Plastic parts are vital in a wide range of different industries. New combinations of materials and manufacturing techniques are being developed all the time, especially in challenging application areas like automotive engineering.
Continuous fiber-reinforced thermoplastics are a common example of this sort of innovation, offering extreme strength while being simultaneously lightweight.
Automotive engineering is just one such field offering an array of possible applications for continuous fiber-reinforced thermoplastics. Components manufactured from this material have good mechanical properties and can accommodate complex geometries, while still being lightweight.
Injection molding technology provides manufacturers with the ability to design workpieces in precisely the shape they require, using their preferred materials. Metal parts can be incorporated into these components, and, at the same time, the technology facilitates short cycle times, a crucial consideration when manufacturing large series.
New Manufacturing Techniques Demand Precise Temperature Monitoring
Using its FiberForm process, KraussMaffei has successfully developed a new technique for producing these parts to a high standard. Continuous fiber-reinforced thermoplastic semi-finished products (also known as organo sheets) serve as the base material in this instance.
Large-format semi-finished products like these can be made from carbon, glass, aramid, or composite fiber layers embedded in a thermoplastic matrix such as polypropylene or polyamide. The organo sheets are heated before being thermoformed into the desired shape and back-injection molded.
The first stage in this FiberForm process – heating of the semi-finished products - is extremely important if the whole process is to be successful. The temperature should be as uniform as possible across the organo sheets’ whole surface.
The sheets are heated in special ovens containing infrared radiators, with two important considerations: the organo sheets must be heated as rapidly as possible and the temperature must be distributed homogeneously across their whole surface.
New Measuring and Control Technology
KraussMaffei has designed and developed an infrared heating technology suitable for this process, capable of guaranteeing homogeneous, rapid heating of the organo sheets. In the standard version, up to 72 infrared radiators will be integrated into the heating system, depending on its size.
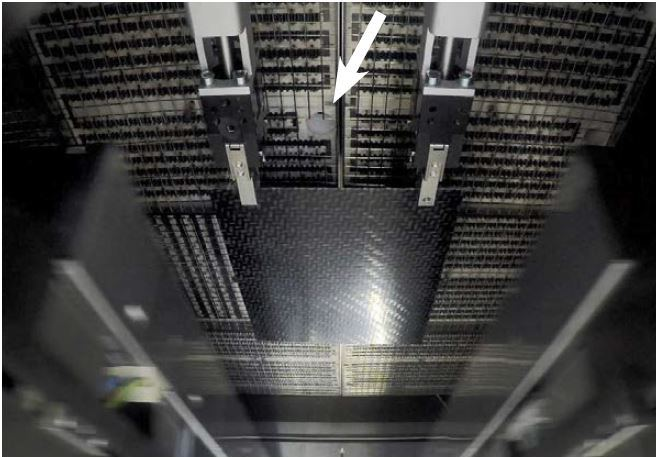
In the infrared heating system of KraussMaffei the semi-finished products are heated up to the due temperature. The infrared thermometers are located behind the recess (white arrow). Image Credit: KraussMaffei
The temperature controller used to operate the individual infrared radiators presented the developers with a huge challenge.
Dr Mesut Cetin, Head of Product Management, KraussMaffei
Dr. Cetin assisted in bringing life to these innovative new lightweight products.
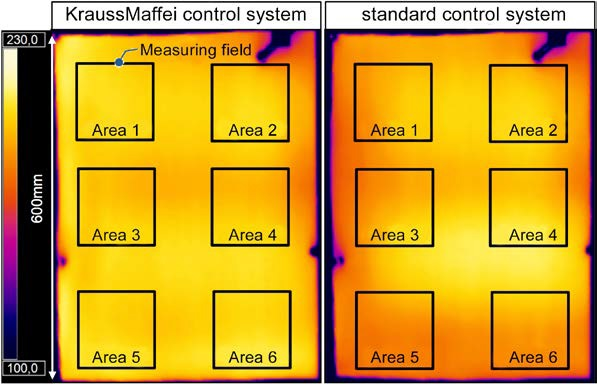
During the development and implementation, the results have been checked additionally with infrared cameras of Optris. The new process regulation of KraussMaffei (left side) ensures a homogeneous distribution of the surface temperature. Image Credit: KraussMaffei
Traditional, commercially available temperature controllers are rarely suitable for this task.
Standard temperature controllers work with just one infrared pyrometer to determine the temperature and control the heating station.
Christian Herrmann, Development Engineer, KraussMaffei
Herrmann was central in developing these new products.
“We could not heat the semi-finished products quickly and achieve homogeneous temperature distribution across their entire surface using this method.” The acting times and controller’s standard design were not suited to the application in question, nor did they meet market requirements.
Furthermore, standard controllers were not able to accommodate the entire system being heated over multiple cycles, or the consequences of this operation.
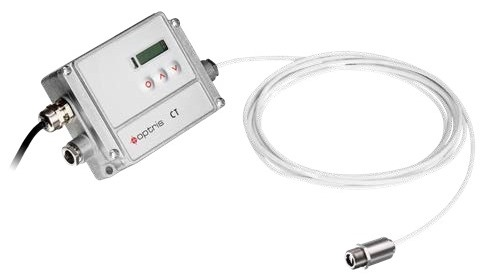
Robust Pyrometers From a Specialist Manufacturer
CT LT22 pyrometers from Optris proved to be an ideal choice in this situation. Herrmann outlines the decision, “There are lots of benefits of using these pyrometers in our applications. They are really compact and able to withstand even the high ambient temperatures that prevail right behind the infrared radiators, which is where we install them.”
