Thermal sensors can be used to ensure the optimal performance of industrial devices, monitoring for changes in temperature that could limit function.
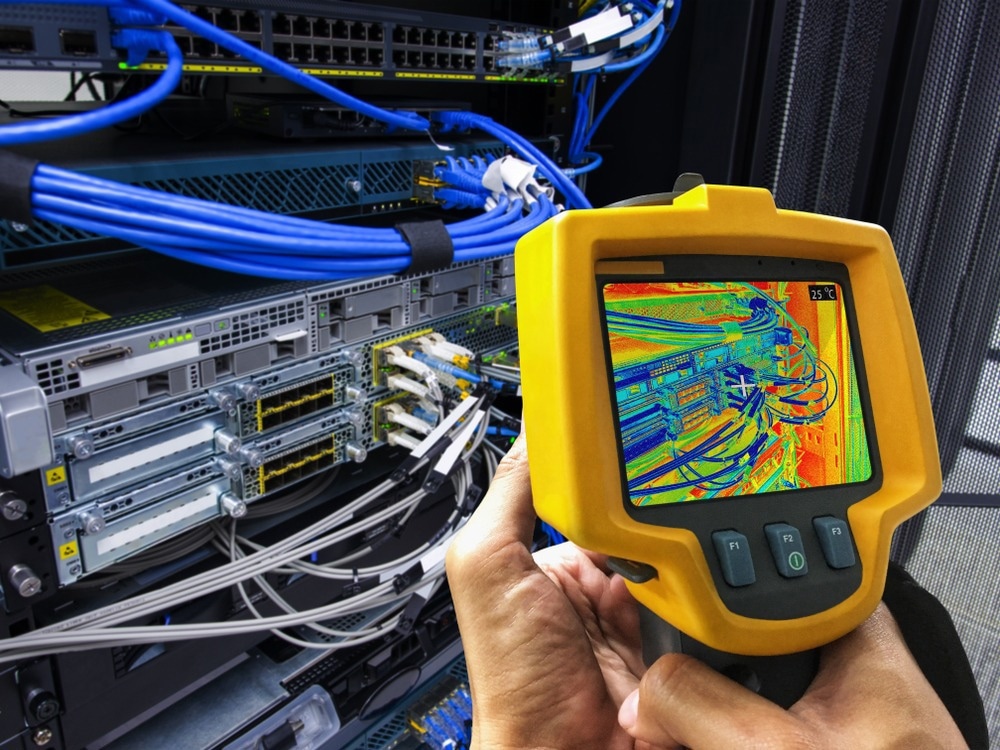
Image Credit: Yentafern/Shutterstock.com
Thermal Sensors and Device Performance Monitoring
A thermal sensor is primarily a device that can measure temperature variations in a system/space by detecting the changes in the electrical properties of the sensor material. In industrial settings, temperature control and measurement have become crucial for monitoring industrial processes as several industrial applications require accurate and continuous temperature control, which can be effectively realized using thermal sensors.
Optimal operating temperature can improve the efficiency, reliability, and performance of industrial processes and the quality of final products, ensure safety, and lead to substantial cost savings. Thermocouples are used extensively as thermal sensors in different applications, including industrial and automotive.
Thermal Sensor Types
Thermocouples
Thermocouples are nonlinear thermal sensors that operate based on the Seebeck effect principle in which the difference in temperature between two different metal wires generates a voltage difference, which is proportional to the changes in the temperature.
The voltage difference is converted to temperature measurements using a look-up table. The temperature ranges and sensitivities of thermocouples vary depending on the types of metals bound together. Although thermocouples have a low accuracy, they can operate across an extensive temperature range from -200 ℃ to 1750 ℃.
Resistance Temperature Detectors (RTD)
RTDs measure the temperature variations based on the changes in the resistance of the sensing material. Thus, these types of thermal sensors require materials with a well-defined temperature-resistance relationship.
Platinum is the most suitable material for RTDs due to its linear relationship between temperature variation and resistance change. Additionally, platinum RTDs are accurate, stable, and have repeatability in measurements within -270 ℃ to 850 ℃ temperature range. Although copper and nickel can be utilized in RTDs, the accuracy attained using these materials is lower than platinum.
Thermistors
Thermistors also measure temperature based on the changes in the resistance. These devices utilize ceramic or polymer materials in place of platinum, which makes them cheaper than RTDs. However, the use of such materials also makes thermistors less accurate than RTDs.
Negative temperature coefficient (NTC) thermistors and positive temperature coefficient (PTC) thermistors are the key thermistor types. In NTC, the resistance change is inversely proportional to the temperature variation, while in PTC, the resistance change is directly proportional to temperature variation. Thermistors can operate between -200 °C and 500 °C temperatures.
Infrared (IR) Sensors
An IR sensor is primarily an electronic sensor that detects temperatures by emitting IR radiations. These sensors are non-contacting type thermal sensors. Expensive IR sensors typically display a higher accuracy compared to cheaper IR sensors.
Why is Temperature Monitoring Important in Industry?
