Critical parts refer to all components in machines, including wires, whose failure might result in a problematic situation. Sensors are vital in managing and protecting critical machine components.
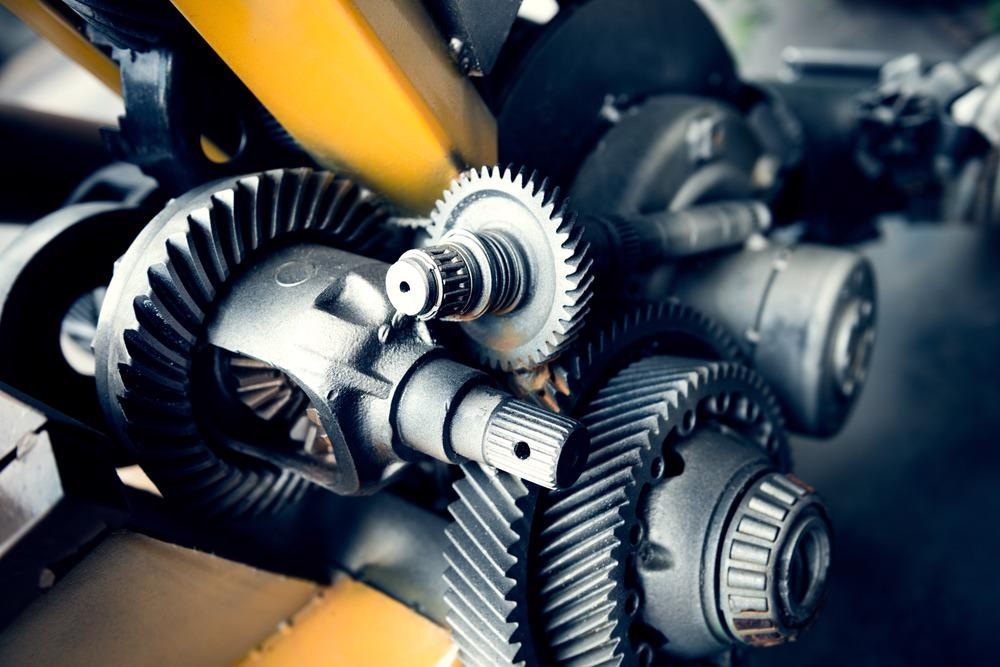
Image Credit: fuyu liu/Shutterstock.com
What are Critical Parts in Machines?
Critical parts in machines are those components that, if they malfunction or get defective, have a disastrous effect on the performance of machinery or jeopardize the end user's safety.
As a result, key components are often subject to extensive quality frameworks, and many sectors have market-specific criteria aimed to guarantee that devices and applications operate effectively while simultaneously optimizing user or customer safety.
Critical component manufacturers must constantly provide very precise components that adhere to industry-specific rules, which has frequently been linked with the high cost of production and lengthy lead times. Identifying the optimal qualities of important parts is critical for choosing the best materials for a specific application.
High-temperature components will almost certainly need a different material than those that require some degree of flexibility or fracture toughness. Engineers can easily discover the material or group of materials that will produce the ideal component for an application by specifying the exact pressures, stresses, or characteristics required of the part.
The landing gear is an example of a critical part of airplanes in the aviation sector. In turbines, the blades used are the most vital parts. Generally speaking, motors, power supply, fuses, circuit breakers, connectors and batteries are all considered important machine parts, where failure results in the overall dysfunction of the machine.
Utilization of Sensors for Monitoring and Protecting Critical Machine Parts
Sensors are used in the industrial sector to analyze the performance of complicated components and critical parts of machines, gathering data to establish typical operating parameters while also detecting even the smallest variations in that performance.
This data may subsequently be used to allow more efficient and appropriate predictive maintenance, avoid downtime and keep equipment operating. Some examples of sensors used for monitoring and protecting critical parts of machinery are presented ahead.
Temperature is among the most dependable indications of the performance of any machine. In general, equipment should function at a constant temperature, with cooling devices (such as coolant, ventilation, or fluid) in place to ensure consistency.
Temperature sensors are used to monitor the temperature changes in parts of machinery. They detect sudden and uncontrollable temperature changes or increases and indicate if something in a critical part of the machinery is not performing at peak efficiency.
MEMS sensors are a sort of motion detector that enable the tracking of activities and effectiveness with almost any type of moving part. One of the most popular applications of these sensors is in car airbags, where they may significantly increase safety when paired with the capacity to transmit a signal upon activation.
Triaxial accelerometer sensors are used to detect vibration on rotating machinery and provide data on velocity, force, and movement. This data is important for determining the consistency of critical parts' vibration ups and downs. If vibrations occur predictably, it is reasonable to infer that the machine is running normally. If there are variations or departures from a constant vibration reading, this nearly generally indicates that the machine is not performing properly, and that extensive review (and repair) is necessary.
Vibration Sensors for Detecting Failure of Critical Machine Parts
Isolators, cooling systems, compressors, motors, pumps, valves, and actuators often indicate that they are defective and likely to malfunction. When a fan gets imbalanced or the bearings fail, the fan begins to vibrate excessively. Although this shift would be imperceptible to the human eye or ear, a vibration sensor can readily detect it.
A remote monitoring system, such as the Sensaphone Sentinel, utilizes sensors to detect abnormal vibration. They identify damage early on, allowing one to take preventative measures and avert a complete failure. A Sensaphone vibration sensor monitors the oscillation velocity (i.e., the intensity of movement) of a machine across the frequency range of 0-25 mm/s (RMS). A 4 mA output equates to 0 mm/sec (i.e. no vibration), whereas a 20 mA output equates to 25 mm/sec (intense vibration).
Radar Sensor Solution for Wear Control in Critical Machine Parts
Ondosense's IoT radar sensor continuously checks the wear of critical machine components in combined heat and power facilities. The sensor system monitors crucial components wear during the operation.
The OndoSense sensor software's algorithms can monitor the state of the critical mechanical parts and the system's status in real-time. This allows advanced predictive cycle planning, ensuring that the operator only performs maintenance when it is essential.
The consequence of the predictive maintenance solution is a reduction of up to 60% in maintenance expenses and a reduction in downtime and operational costs. Simultaneously, the plant's energy output rapidly rises.
Benefits of Utilization of Sensors for Monitoring Critical Machine Parts
Sensors act as an early warning system when a critical product part of a machine is defective. By delivering an alarm as soon as they notice unusual behavior, they assist in fixing problems before they become severe.
Sensors also decrease downtime and boost the productivity of the machine by detecting failure and delivering real-time information about critical machine components.
References and Further Reading
Correa, J. C., & Guzman, A. A. (2020). Fundamentals of mechanical vibrations. In Mechanical Vibrations and Condition Monitoring (pp. 1-26). Academic Press. https://doi.org/10.1016/B978-0-12-819796-7.00001-9
Ondosense. (2022). Save 60% on maintenance costs – with predictive maintenance. Available at: https://ondosense.com/en/applications/predictive-maintenance-energy-industry/.
Sensaphone. (2016). Vibration Sensors Alert You When Critical Machine Parts are Failing. Available at: https://blog.sensaphone.com/vibration-sensors-provide-early-warning-of-critical-machine-part-failures.
Disclaimer: The views expressed here are those of the author expressed in their private capacity and do not necessarily represent the views of AZoM.com Limited T/A AZoNetwork the owner and operator of this website. This disclaimer forms part of the Terms and conditions of use of this website.