Sponsored by CSEMOct 23 2020
Using micro-manufacturing techniques inherited from the microelectronics industry, it is possible to batch process with a micrometric precision, centimeter scale silicon parts with extremely fine mechanical functions.
High precision mechanical watches can particularly benefit using this method, as it fosters the emergence of novel ideas and enables their concretization at the watch scale.
CSEM has always played a key role in this field and looks to become the Swiss Competence Center for the design, assembly, manufacturing, and characterization of hybrid silicon-based innovative watch micromechanisms.
A novel escapement has been invented in the Frame of the SILOSCAPE MIP, designed, produced and integrated in a watch caliber; through a first characterization campaign its functionality has been validated. Silicon is corrosion free, magnetic, and characterized by a low density and a high fracture strength, an ideal elastic behavior.
It can be batch processed in 2.5D with a micrometric precision for the production of large quantities of centimeter-scale mechanical parts that can comprise multiple levels and fine mechanical functions such as flexure blades by utilizing microfabrication methods which were inherited from the microelectronic industry (DRIE).
Silicon has progressively opened up new opportunities for the design and production of novel and innovative watch mechanisms because of the combination of all these interesting features.
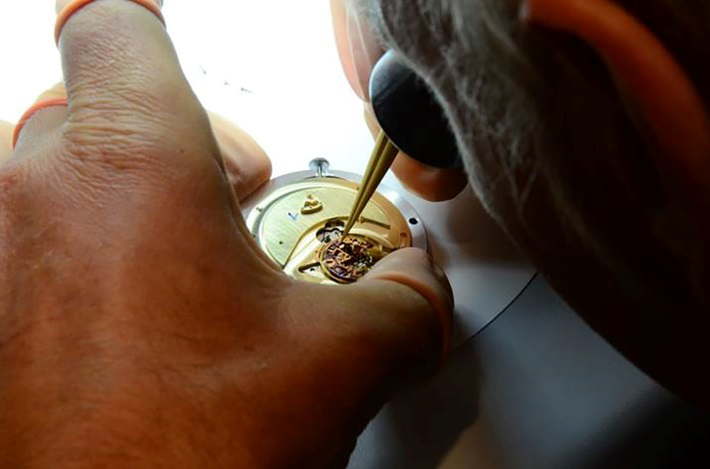
Figure 1. Assembly of the SILOSCAPE escapement in a watch caliber. Image Credit: CSEM
CSEM was a precursor in this field[1] in the late 1990s, paving the way for a new trend which is now followed by a number of key players in the Swiss watch industry. Since then, CSEM has kept carrying on its pioneering work by improving its mastery of the production of such delicate parts [2,3,4] and by pushing back the frontiers of the micromechanical structuration of silicon.
The most delicate and high added-value technical parts of a mechanical watch are the oscillator and the escapement. CSEM has proposed several original designs of mechanical watch oscillators for the past ten years and, in a close partnership with Vaucher Manufacture Fleurier, integrated at the watch level, the very original FlexTech and silicon-based Genequand[5] escapement, the very first in its kind.
Designed and produced by CSEM, the SILOSCAPE escapement is the last FlexTech based escapement, seen in Figures 1 and 2. The SILOSCAPE escapement is based on the use of flexure blade pivots like the Genequand escapement, replacing conventional ruby pivots and enabling extremely precise and frictionless oscillations of the guided components.
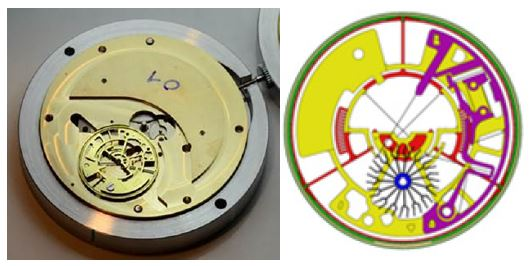
Figure 2. SILOSCAPE escapement (right) integrated in a watch caliber (left). Image Credit: CSEM
Comprising a total of four monolithic silicon parts from the escapement wheel to the oscillator, and paired with a Wittrick oscillator, this original escapement is assembled using a mixture of wafer level and manual assembly methods.
The SILOSCAPE escapement features a high-power reserve (usually three times higher than conventional Swiss anchor escapements) and, it can restart instantly on its own, utilizing the torque supplied by the escapement wheel when subject to external perturbations causing it to halt, therefore behaving similarly to the classical Swiss anchor escapement.
It is expected to be comparable to a Swiss anchor escapement as far as its isochronism is concerned, but a fine-tuning mechanism is needed to set it correctly; this mechanism is integrated directly in the escapement itself so that no additional part is needed in the end.
The experimental tests which were performed on the first prototypes enabled the validation of the intrinsic auto-starting specificity of the SILOSCAPE escapement. In order to better tune/compensate the isochronism a design update is still needed; a solution has been identified and is ready to be implemented on the next run of parts.
To fully validate the last main design iteration the next steps are: a shock analysis leading to a specific anti-shock design, the integration of all these updated parts in a watch caliber and a full characterization campaign similar to the procedure and then watchmakers when they want to validate a new design prior to its industrialization.
Acknowledgments
Produced from materials originally authored by F. Barrot, G. Musy, O. Laesser ●, R. Winiger ●, F. Cosandier, L. Giriens, E. Dominé, Y. Petremand, M. Amine, S. Ischer, P.-A. Clerc, S. Pochon and F. Rigoletti from CSEM.
References
● External key contributors: "Olivier Laesser" and "Winiger Horloger"
[1] A. Perret, "Le silicium comme matériau dans la fabrication de pièces mécaniques", SSC, 2001.
[2] S. Jeanneret, et al., “Procédés de micro-fabrication avec application horlogère, développements récents”, SSC, 2008.
[3] O. Dubochet, et al., “ L’hybridation du silicium: vers une simplification de l’intégration decomposants silicium dans les mouvements horlogers”, SSC, 2015.
[4] M. Despont, et al., “ “Tic-Tac” made in Silicon”, SSC, 2019.
[5] F. Barrot, et al., “Un nouveau régulateur mécanique pour une réserve de marche exceptionnelle”, SSC, 2014.
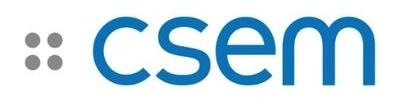
This information has been sourced, reviewed and adapted from materials provided by CSEM.
For more information on this source, please visit CSEM.