Measuring the surface profile is a crucial step in the manufacturing industry to evaluate the quality of machined surfaces and ensure that the required quality standards are met. Using sensors for this purpose allows for highly accurate, non-contact measurements of surface profiles.
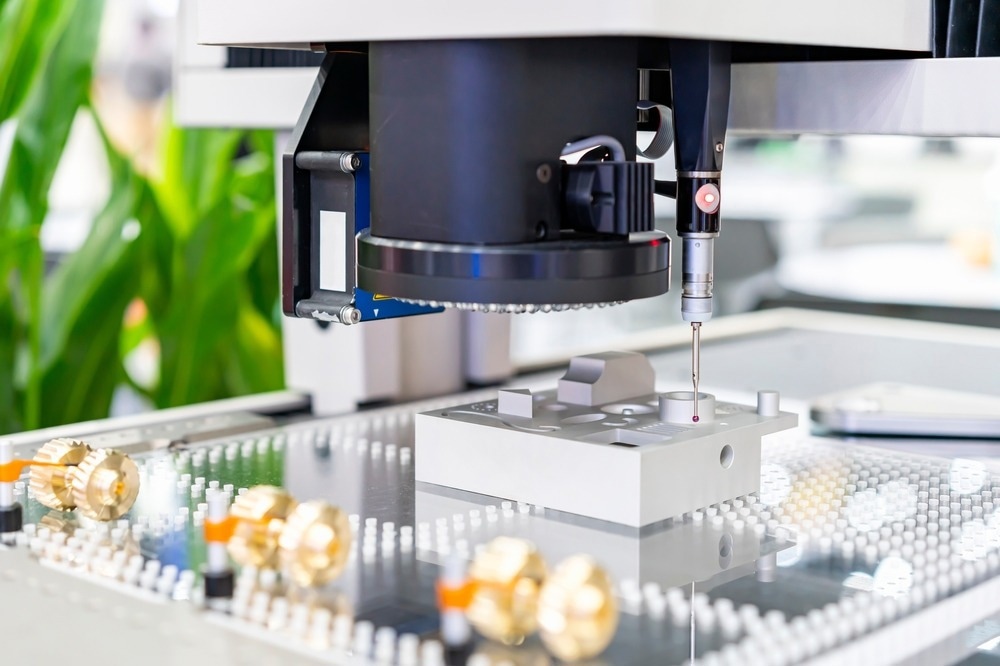
Image Credit: Surasak_Photo/Shutterstock.com
Importance of Profile Measurements
A product's surface reflects its internal and external characteristics and the surface texture is associated with the product application. Advancements in science and technology, as well as the need for mechanical high-precision surfaces, have led to the extensive utilization of micro-nanoscale sensors, micro-electromechanical systems (MEMS), nano-electromechanical systems (NEMS), and precision optical components in the machining industry.
Additionally, the importance of measuring and evaluating surface textures at the micro/nanoscale has increased significantly, making the need for high-resolution, large-dynamic-range, two- or three-dimensional (2D/3D) surface profile measurements more critical than ever before. Consequently, extensive research has been conducted on this subject.
Sensors are utilized to measure bridge profiles for detecting damage, as well as for 2D and 3D surface profile measurements and vehicle localization. These tasks are accomplished using technologies such as laser diodes, image sensors, and inertial measurement units.
Sensors to Measure Surface Roughness
Surface roughness is a key element of material characteristics that significantly impacts performance, functionality, and quality. It defines the irregularities and variations in the ideal surface shape. Accurate and reliable measurement of surface roughness is crucial in various industries, including engineering, manufacturing, and materials science.
Sensors used to measure surface roughness have a wide range of applications in different fields, such as engineering, manufacturing, and materials science. These are used to evaluate the surface roughness of electronic components, machined parts, and implants. In addition, they play a vital role in monitoring surface wear and tear, ensuring product quality, and maintaining performance standards.
Several types of sensors are available for measuring the surface roughness. Contact sensors are frequently used. Stylus-type sensors are a prevalent option because they physically make contact with the measured surface. These sensors utilize a stylus or probe to touch the surface, which is then measured to determine surface roughness.
Non-contact sensors are instruments that do not come into physical contact with the surface they are measuring. They can be classified into two main groups: electromagnetic sensors and optical sensors.
