Since its founding more than 170 years ago, the independent family company LEIPA GROUP has advocated for environmentally friendly paper and packaging techniques and technologies that are 100% recyclable.
The LEIPA FlexPack business unit, together with the carton board and specialty paper segments, are among the spectrum of commercial operations carried out in Schrobenhausen, where the company was created. The latter offers paper-based flexible packaging options.
The “classic product” for safely preserving priceless items in boxes and packaging is a LEIPA multi-ply grey carton board. It is also a popular standard approach for hardbound books or pallet covers. Environmentally friendly material with grammages ranging from 300 to an astonishing 950 g/m2 is incredibly robust and sturdy and is utilized in various applications.
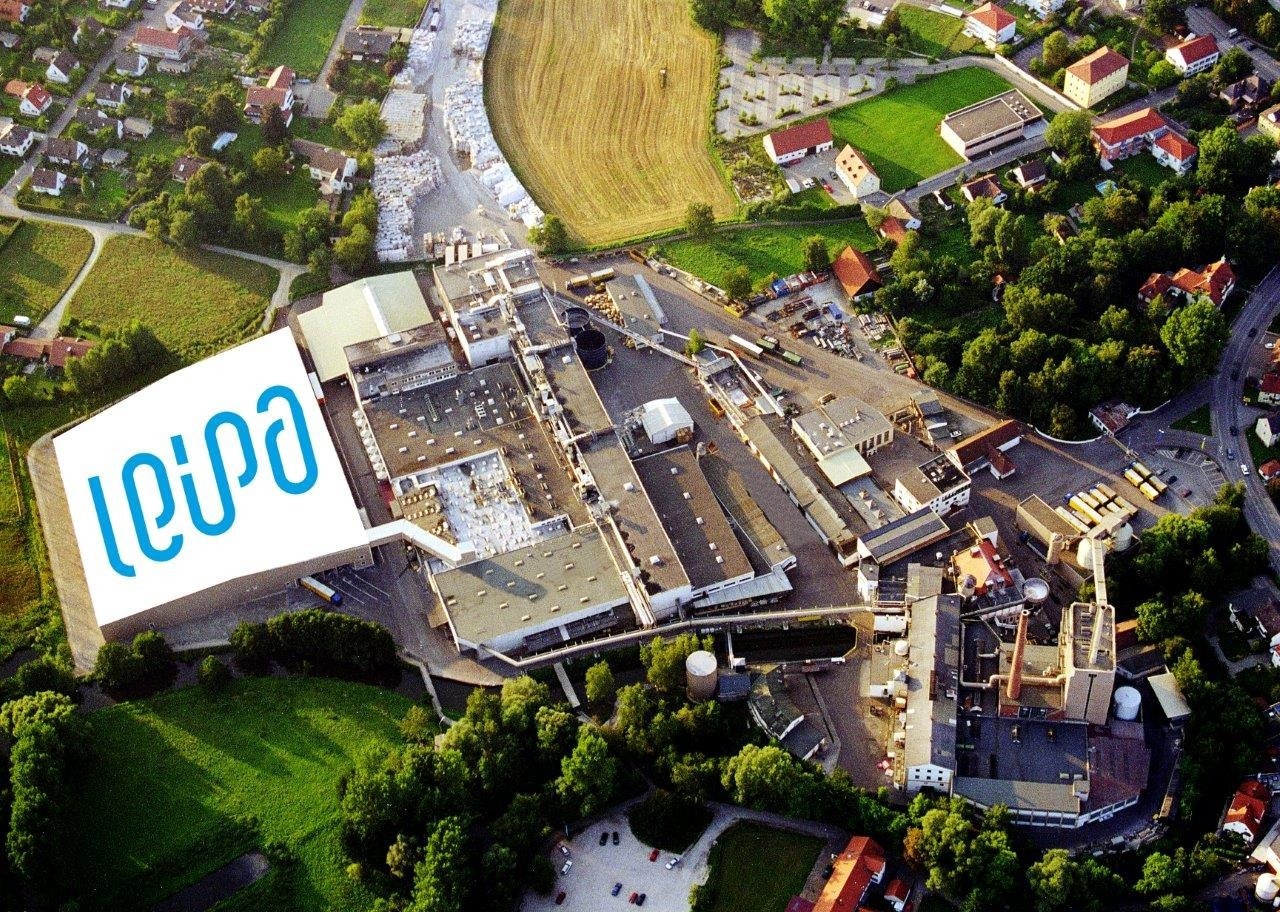
Image Credit: VEGA Grieshaber KG
The top, interlining, and back layers of the carton board machine at the Schrobenhausen site were originally supplied by three distinct stock preparation lines, one for each layer. The expenditures associated with running and maintaining the threefold system technology and the percentage of foreign objects and dirt in the recycled paper used were rising.
