In the swiftly advancing realm of manufacturing, the Internet of Things (IoT) has transitioned to an industry game-changer. AI, wearables, and 3D printing are among the tools propelling transformative applications of IoT in manufacturing, offering significant returns on investment. This article delves into the historical context of IoT in manufacturing while providing real-life case studies to anticipate upcoming trends.
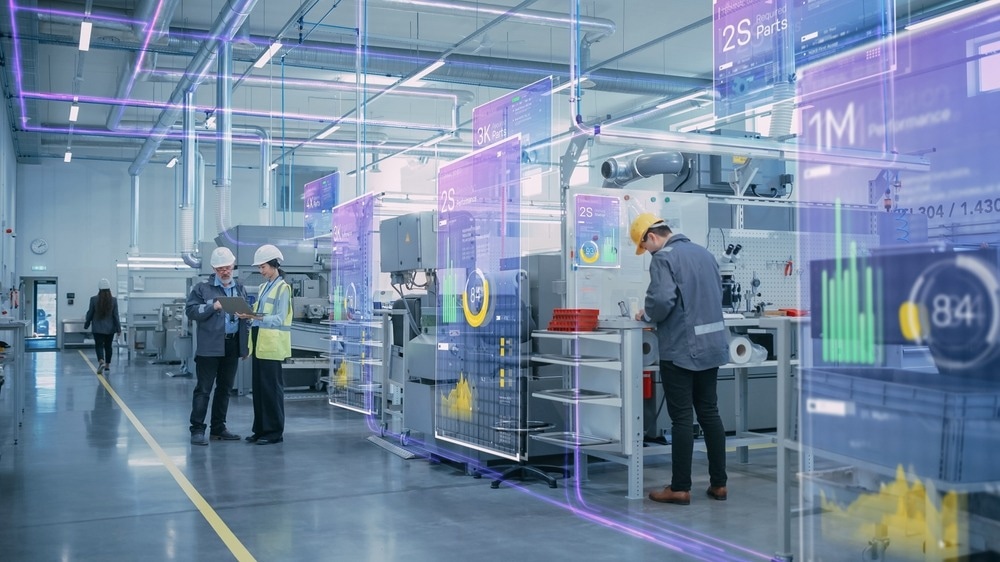
Image Credit: Gorodenkoff/Shutterstock.com
IoT in Manufacturing: A Historical Perspective
Today, the term "Internet of Things" (IoT) refers to Internet or network-connected devices that lack a web GUI. These devices are equipped with sensors, software, and technology, enabling them to exchange significant data with other devices online. Common examples of IoT include smart devices and personal digital assistants.
IoT has proven invaluable in streamlining our personal lives and enhancing organizational daily operations. These devices can monitor activities, track progress, optimize efficiency, and provide companies with crucial information for making informed business decisions. IoT in manufacturing solutions enables companies to gain operational insights, thus tailoring marketing strategies for maximizing ROI.
While smart devices are relatively recent, the utilization of IoT in manufacturing dates back several decades. As early as 1968, General Motors implemented a programmable logic controller (PLC) in their automatic transmissions manufacturing division, even before the internet was widely accessible. Subsequently, machine-to-machine devices integrated telephony and computing to further enhance manufacturing efficiency.
In 1999, the term "Internet of Things," was coined to include all devices capable of connecting to the Internet without a graphical interface. In recent years, the Industrial Internet of Things (IIoT) has become extremely important in every major industry worldwide, including manufacturing.
IoT in Manufacturing: The Current Landscape
Today, IoT in manufacturing plays a massive role in optimizing operations, asset tracking, collecting data, and predictive maintenance, providing many advantages.
The integration of IoT in manufacturing processes can lead to numerous cost-saving benefits. These IoT in manufacturing technologies optimize inventory and asset management, lower search times, reduce machine downtime, and improve daily operations, contributing to enhanced energy efficiency. Each of these individual benefits can independently lower operational costs and their combined effect results in substantial reductions in monthly and yearly expenditures for companies.
Efficiency can be greatly improved by using IoT in manufacturing tools, creating a network with minimal human interference. This enables manufacturers to automate a majority of processes, leading to quicker problem identification, improved performance, and reduced operation time, sometimes even from days to a handful of hours. Faster production leads to shorter time-to-market, reducing product cycle time and potentially increasing revenue.
Safety in the workplace is of utmost importance in the manufacturing industry. IoT in manufacturing systems, such as wearable devices, can monitor the health and risk activities of workers on manufacturing floors, leading to increased safety measures. For industries dealing with hazardous materials, IoT in manufacturing could also include monitoring devices on containers to ensure no leaks during transport.