The pyrometers themselves are comprised of two parts - the compact sensor head is just 14 mm in diameter, and able to function at ambient temperatures up to 180 °C without cooling. The remote electronic system is where the parameters are defined, and this can be installed a good distance away from the sensor itself.
In this example, the electronic system was installed externally to the infrared heating system. The sensor head was fitted with an optional air purge collar in order to prevent the optics from being contaminated by spray mist or dust.
Alongside the compact design, this extra was very important to us, because dust loads are always to be expected in the plastics industry.
Christian Herrmann, Development Engineer, KraussMaffei
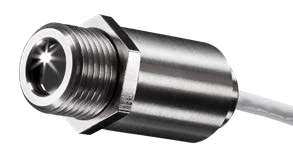
Intelligent Control Technology
The software used for controlling the temperature of the new heating system is comprised of one external and numerous internal closed-loop systems. Initially, a single pyrometer is assigned to each individual heating zone.
The external closed-loop system monitors the overall temperature, simultaneously accounting for the way in which the various zones affect one another. Temperature control hardware is provided by industrial PCs, with the pyrometers connected via a 4 to 20 mA current output. These are included in Optris pyrometers as standard.
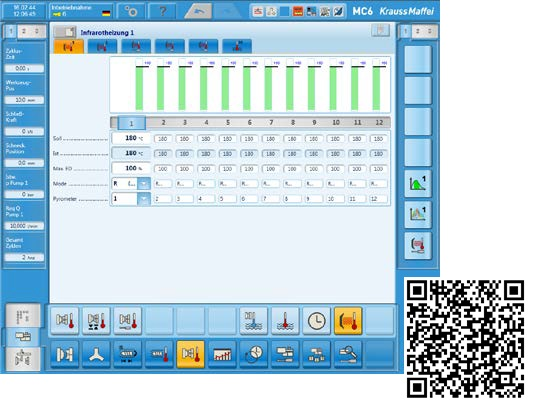
Screenshot of the user interface at the plant. Image Credit: KraussMaffei
KraussMaffei’s infrared heating technology can be integrated into a production facility from both a software and hardware perspective.
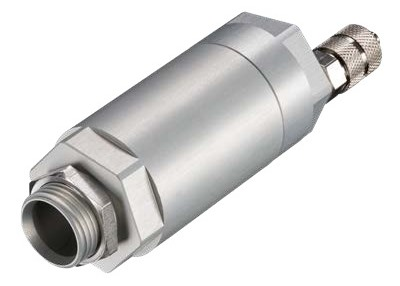
The system is mechanically connected to an injection molding machine via the standardized Euromap 18 interface, meaning that KraussMaffei’s infrared heating technology can also be retrofitted into injection molding machines already installed and in use.
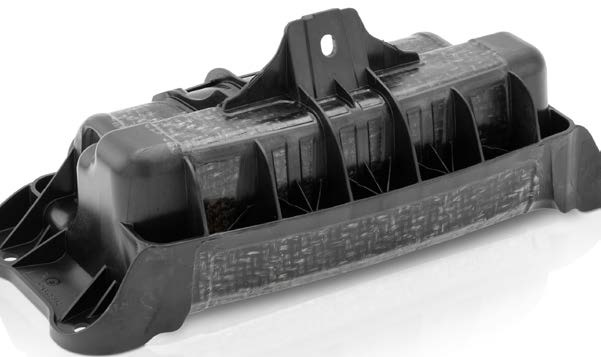
Airbag housing after the FiberForm process. Image Credit: KraussMaffei
The hardware and software solution for controlling the infrared heating system’s temperature must also be able to seamlessly communicate with the injection molding machine’s controller. Because of this, the heating technology is fully integrated into the KraussMaffei MC6 injection molding machine controller.
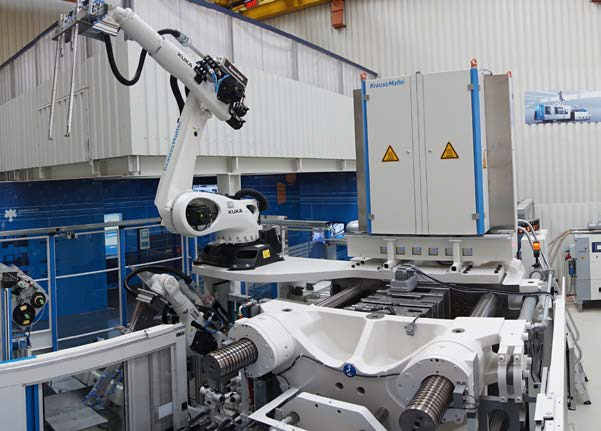
Automated manufacturing plant for the production of continuous fiber-reinforced thermoplastics. Image Credit: KraussMaffei
Reliable Series Production
The infrared heating technology heats the organo sheets rapidly and homogeneously. This is an important consideration when working with series production, along with the issue of the oven’s reliability.
These considerations are relevant for the control technology, as well as the mechanics themselves. Reliable components are essential, as, in a worst-case scenario, a single failed pyrometer could result in a complete halt in production.
“Since we have been using Optris pyrometers - and we started way back in 2010 - we have not had a single device failure,” says Dr. Cetin, summarizing his company‘s experience with Optris temperature measurement technology.
Acknowledgments
Produced from materials originally authored by Dr. Mesut Cetin and Christian Herrmann from KraussMaffei, and Torsten Czech from Optris GmbH.

This information has been sourced, reviewed and adapted from materials provided by Optris GmbH.
For more information on this source, please visit Optris GmbH.