Confocal sensors possess a remarkable level of accuracy and can measure the surface roughness within a range of 0.01 to 10 µm. Nevertheless, these sensors have certain limitations, such as being affected by the characteristics of the surface being measured and the presence of contaminants.
Gauging the surface roughness using interferometric sensors employs the principles of interferometry. These sensors can achieve high levels of precision by directing a beam of light at the measured surface and then capturing the reflected light with a detector.
The interferometry-based sensor technology is particularly useful for measuring the surface roughness, with an effective range of 0.001–1 µm. Despite high accuracies, these sensors have certain limitations. For example, they can be affected by the characteristics of the measured surface, vibrations, and temperature variations.
Sensors in Metrology
Metrology involves the creation, calibration, and application of measurement tools and techniques, including sensors, to ensure accurate and consistent measurement.
The goal of metrology is to ensure that the processes and products meet established specifications and standards and that they function as intended.
The sensors used in the metrology industry are essential for the accurate and precise measurement of physical quantities such as pressure, temperature, displacement, and other parameters. In doing so, these measurements help to evaluate the performance and quality of products and processes, ensuring that they adhere to established standards and specifications.
Collecting and analyzing sensor data provides valuable insights into the behavior of components, materials, and systems, enabling the identification and diagnosis of potential issues or malfunctions. This information is crucial for making informed decisions during product development, design, and production and for improving overall product quality and efficiency.
Using sensors in automating metrology helps evaluate and analyze manufactured goods, streamlines the measurement process, and improves data precision, reliability, and consistency. Automating the measurement procedure allows manufacturers to reduce errors, increase production rates, and enhance product quality.
MEMs, a kind of digital sensors are increasingly being incorporated into the Internet of Things (IoT) systems at large scales at low cost and with ease. These sensors generate substantial amounts of data that can be utilized in machine learning (ML) and artificial intelligence (AI) systems.
In the context of Industry 4.0, sensor data plays a crucial role in IoT systems. Hence, it is essential to provide the fundamental characteristics of the sensor, including quantity, type, unit, quality, and uncertainty, in a machine-readable format.
Laser Triangulation for High-Precision Profile Measurement
The concept of triangulation has been widely acknowledged for many years and involves using three-point references to measure geometric relationships. Triangulation sensors use laser light to measure surfaces with high accuracy.
These sensors project a laser beam onto a target surface and employ a high-resolution sensor array tilted at a fixed angle to detect diffuse reflections. The distance between the sensor and the target can be determined by measuring the changes in the angle of the reflected light, resulting in measurements with sub-micrometer precision.
Laser-line triangulation involves projecting a laser line onto a surface, which produces a surface profile. The surface profile can be calculated by measuring the intensity of the reflected light using a position-sensitive two-dimensional sensor element. This technique can be extended to create a three-dimensional image of the surface by vertically moving the target or sensor.
Conclusion
Overall, measuring surface profiles in the metal industry is crucial for maintaining high-quality machined surfaces that meet industry standards. Advanced sensors, including micro-nanoscale sensors, MEMS, NEMS, and precision optical components, have revolutionized the precision and efficiency of these measurements.
The focus on micro/nanoscale surface texture measurements has intensified, necessitating high-resolution, large-dynamic-range, and two- or three-dimensional profile assessments. Surface roughness, a key determinant of material characteristics, has been extensively addressed, emphasizing the critical role of sensors in engineering, manufacturing, and materials science.
Integrating sensors into metrology practices has emerged as a cornerstone of accurate and consistent measurements across various physical parameters. By contributing to the evaluation of product performance and quality, sensors aid in adhering to established standards.
References and Further Reading
Gao, W., et al. (2019). On-machine and in-process surface metrology for precision manufacturing. CIRP Annals, 68(2), pp. 843-866. doi.org/10.1016/j.cirp.2019.05.005.
Sensors in Surface Roughness Measurement: A Guide.
The Critical Role of Sensors in the Metrology Industry.
Disclaimer: The views expressed here are those of the author expressed in their private capacity and do not necessarily represent the views of AZoM.com Limited T/A AZoNetwork the owner and operator of this website. This disclaimer forms part of the Terms and conditions of use of this website.