By Ankit SinghReviewed by Susha Cheriyedath, M.Sc.Sep 30 2024
Imagine your senses as tools that help you perceive the world around you—your eyes detect light, and your skin senses temperature changes. Physical sensors work similarly but for machines.
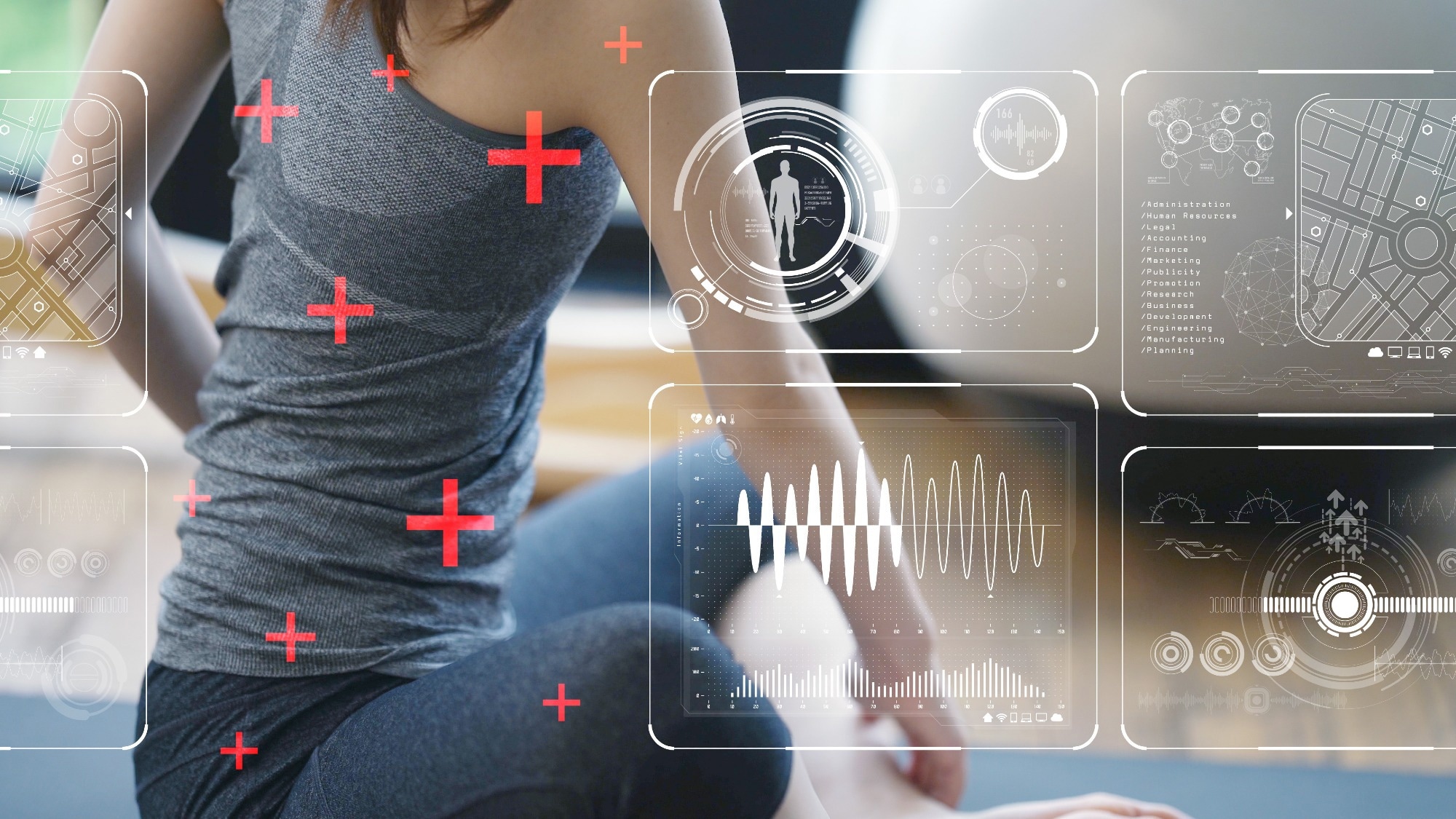
Image Credit: metamorworks/Shutterstock.com
Physical sensors are devices that convert changes in the physical environment, like temperature, pressure, or motion, into electrical signals that can be measured. These sensors help various systems in industries like healthcare, environmental monitoring, and industrial automation to monitor and respond to the world around them. In essence, physical sensors are the “senses” of modern technology, enabling machines to understand and interact with their surroundings.
