In this interview, AZoSensors talks to Manny Romero, Senior Product Manager at Teledyne Dalsa, about their latest high-speed imaging products and the possibilities these entail.
Please could you provide a brief overview of Teledyne DALSA and the work you do with high-speed imaging?
Teledyne DALSA is part of the Teledyne Imaging group of leading-edge technology companies aligned under the Teledyne umbrella. Individually, each company offers best-in-class solutions. Together, they combine and leverage each other’s strengths to provide the deepest, widest imaging and related technology portfolio in the world.
Equipment manufacturers face many challenges meeting expectations for high-speed inspection. This requires new technology enabling higher speeds and high-performance image capture. We are meeting these challenges by developing high-speed scanning and super-resolution cameras to bring improved clarity to quality inspections.
From increasing frame rates to increasing pixel size, it is about more. It is about taking bursts of images in the time it used to take for a single image, making multiple passes over a single object in parallel and capturing an entire field of vision in stunning clarity and depth.
It is also about knowing more, understanding more about the objects we are looking at so that we can analyze and classify them more completely.
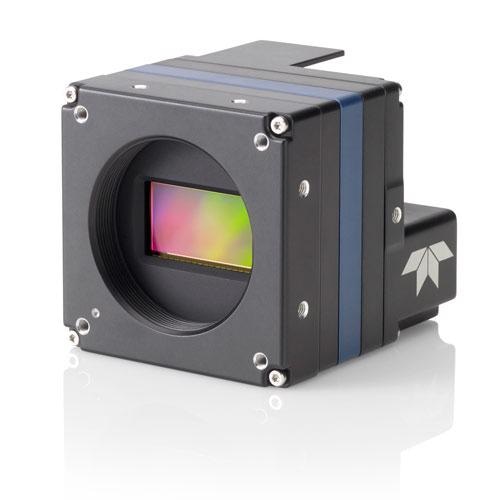
Image credit: Teledyne Dalsa
What would you say are some of the main or most important applications of high-speed imaging?
- Machine Vision
- Robotics
- Factory Automation Inspection
- Electronics manufacturing
- 3D solder paste inspection
- Package and bump inspection
- Automated Optical Inspection (AOI)
- Semiconductor wafer inspection
- Surface and bump inspection
- Solar panel inspection
- Motion Tracking and Analysis
- High-Speed 3D imaging
Which capabilities and features make the Falcon4-CLHS and the Genie Nano-CXP strong choices for any high-speed imaging needs?
Genie Nano-CXP’s latest 67 and 37 MP CMOS versions use the new Teledyne e2v Emerald sensors, which enable more objects to be captured in a single high-resolution shot.
With Genie Nano’s CoaXPress 6.25 Gbps technology, cameras can reach incredible speeds over longer distances. With higher-end coax cables, CoaxPress can send power and data all through a single cable.
The latest Falcon4-CLHS 11.2M model uses Teledyne DALSA’s advanced CMOS architecture and has a frame rate of up to 609 fps, delivering over 12 times faster frame rates than the typical 4KHD camera. This model can reach multiple thousand frames per second in partial scan mode.
The Falcon4-CLHS leverages standard cabling technology such as CX4 and fiber optic (AOC) cables to maximize length and speed.
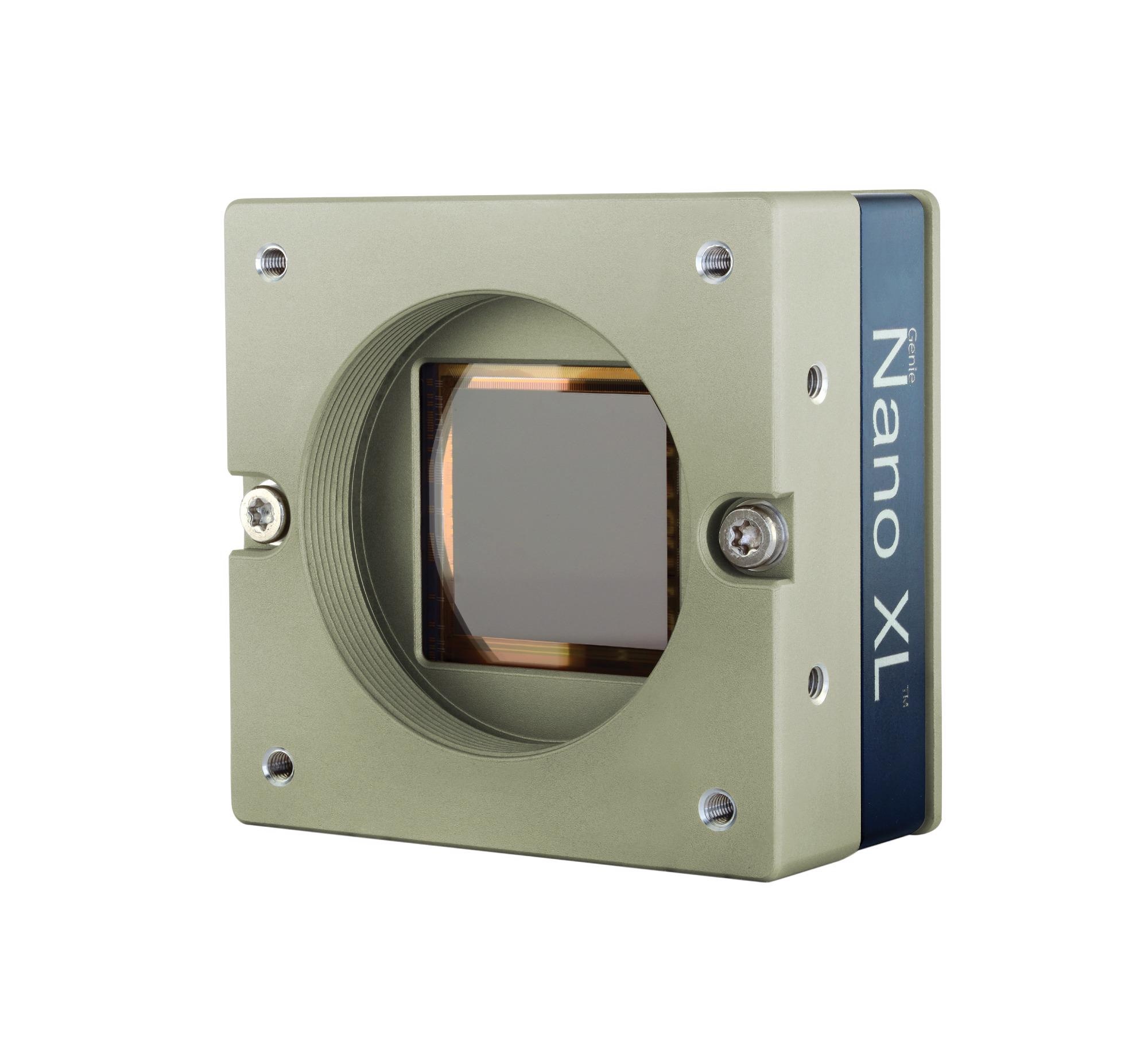
Image credit: Teledyne Dalsa
On a similar note, how are the products able to cover such a wide range of applications with presumably vastly different requirements?
