In this interview, AZoSensors talks to Jürgen Skowaisa, Product Management Radar, Ultrasonic from VEGA, about how reliable level and pressure monitoring is required to produce clear drinking water.
Can you start by giving our readers an overview of the importance of drinking water treatment processes in deep wells and related applications?
Drinking water will become more and more important in the future - some people even say that it is the gold of tomorrow. Drinking water must first be extracted by river dam, water source, or deep well in order to get to the groundwater or water from rivers or seas.
Extracted water must be cleaned and treated before ultimately being stored and distributed to people. In the drinking water industry, many applications require a reliable level and pressure measurement solution.
Inside a deep well, groundwater must be measured constantly during water extraction. Level measurement using a hydrostatic pressure transmitter is ideal in this scenario because these instruments use a robust ceramic cell that enables reliable, maintenance-free measurements. A cable version is also available, with cables up to 1000 meters long.
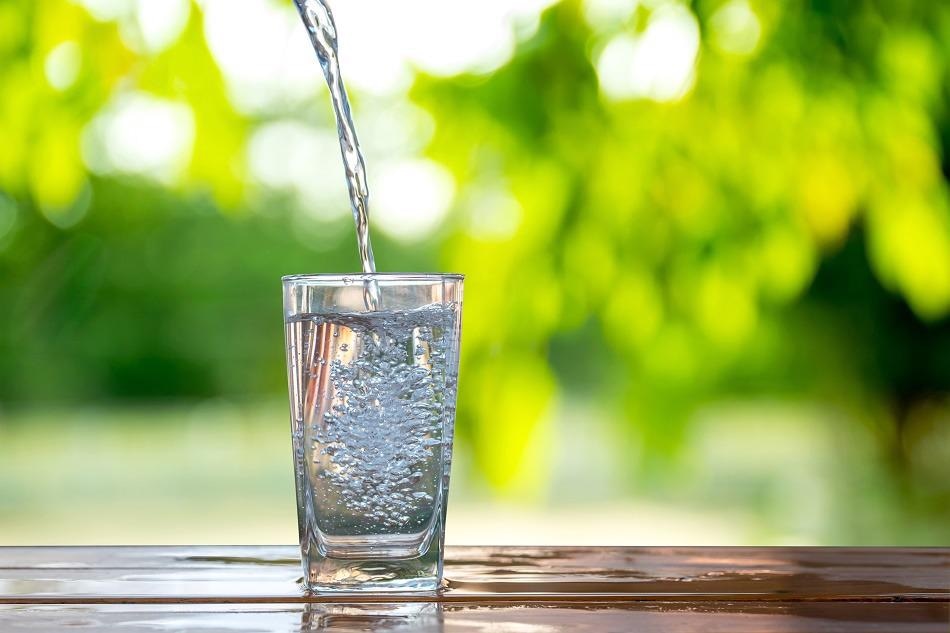
Image Credit: jinnawat tawong/Shutterstock.com
Not all deep wells have a narrow tube to measure inside – there may be a bigger well or a bigger tube barrier, meaning that a non-contact sensor needs to be installed. Ultrasonic sensors have been used in the past to measure the surface level of the water, alongside a controller to control the pump.
How can radar applications be used in place of traditional ultrasonic measurement devices, and when is it better to use cable measurement systems?
Today, we use radar devices for many kinds of applications. A range of radar technologies is available, and these are specifically designed for water level measurement applications. We offer compact versions of radar technologies, cable versions, and controller versions.
To effectively compete with ultrasonic instruments, a radar device must be able to perform similar functions.
Ideally, radar solutions should offer a compact design and high chemical resistance. A display is also a useful feature in some settings. In inaccessible places, such as on a high tank, a display may not be necessary. A direct cable connection can be used to connect the cable directly to a remote system.
Radar sensors have a maximum measuring range of between 8 and 15 meters, making them suitable for a lot of standard applications.
