Separating the emulsions from water and oil is a critical process in the production of petroleum. Whenever oil and water are present together, it almost always results in emulsions that entail extra treatment processes.
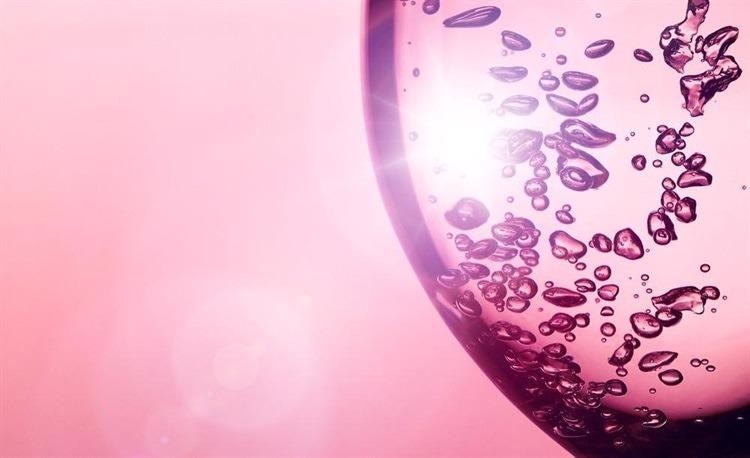
Image Credit: OlegRi/Shutterstock.com
The formation of water and oil emulsions presents multiple interface level measurement challenges because a layer of emulsion shows up between the aqueous and organic layers. In petroleum, gas, and hydrometallurgical production fields, solvent extraction devices, also termed contactors, are essential.
Solvent extraction is a crucial process commonly used in recovering and purifying metals and oxides from their parent ores and in the purifying process of oil products. As a result, it is one of the most significant processes across the hydrometallurgical and petroleum sectors.
Various other industries, including chemical, food processing, and agricultural industries, also require separation vessels in which tracking the location of the interface and the liquid level is important.
How Do Contactors Work?
The fundamental concept behind the working of a contactor is the formation of a dispersion of one of the phases into the other, thereby producing a relatively greater specific interfacial area. This interfacial area serves as the pathway for mass transfer of the relevant solute to take place, allowing it to be recovered and purified of any contaminants. Then, segregation of the two phases occurs for downstream processing.
To achieve the extraction of solvent on an industrial level, a myriad of different contactors have been created and used, including mixer-settlers, annular centrifugal extractors, gravity settlers, rotating disc contactors, and pulsed columns.
Settlers are classified as gravity or centrifugal settlers, depending on the key driver for phase disengagement. The names are self-explanatory: in the former, phase separation is accomplished only by gravity, but as for the latter, it is accomplished with centrifugal force.
The disadvantage of centrifugal settlers is that they are very power-consuming, costly, and require a lot of upkeep; thus, they should only be utilized when gravity settlers are not an option. Hence, gravity settlers are the most popular choice of settler for use in hydrometallurgical processes when the suspensions can be separated comfortably by the help of gravity.
The principle of gravity settling is also utilized for phase disengagement in variable contactors such as pulsed columns, rotating disc contactors (RDCs), and so on. For the proper working of these gravity-based settler machines, precise estimation and regulation of the two-phase interface is required. Because these settlers work continuously, it is imperative to have constant online monitoring and adjustment of the two-liquid interface to prevent any possibilities of entrapment of one phase in the other.
Mechanisms for Interface Detection
Three kinds of specialized instrument systems can be used for interface discernment between two liquids in gravity settlers: first is a single probe using the concept of a clean or uncontaminated nexus, second is a segmented probe with a number of detectors that cover the entire depth of the settler machine, and finally, industrial tomography.
Although the segmented and the tomographic types tend to provide comprehensive details about how the two phases are distributed within the container, such systems are complex and costly to design, construct, and operate.
Single probe systems are favorable in terms of decreased cost and hassle for estimating the nexus of the two liquids in disengagement portions of solvent extracting devices used in the hydrometallurgical and petroleum sectors.
Various researchers have employed ultrasonic probes to test liquid interfaces. Almost always, the approach used involves the determination of the location of the interface by estimating the signal's duration of flight, but this approach necessitates the awareness of the acoustic speed in the respective media apriori.
Self-Calibrating Sensors and Ultrasonic Testing
Behnia et al. (2019) described a self-calibrating sensor installed on a directed float in a gravity settling tank that monitors the acoustic speed in the oil portion and utilizes it to determine the whereabouts of the nexus (or the interface).
However, in the presence of interface-seeking pollutants, the reliability of the algorithm for analyzing the signals was not considered.
Mukherjee et al. (2021) use a signal reading approach that is complex and robust to extend the application to more complicated practical instances, such as liquid-liquid junctions polluted by emulsified layers or particle contaminants.
The acquired ultrasonic testing (UT) signal is analyzed in real-time using a unique algorithm to determine both the acoustic speed in the oil phase and the nexus point. Because the entire container dimensions are specified, the algorithm is also capable of computing the acoustic speed through the water phase.
The designed algorithm is demonstrated to be sufficiently robust to handle information even with contaminants present to determine the nexus point of two liquids with unparalleled accuracy. When the UT signal is reflected back from the two-phase junction, its signature can be distinguished by the algorithm, enabling it to utilize this data to identify it among other reflected signals.
This was accomplished through the use of matched filter methods.
Continue reading: Electric Vehicle Sensors for Leak Detection.
References and Further Reading
Abbate, A., Koay, J., Frankel, J., Schroeder, S. C., & Das, P. (1997). Signal Detection and Noise Suppression Using a Wavelet Transform Signal Processor: Application to Ultrasonic Flaw Detection. IEEE Transactions on Ultrasonics, Ferroelectrics, and Frequency Control, 14-26. Available at: https://ieeexplore.ieee.org/document/585186
Alshaafi, E., Prakash, A., & Mercer, S. (2019). Ultrasonic technique for tracking oil-water emulsion layer in separation vessels. Journal of Petroleum Science and Engineering. Available at: https://www.sciencedirect.com/science/article/pii/S0920410519310125
Behnia, I. P. (2019). Ultrasonic based technique for monitoring oil layer height and interface position in separator vessels. Can. J. Chem. Eng., 115-122. Available at: https://www.sciencedirect.com/science/article/pii/S0920410519310125?via%3Dihub
Mukherjee, D., Sen, N., Singh, K., Saha, S., Shenoy, K., & Marathe, P. (2021). Automated interface detection in liquid-liquid systems using self-calibrating ultrasonic sensor. Chemical Engineering Science. Available at: https://www.sciencedirect.com/science/article/pii/S0009250921000750
Disclaimer: The views expressed here are those of the author expressed in their private capacity and do not necessarily represent the views of AZoM.com Limited T/A AZoNetwork the owner and operator of this website. This disclaimer forms part of the Terms and conditions of use of this website.