Machinery and equipment will function the most optimally when kept within an acceptable temperature range. Technicians can prevent performance issues in advance by monitoring the temperature levels, as both underheating and overheating can significantly impact the equipment/machinery efficiency, performance, and service life, and lead to expensive repairs.
Chemical processing, power generation, food processing, pharmaceutical production, and semiconductor manufacturing are some real-world industrial processes where temperature control is a crucial requirement.
Integrating Thermal Sensors in Device Performance Monitoring Systems
Thermal sensors can be integrated into device performance monitoring systems through direct connection, wireless connection, network connection, and cloud-based connection. In direct connection, a cable is used to directly connect the thermal sensor to the monitoring system. Direct connection is the simplest method to integrate thermal sensors and is used extensively to integrate thermal sensors.
Wireless connection involves connecting the thermal sensor with the monitoring system using a Bluetooth or radio-frequency (RF) connection, which allows the installation of thermal sensors in remote locations where direct connection cannot be used.
In network connection, the thermal sensor is connected to the system over a network, such as a Wi-Fi or Ethernet network. This integration allows access to the thermal sensor from any location.
Cloud-based connection involves connecting thermal sensors to a cloud-based monitoring system. Thus, the method enables remote monitoring of the thermal sensor. Modbus, Ethernet, Wi-Fi, and Bluetooth are the communication protocols used for temperature data transmission to the monitoring systems for analysis.
Thermal sensors are compatible with modern industrial Internet of Things (IIoT) frameworks. These sensors can be integrated into the frameworks through direct connection or by connecting to a gateway that transmits the data collected by the sensors to the frameworks.
The data obtained from the sensor after connecting the sensor to the IIoT framework can be utilized to monitor the target object's temperature and detect potential problems to avoid equipment damage.
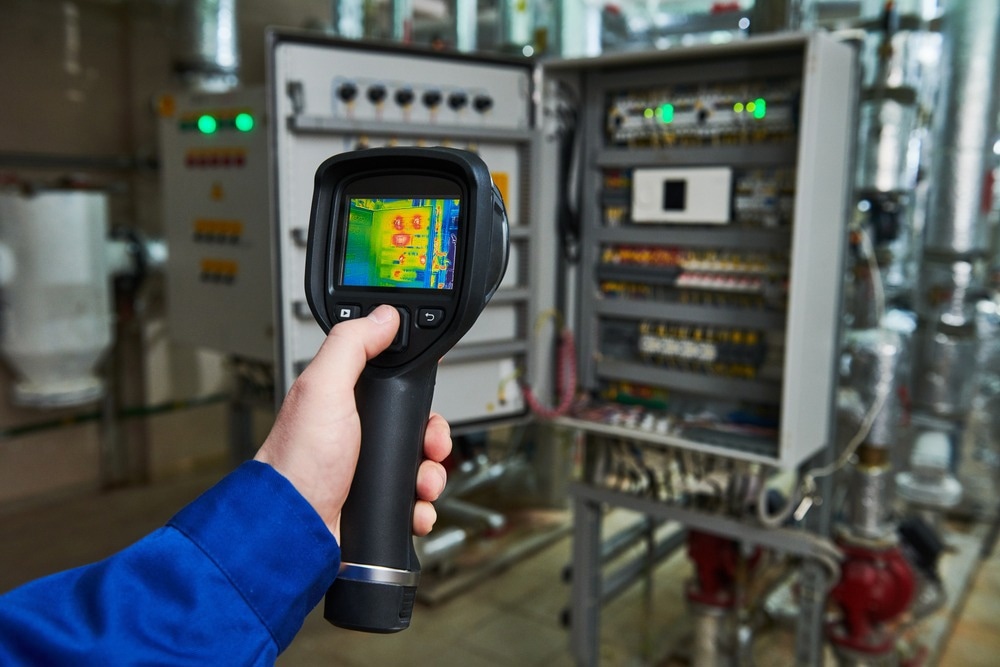
Image Credit: Dmitry Kalinovsky/Shutterstock.com
Benefits and Challenges of Thermal Sensor-Enabled Performance Monitoring
Temperature monitoring can decrease the risk of costly equipment failure and downtime through early fault detection by identifying temperature fluctuations that indicate a potential problem in an industrial device. Equipment breakdowns result in production delays, higher maintenance expenses, and reduced output.
Thus, predictive maintenance using thermal sensor data is crucial to ensure the longevity, performance, and efficiency of industrial devices. Moreover, expenses on energy can be reduced substantially by minimizing energy expenditures and usage when the equipment is kept at its optimal temperature.
However, challenges related to sensor calibration, sensor placement optimization, and the ability of the sensors to withstand severe industrial environments are the main problems thermal sensor-enabled monitoring faces.
Although thermal sensor calibration is crucial to ensure measurement accuracy, the calibration is difficult due to the intangibility of temperature, which necessitates repeated calibration of the sensor.
Similarly, sensor placement optimization is also challenging as several factors, such as sensor accuracy and cost and observability of the system, must be considered while deciding on the sensor positions, specifically when the sensors are used for condition-based maintenance.
Recent Developments
In a paper recently published in the journal Sensors, researchers developed a high-temperature probe using silicon carbide (SiC) Schottky diodes as a sensing element for the cement industry.