Sometimes it makes sense to use a cable measurement instrument, particularly when conducting measurements in a challenging atmosphere. Cable instruments are available in PVDF housing, with everything required for the measurement included inside the housing.
The complete range of electronics and the cable entry is enclosed, so there is no opportunity for humidity to affect the components, even if the sensor is flooded for a short time.
Different versions of sensors are available, not only in terms of signal output but also in terms of the design of the sensor. The signal output will be selected either for the 4 … 20 mA as a standard, or Modbus or STI 12 for the hydrological market.
Larger sensors are also available, offering a maximum range of 15 to 30 meters. The presence of a larger antenna also allows for better focusing.
Can you give our readers a practical example of these sensors in operation?
A drinking water facility is located by a lake, next to a river dam in the South region of the Black Forest, very close to VEGA’s headquarters. Black Forest water is treated in this facility before being distributed to 250,000 local residents.
The inlet to this river dam is important, and the flow of this inlet must be measured every day or even constantly. The facility uses a bubble method which involves using a compressor to insert air into the inlet. This allows the pressure to be ascertained, enabling the flow to the flume to be calculated.
The bubble method works, but it does involve higher installation, maintenance, and running costs.
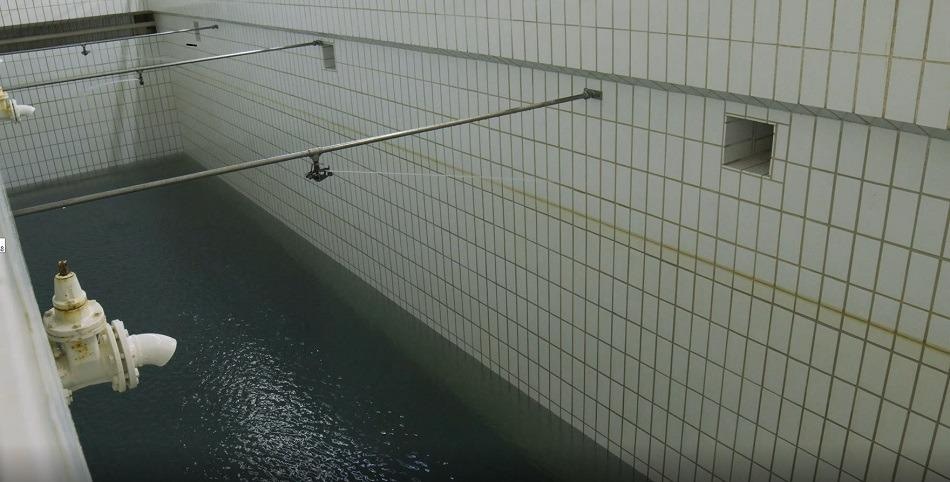
Image Credit: VEGA Grieshaber KG
A contactless radar system offers a much better solution. This approach also involves a channel, a flow, and a flume. Here, we can measure the level and calculating the dimension of the flume and the flow using a non-contact radar.
An ultrasonic sensor would make use of a sound wave, but this sound wave can be impacted by wind, rain, or temperature, changing its velocity and potentially returning an incorrect level. The radar device, however, uses a microwave which is not affected by these influences.
How has the development of new and improved controllers impacted measurement applications?
Our new controllers are very robust and include a large display. These can be mounted outside of a pipe on a wall, on a front panel, in a switching cabinet, or on a carrier rail.
It is possible to connect one or two sensors and have different relays inside, with larger controllers including additional digital inputs and an SD card large enough to store more than 100 million values. These controllers also offer integrated functions, for example, pump control, flow measurements, internal flumes, and a totalizer.
Regardless of the size or mounting of a controller, each has the same functions and relays inside, and even the smaller controllers have functions for measuring water and wastewater, making them ideal for machines and plant manufacturers.
How do filter functions differ between ultrasonic and radar applications?
When the water reaches the water treatment plant, one of the first steps in processing involves the filter system. There are different types of filters available, depending on where the water comes from; for example, from a river, a well, or from a lake like in our example.