IoT in Manufacturing: Kaeser’s Digital Twins
In the context of IoT in manufacturing applications, a digital twin virtually represents an object or system, covering its entire lifecycle and receiving real-time updates from data. It utilizes simulation, machine learning, and reasoning to aid in decision-making.
With Digital Twins, manufacturers can create robust virtual replicas of physical objects, proving beneficial in the manufacturing process. With virtual copies of equipment and spare parts, managers can simulate processes, identify and address issues, and achieve desired outcomes without risking physical assets.
Coburg-based Kaeser Kompressoren SE, a prominent manufacturing company and provider of compressed air products, leveraged digital twins as an IoT in manufacturing tool to transform its business model from product-selling to service-selling. This IoT in manufacturing technology supplies Kaeser with operational statistics on the equipment during its lifecycle, specifically the air consumption rates.
Because of this monitoring, Kaeser was able to charge clients based on real air usage rather than a predetermined fee, resulting in a 30% savings in commodity prices. Additionally, implementing digital twins led to the successful onboarding of nearly half of all major vendors.
IoT in Manufacturing: Armal’s Remote Monitoring
Remote monitoring represents a compelling application of IoT in manufacturing. For manufacturers with industrial assets, it enables continuous monitoring of equipment usage and health, facilitating performance assessment. Additionally, IoT sensors play a crucial role in promptly deploying services to address any issues that may arise. This innovative approach opens up new possibilities for an Equipment-as-a-Service business model.
Armal, a prominent manufacturer of portable toilets, relies on molding equipment to produce plastic frames and components for their products. Its objective was to optimize power consumption by closely monitoring the machinery. It could remotely measure power use throughout the whole manufacturing cycle by utilizing IoT sensors and industrial software.
Implementing a real-time IoT monitoring system along the manufacturing line produced outstanding results, lowering machinery energy expenditures by over 40%. As a result, Armal concluded its digitalization journey by implementing an IoT system that can provide real-time power data for each unit.
IoT in Manufacturing: Amazon’s Logistics Management
Logistics in manufacturing companies pose risks due to uncontrollable weather conditions, a high potential for fraud, and the management of numerous assets. For businesses heavily reliant on transportation, adopting IoT-enabled interconnections between devices and systems can be advantageous.
IoT in manufacturing applications for logistics covers various use cases throughout the supply chain, encompassing warehousing, fleet management, and cargo tracking. Amazon, as a company, has experienced benefits by utilizing standalone drop shipping bots and lockers, which enhance delivery convenience and boost profitability, ultimately leading to reduced shipping costs.
By implementing automatic order processing and status updates using IoT in manufacturing tools, Amazon has successfully minimized the need for large delivery staff and decreased overall operating expenses. The utilization of connected bots for last-mile delivery further contributes to cost reduction and heightened customer satisfaction.
IoT in Manufacturing: The Future
Opportunities for lucrative growth are being presented by IoT in manufacturing. Leading players in the industry are already exploring niche technologies to capitalize on digitization and optimize its benefits. This is primarily because IoT in manufacturing is quickly becoming a prerequisite for transforming conventional factories into intelligent and efficient smart spaces.
The implementation of IoT in manufacturing is causing significant disruption and has the potential to enhance the safety of frontline workers while simultaneously increasing overall productivity and efficiency. According to experts, the global IoT in the manufacturing market is projected to experience substantial growth, with its size expected to rise from USD 33.2 billion in 2020 to USD 53.8 billion by 2025, exhibiting a Compound Annual Growth Rate (CAGR) of 10.1%.
It is evident that the IoT in the manufacturing industry will make noticeable strides in the near future. Manufacturers are keen to adopt interconnected and intelligent manufacturing systems, moving toward a new level of production efficiency.
References and Further Reading
Element14. (2017, June 14). Amazon – a prime example of an IoT implementation. Retrieved from https://in.element14.com/amazon-a-prime-example-of-an-iot-implementation
Hannover Messe. (2018, April 5). Kaeser digitally replicates its compressors. Retrieved from https://www.hannovermesse.de/en/news/news-articles/kaeser-digitally-replicates-its-compressors
OutSource IT Solutions. (2023). The Rise of IoT in Manufacturing. Retrieved from https://www.osgusa.com/iot-in-manufacturing/
Peranzo, P. (2023, May 29). How is IoT Used in Manufacturing: 8 Use Cases and Upcoming Trends. Retrieved from Imaginovation: https://imaginovation.net/blog/iot-in-manufacturing/
Zerynth. (2023). Case study | Industrial IoT for monitoring production. Retrieved from https://zerynth.com/customers/case-studies/armal/
Disclaimer: The views expressed here are those of the author expressed in their private capacity and do not necessarily represent the views of AZoM.com Limited T/A AZoNetwork the owner and operator of this website. This disclaimer forms part of the Terms and conditions of use of this website.