The company began a thorough modernization project, integrating the three stock preparation lines into one and investing in new plant components and substantial automation technologies.
The four key objectives were to raise operational dependability, use new technologies to increase production’s cost-effectiveness, lower maintenance expenses, and enhance drinking quality.
A high level of automation is essential in a modern stock preparation system that demands availability around the clock throughout the year. A cutting-edge control system and the appropriate sensors guarantee this.
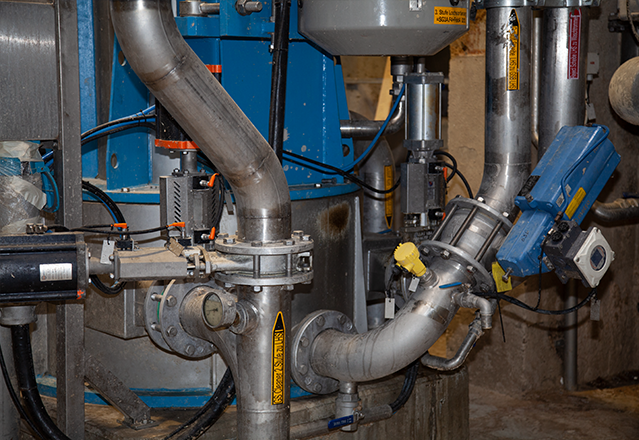
Image Credit: VEGA Grieshaber KG
The VEGABAR 82 pressure transmitter was chosen as the standard instrument for level and pressure measurement in the new stock preparation system due to the positive experiences the company had previously had with VEGA sensors. The devices’ resilience and ease of on-site adjustment were additional key factors.
The used measurement technique, particularly in processing recovered paper, is susceptible to extremely high mechanical stresses caused by abrasive residues in the suspension, refiner, or standpipe vibration, in addition to hydraulic shock caused by the rapidly closing valves.
Variable stock densities and agitators in vats and stock towers are additional challenges that each measuring system must overcome. Additional considerations include cleaning the inside of equipment components with aggressive chemicals and cleaning the exterior with high-pressure cleaners.
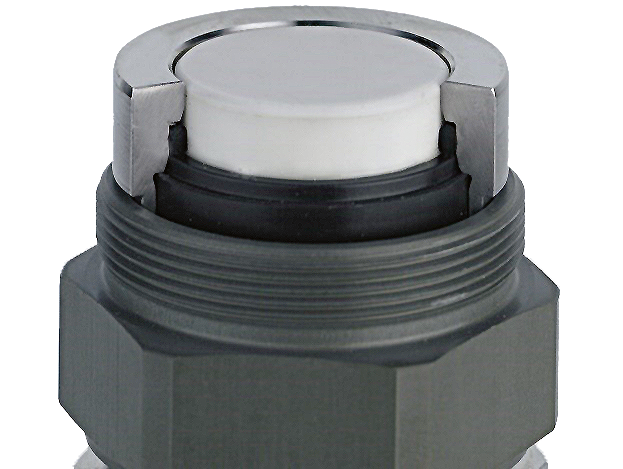
Image Credit: VEGA Grieshaber KG
Despite these challenging circumstances, sensors must be able to measure accurately and consistently. Early on, VEGA recognized the benefits of durable ceramic and developed a sophisticated sensor design using the dry, capacitive measuring cell CERTEC®.
The diaphragm is made of high-purity alumina ceramic (99.9% Al2O3), which is second only to diamond in terms of hardness. This provides the extended service life necessary for profitable continuous operation while protecting against abrasion, particularly in cleaners.
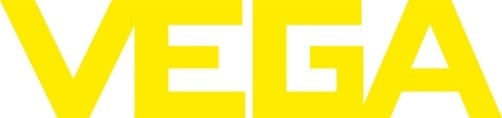
This information has been sourced, reviewed and adapted from materials provided by VEGA Grieshaber KG.
For more information on this source, please visit VEGA Grieshaber KG.