One typical filter often used in drinking water treatment plants is a sand filter. Here, gravity prompts the water to travel from the top of the filter to the ground, filtering out all the small particles.
When the filter gets dirty, it will need to be backwashed. During backwashing, the surface becomes rougher because compressed air and water are pressed from the bottom to take the sludge out. After a few cycles, however, the water is clean, and the filter can be used again.
Both ultrasonic and radar sensors can be used along with a controller to measure the surface prior to the filter being backwashed, but ultrasonic devices can potentially lose the signal because the rough surface results in part of the soundwave being reflected off to the side.
A radar device will be able to return the right value, however. During the filter backwash procedure, there would be no reliable measurement using the ultrasonic device. This can cause problems because we need a reliable measurement at this time to monitor the progress of the backwash.
Why are radar sensors useful in measuring and managing the chemicals present in water treatment systems?
Every treatment plant has chemicals present. A drinking water facility will likely use chemical tanks filled with chlorine for disinfection or iron sweet sulfate. It is very important to ensure reliable measurement of these chemical tanks because the chemicals are constantly filled and emptied.
We currently offer a chemical-resistant compact new radar sensor. A considerable benefit of the radar sensor is that it has no blocking distance. Unlike ultrasonic sensors, it is possible to measure up to the surface of the sensor, and we can use the complete capacity of the vessel, therefore saving time and money.
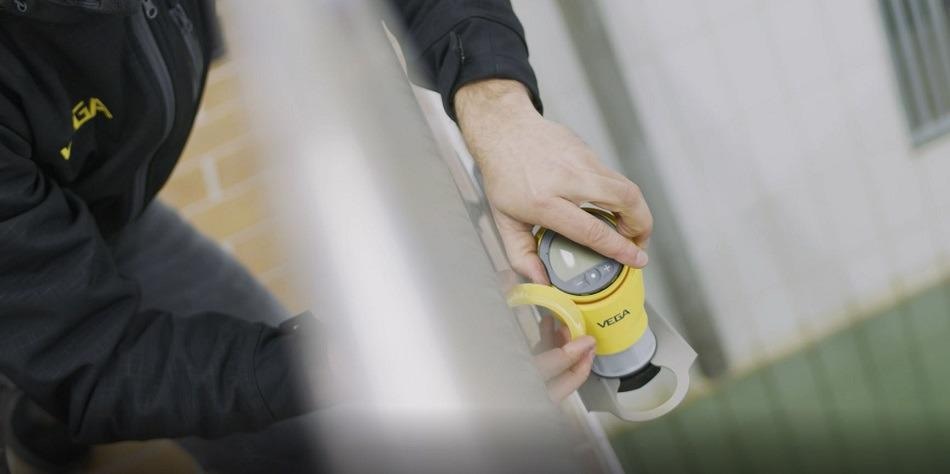
Image Credit: VEGA Grieshaber KG
Radar sensors can penetrate plastic, allowing measurements to be performed through the plastic. This is especially beneficial when working with very aggressive chemicals, IBC containers, or other portable containers. For example, it is possible to mount the radar device on the wall and measure the inside level through the surface of the plastic container.
Because IBC containers are always the same size, no re-adjustment is necessary - just place the new container in the same position and conduct the next measurement.
In the future, it may be possible to mount a sensor directly on the container, with the supplier of the chemicals taking responsibility for measuring the level in the tank. This would require the use of a battery-operated, wireless, non-contact radar device, which uses a modem to send data to cloud storage twice a day.
Then, if the tank is starting to empty, the supplier will be made aware of this and can arrange delivery of a replacement. Because measurements are taken once or twice a day, these batteries would last over ten years.
This would offer significant advantages to the supplier, who can optimize delivery route planning. Meanwhile, the user does not have to worry about chemicals running out because the supplier will be managing this.
How important is managing contamination?
Once the water has been treated, it is important to measure and manage contamination. The treated water is often stored in underground basins, and everything is clean. Because it is important to ensure no contamination enters the water, it makes sense to use a non-contact level measurement.