Four-hexahedral SiC (4H-SiC) devices with annealed nickel (Ni)/4H-SiC Schottky contacts were synthesized, packaged, and measured up to 400 °C, and fully parameterized to evaluate temperature-sensing properties and detect the best-performing devices in industrial environments.
Exceptional diode temperature sensitivities were observed between 1.8 mV/°C and 2.54 mV/°C for 100 nA–100 µA bias currents. Additionally, excellent sensing linearity was displayed within this current interval.
Moreover, a high response time of 117 °C/µs was achieved for the processing circuit, which was much higher than the speed of the temperature variation in the operation environment.
Low and high-temperature points in a raw meal mill were selected for temperature monitoring using the high-temperature probe and thermocouple-based alternatives. A very close agreement was observed between the conventional and proposed temperature sensing solutions between 40 °C and 400 °C, with the lifetime of the best probe being six months, which was significantly higher than conventional solutions.
Thus, the study demonstrated the feasibility of using the proposed high-temperature probe in industrial settings, specifically in the cement industry, to increase the efficiency of raw meal mills and reduce their energy consumption.
Future Trends
Recently, a team from the University of Tokyo investigated the behavior of a heat flux sensor containing special magnetic materials and electrodes during complex heat flow patterns. The magnetic material based on gallium and iron demonstrates an anomalous Nernst effect (ANE) phenomenon in which the heat energy is converted to an electrical signal.
Flexible, easy-to-produce, cheap, and robust microscopic circuits were developed by identifying the proper electrode and magnetic materials and then applying them in a repeating pattern.
Specifically, the team designed the circuits to increase the ANE while suppressing the Seebeck effect, which interferes with the ANE data-gathering potential. Most circuits displayed their effectiveness in providing heat flux data in real-time.
To summarize, thermal sensors play a critical role in ensuring optimal efficiency and performance of industrial equipment and the safety of workers while reducing energy usage and equipment failures. Proactive temperature management using these sensors can improve industrial process efficiency.
References and Further Reading
Thermal Sensors. [Online] Available at: https://www.sciencedirect.com/topics/engineering/thermal-sensor
IIoT sensors – The foundation of digital industry. [Online] Available at: https://www.yokogawa.com/eu/solutions/featured-topics/digital-infrastructure-wiki/dx-components/iiot-sensors-the-foundation-of-digital-industry/
Sensor Placement Optimization. [Online] Available at: https://www.imperial.ac.uk/structural-integrity-health-monitoring/research/life-cycle-assessment-of-complex-structures/structural-health-monitoring/sensor-placement-optimization-/
Schweber, B. (2021). The challenge of temperature measurement and sensor calibration, Part 1. Available at: https://www.sensortips.com/featured/challenge-temperature-measurement-sensor-calibration-part-1-faq/
Jansen, J. & Merwe, A.V.D. (2020). A Framework for Industrial Internet of Things. Responsible Design, Implementation and Use of Information and Communication Technology, 12066, pp. 138-150. doi.org/10.1007/978-3-030-44999-5_12
Implementing a Cloud based Temperature Monitoring System. [Online] Available at: https://www.elpro.com/en/temperature-monitoring/cloud-based-temperature-monitoring
Novel thermal sensor could help drive down the heat. [Online] Available at: https://www.eurekalert.org/news-releases/996456
Draghici, F., et al. (2018). 400 °C Sensor Based on Ni/4H-SiC Schottky Diode for Reliable Temperature Monitoring in Industrial Environments. Sensors, 19(10), p. 2384. doi.org/10.3390/s19102384
Industrial Temperature Sensor Technology. [Online] Available at: https://www.advancedtech.com/blog/temperature-monitoring/
Significance of Temperature Sensor Probes in Industrial Applications. [Online] Available at: https://www.birkmfg.com/blog/significance-of-temperature-sensor-probes-in-industrial-applications/
The Different Types of Thermal Sensors. [Online] Available at: https://resources.system-analysis.cadence.com/blog/msa2021-the-different-types-of-thermal-sensors
Benefits of temperature control in industry. [Online] Available at: https://www.fujielectric.fr/en/news/Benefits-of-temperature-control-in-industry
Why temperature control is essential to the manufacturing sector. [Online] Available at: https://www.askewsltd.com/blog/why-temperature-control-is-essential-to-the-manufacturing-sector/
Benefits of Temperature Monitoring in Industrial Settings. [Online] Available at: https://www.yg-enclosure.com/article/benefits-of-temperature-monitoring-in-industrial-settings.html
Constructing a Monitoring System Using Existing Sensors. [Online] Available at: https://www.yokogawa.com/library/resources/application-notes/constructing-a-monitoring-system-using-existing-sensors/
Fan, G., et al. (2015). Large-Scale Wireless Temperature Monitoring System for Liquefied Petroleum Gas Storage Tanks. Sensors, 15(9), pp. 23745-23762. doi.org/10.3390/s15092374
Disclaimer: The views expressed here are those of the author expressed in their private capacity and do not necessarily represent the views of AZoM.com Limited T/A AZoNetwork the owner and operator of this website. This disclaimer forms part of the Terms and conditions of use of this website.