created to help the reader understand the technologies that form the majority of present-day industrial gas detectors, along with some of the major areas and applications where a particular technology may be used:
Catalytic Bead (CB)
The operating principle of catalytic gas detectors uses catalytic combustion to analyze combustible gases in air at LEL (lower explosive level) concentrations. A heated catalyst (a coated wire coil) burns the specified gas.
The electrical resistance of the wire becomes greater as its temperature increases. An average Wheatstone bridge circuit employs two-wire coil elements (one for compensation and one for detection) to modify the raw temperature change to indicate the presence of combustible gas.
- Catalytic Bead technology can be used in the following applications: They are most effective for the detection of hydrocarbon gas, along with acetylene and hydrogen. They work well in environments with high and low-temperature extremes, around vibrating or hot machinery, and in humid conditions.
Electrochemical (EC)
Electrochemical detectors are classed as transducers that translate gas concentration into an electrical current. They utilize electrodes and an electrolyte to create an electrochemical reaction that generates a current corresponding to the concentration of gas.
Various kinds of cells have been produced for particular toxic gases, such as oxygen enrichment or deficiency, carbon monoxide, hydrogen sulfide, and more.
Electrochemical technology can be used in the following applications:
- They are highly suited for the detection of oxygen enrichment or deficiency in confined spaces, and in the measuring of toxic gas in the parts-per-million (ppm) range.
Point Infrared (PIR)
Infrared gas detectors utilize two wavelengths, one at the gas absorbing ‘active’ wavelength and the second at a ‘reference’ wavelength with no gas absorption.
The concentration of hydrocarbon gas is tested using the infrared absorption of an optical beam referred to as the active beam in point IR detectors. An additional optical beam, the reference wavelength, adheres to the same optical path as the active but holds radiation at a wavelength not absorbed by the gas.
Point Infrared technology can be used in the following applications:
- They are most appropriate for the detection of hydrocarbon gas, particularly in environments lacking in oxygen, for example, ducts or inaccessible areas like ceilings, as they require little maintenance.
- They are additionally suited to environments where there are known concentrations of halogenated hydrocarbons, silicones, or hydride gases. Flammable hydrogen has a high response with catalytic gas detectors but cannot be detected by IR absorption.
Open Path Infrared (OPIR)
OPIR detectors have a similar operating principle to the point IR technology described above, however, the detection path distance of the IR beam is increased to greater than 100 meters.
Utilizing separate IR transmitters or a retro-reflector and receivers housed in various enclosures, OPIR detectors monitor for a gas cloud in the IR beam path. There are OPIR detectors on the market that measure in both the LEL-m and ppm-m ranges to identify both small and large leaks.
- Open Path Infrared technology can be used in the following application: They are highly suited for use in large and uncontained areas where they can be installed along a line of many sources of potential leaks such as a row of pumps, tanks, or valves.
Laser-Based Gas Detection Technology (ELDS)
The Enhanced Laser Diode Spectroscopy Gas Detector (ELDS) is an open-path and non-contacting method of identifying particular flammable or toxic gases. The ELDS sensor’s laser optical technology detects and measures a gas’s particular harmonic fingerprint when a gas leak occurs.
False alarms as a result of interference gases, which are experienced by alternative detection technologies, are not a challenge for ELDS detectors due to their very selective harmonic fingerprint technology. In contrast to electrochemical cells, ELDS sensors are also resistant to sensor poisoning because they are an optical device.
- Laser-Based technology can be used in the following application: They are most effective in monitoring the outer perimeter of property fence lines to protect against a particular toxic gas reaching beyond the boundaries of the facility.
Ultrasonic (UGLD)
Compared to traditional gas detectors that analyze % LEL, ultrasonic gas leak detectors react to the ultrasonic noise produced by a pressurized gas leak.
This ultrasonic noise gives a measurement of the leak rate and constructs alarm and warning thresholds. The gas does not need to reach the sensing element because the detector ‘hears’ the gas leak.
- Ultrasonic technology is used most effectively in outdoor installations and indoor spaces with high ventilation rates.
Layers of protection can be created around a facility by considering the possible gas hazards, therefore, mitigating risk and helping to keep employees safe. Point fixed gas detectors are the first line of defense installed near to possible leak sources for example tanks, compressors, valves, pumps, pipes, and other equipment.
The addition of UGLD and/or ELDS detectors brings additional layers of protection to improve the safety and protection of people, facilities, and equipment.
Watch the MSA eLearning webinar on Gas Sensing Technologies to get more information about these detection technologies and their strengths and weaknesses.
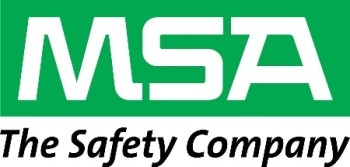
This information has been sourced, reviewed and adapted from materials provided by MSA - The Safety Company.
For more information on this source, please visit MSA - The Safety Company.