The sensor can be mounted on the wall or ceiling using a special mounting tool or via a stainless-steel tube where the cable is also located. Non-contact sensors are also easier to adjust, and all of our sensors and controllers have Bluetooth capabilities, which allow users to adjust the instrument using a smartphone or tablet.
People do not want to enter clean water storage areas because there is always a risk of infection, particularly currently. Staying outside to make the adjustment via a window is easier and much more comfortable.
Climbing on a chemical tank is also difficult and potentially dangerous, particularly during cold or wet weather. The distance between the sensor and the mobile equipment can be up to 50 meters, depending on the make-up of the site.
Can you give our readers an overview of VEGA’s pressure sensor range?
The drinking water industry uses a lot of pressure devices because the water is pumped between facilities and instruments. Pressure sensors and pressure monitoring are important for process monitoring and also in terms of safety and ensuring that leaks are detected and addressed rapidly.
Conventional pressure sensors have existed for many years, and this type of pressure sensor is used in many different industries, for example, the chemical industry, oil and gas industry, food and pharma industries, and the paper industry.
The drinking water industry has extremely stringent requirements, necessitating the development of new pressure sensors. VEGA has offered a new type of pressure sensor for over a year. This sensor features a compact design and robust housing, and it includes options with or without an inbuilt rotatable display.
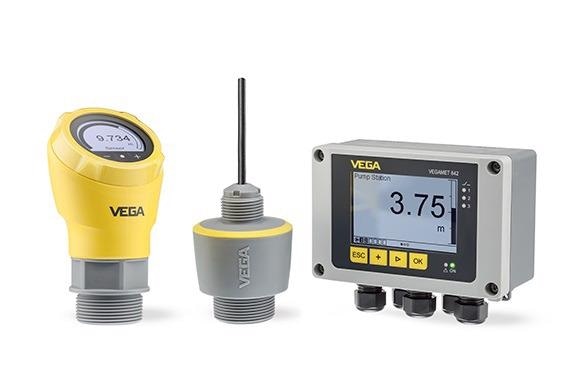
Image Credit: VEGA Grieshaber KG
Both models of sensors are available with a ceramic cell or a metallic cell. The sensor’s signal output is 4 to 20 mA, and we also offer a transistor output and IO-Link output for digital communication.
Drinking water facilities can use these kinds of sensors to monitor pressure. Colored lights show users whether or not pressure is currently at an acceptable level, and users can define what that acceptable level is.
What is the significance of pressure peaks and why is this important in drinking water measurements?
Pressure peaks occur in pipes because the pump pumps the water from one side to another side via a series of wells which may switch off or switch on. This fast-moving water results in high-pressure peaks. It is important that a sensor can accommodate these changes in pressure.
Ambient temperature can also affect water pressure, and this will impact an ultrasonic sensor much more than it would impact a radar sensor.
Every ultrasonic device will use a temperature measurement rather than the transducer in order to compensate for this influence, but this can still cause problems, for example, when the transducer is heated by the sun.
The temperature rarely stays the same and this can lead to more than 30% failure on flow measurements taken using the ultrasonic device.
Our overall goal is to replace ultrasonic devices with radar. Both technologies are at the same price point, but from a performance, perspective radar is always better and much freer from external influences.
About Jürgen Skowaisa
After military service, he studied engineering physics at the University of Applied Sciences in Heilbronn. Internship at Dornier in Immenstaad.
His employment at VEGA Grieshaber KG, Schiltach, began in 1989. First, he worked in the area of product development for laser and radar technology. As of 1996, he moved into product management for radar and ultrasonic sensors.
His responsibilities are not limited to VEGA products, but also include various sectors such as chemicals as well as bulk solids and water, wastewater.
Disclaimer: The views expressed here are those of the interviewee and do not necessarily represent the views of AZoM.com Limited (T/A) AZoNetwork, the owner and operator of this website. This disclaimer forms part of the Terms and Conditions of use of this website.