Both the Genie Nano-CXP and Falcon4-CLHS feature CMOS sensor architectures that deliver unmatched speed and sensitivity for high-speed machine vision applications like defect detection, part measurement, semiconductor inspection, electronics manufacturing, etc.
By incorporating CMOS sensors with multiple megapixels in our high-speed cameras, manufacturers are able to achieve exceptional image quality while getting more detailed inspections resulting in higher yields.
In addition, these cameras support CoaXPress (CXP) or Camera Link HS (CLHS) technology. CoaXPress enables the camera to transfer vast amounts of data to our Xtium™ and Xtium2™ frame grabbers in real-time.
By enabling maximum sustained throughput and ready-to-use image data, the Xtium series minimizes CPU usage and improves processing times for the host applications.
Our Camera Link HS technology is specifically engineered for industrial imaging applications delivering thousands of frames per second in Partial Scan Mode (ROI). In-sensor binning also allows the camera to have a large full well greater than 160Ke. This makes the new camera ideal for high-speed 3D imaging and factory automation inspection applications.
How does Teledyne approach the development process for these high-speed cameras and sensors?
We look to the market and the voice of the customer to guide us in our imaging solution development. We have the resources and ability to develop a wide variety of imaging solutions, but being able to provide solutions that solve real problems (challenging problems) is our core goal.
As part of our development process, ease of use is key. We want to ensure that our customers can easily integrate our technology into their imaging systems. This means that everything needs to be as clear, intuitive and logical as possible.
This includes our camera design, software, documentation, support and everywhere our customers interact with our products and our organization.
We also want to provide our customers with the flexibility to evolve with Teledyne Imaging as their systems needs and technology needs evolve. This means straightforward migrations to new sensors and even interface technology as needed.
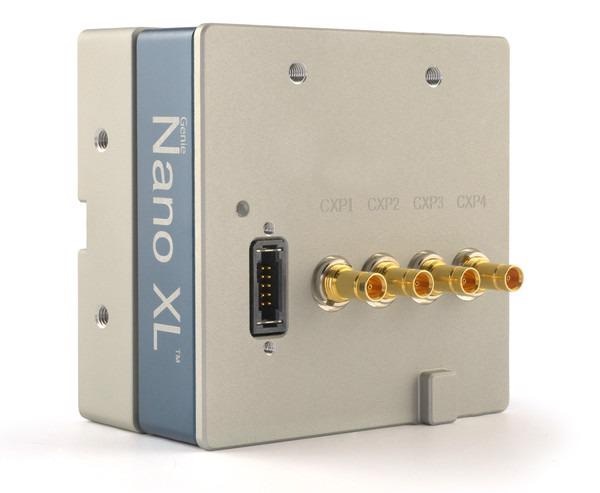
Image credit: Teledyne Dalsa
Where do you see the future of high-speed imaging going?
We continue to see the future of high-speed imaging expanding in applications such as semiconductor wafers, printed circuit boards and 3D printing. In addition, we see many other industries using high-speed imaging, including intelligent traffic systems, aerial mapping, railroad inspection, motion tracking and analysis, to name a few.
About the interviewee
Manny Romero is Senior Product Manager at Teledyne DALSA and Teledyne Lumenera for Machine Vision 2D cameras. With 23 years of machine vision industry experience in roles from R&D to strategic product development, Manny brings deep expertise in image acquisition systems, communication protocols and camera platform design.
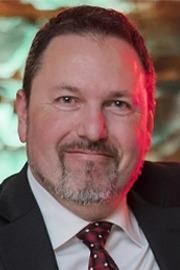

This information has been sourced, reviewed and adapted from materials provided by Teledyne DALSA.
For more information on this source, please visit Teledyne DALSA.
Disclaimer: The views expressed here are those of the interviewee and do not necessarily represent the views of AZoM.com Limited (T/A) AZoNetwork, the owner and operator of this website. This disclaimer forms part of the Terms and Conditions of use of this website.