Fundamentals of Physical Sensors
Physical sensors are fundamentally grounded in the principles of physics. This section investigates the technical facets and fundamental principles underpinning the operation of physical sensors, the diverse categories of physical sensors, the mechanisms they employ to detect changes, and the critical characteristics that shape their performance.1
Definition and Operation of Physical Sensors
Physical sensors are devices designed to detect and measure changes in physical quantities, converting these variations into electrical signals. The sensing process involves three key components:
-
Sensing Element: The core of any physical sensor, this component responds to environmental changes such as temperature, pressure, or motion. For example, in a thermocouple, two dissimilar metals generate voltage in response to temperature differences.
-
Transducer: This crucial part converts the physical changes detected by the sensing element into electrical signals. For instance, piezoelectric sensors convert mechanical stress into electrical charge.
-
Signal Conditioning: Once the electrical signal is generated, it often requires conditioning—such as amplification, noise filtering, or analog-to-digital conversion (ADC)—to make it suitable for further processing.
These components work together to ensure accurate and reliable data acquisition in various applications, from industrial automation to healthcare technologies.1,2
Types of Physical Sensors
Physical sensors are categorized by the type of physical quantity they measure, each serving distinct roles across various industries:
-
Temperature Sensors: Devices like thermocouples, thermistors, and resistance temperature detectors (RTDs) measure thermal changes by converting heat into electrical signals. These sensors are essential for monitoring system or environmental temperatures in industrial, medical, and HVAC applications.
-
Pressure Sensors: Strain gauges, piezoelectric sensors, and capacitive pressure sensors are used to measure pressure variations in gases or liquids. They are widely deployed in industrial automation, automotive systems, and medical devices for precise fluid pressure monitoring.
-
Proximity Sensors: Inductive, capacitive, and optical proximity sensors detect the presence or absence of objects without physical contact. These sensors are critical for automation, safety, and process efficiency in manufacturing environments.
-
Motion Sensors: Accelerometers and gyroscopes detect movement, orientation, or acceleration changes. They are integral to the performance of mobile devices, automotive systems, and aerospace applications.
-
Humidity Sensors: These sensors measure air moisture content, playing a vital role in agriculture, weather forecasting, and HVAC systems to ensure optimal environmental conditions.
-
Magnetic Field Sensors: Hall effect sensors and magnetometers detect changes in magnetic fields. They are key components in navigation systems, motor control, and electronic compasses across numerous industries.1
Sensing Mechanisms
Different types of physical sensors rely on various physical principles to detect environmental changes:
-
Piezoelectric Effect: Certain materials generate an electrical charge when subjected to mechanical stress. This principle is used in sensors that measure pressure, vibration, or mechanical strain, such as piezoelectric accelerometers, which are widely applied in industrial and automotive systems.
-
Thermoelectric Effect: Temperature sensors like thermocouples utilize the thermoelectric effect, where two dissimilar metals produce a voltage when exposed to a temperature gradient. This voltage allows for precise measurement of temperature differences, making thermocouples essential for a range of industrial and scientific applications.
-
Optical Sensing: Optical sensors leverage light to detect environmental changes. Devices such as photodiodes convert variations in light intensity into electrical signals. These sensors are commonly used in fiber optic communications, imaging technologies, and proximity detection in manufacturing processes.
-
Electromagnetic Induction: Inductive sensors operate on the principle of electromagnetic induction, where a changing magnetic field induces an electric current in a conductor. Inductive proximity sensors, often employed in industrial automation, detect metallic objects without requiring physical contact, enhancing operational efficiency and safety.1,2
Characteristics of Physical Sensors
The performance of physical sensors is evaluated based on several critical characteristics, each impacting the sensor’s accuracy and reliability in various applications:
-
Sensitivity: Sensitivity measures the sensor’s ability to detect small variations in the measured physical parameter. Highly sensitive sensors are essential in precision-demanding fields such as medical devices and scientific instruments, where even minute changes must be accurately captured.
-
Accuracy: Accuracy reflects how closely the sensor's output aligns with the true value of the physical quantity being measured. High accuracy is vital in sectors like healthcare, where even small discrepancies could lead to incorrect diagnoses or ineffective treatments.
-
Linearity: Linearity refers to the extent to which a sensor’s output is directly proportional to the input parameter throughout its measurement range. High linearity ensures reliable and predictable performance, making these sensors ideal for use in calibration and control systems.
-
Response Time: Response time defines how quickly a sensor can detect changes and deliver an output signal. Fast response times are critical in real-time applications such as automotive safety systems, where immediate detection of obstacles or changing conditions can help prevent accidents.3,4
Signal Conditioning and Data Processing
After a physical sensor detects and converts a parameter into an electrical signal, further processing is typically required to ensure the signal is suitable for analysis:
-
Amplification: Signals generated by physical sensors are often weak and need amplification to be effectively processed. Without amplification, the output may be too minimal to be accurately measured, affecting the performance of the overall system.
-
Filtering: Sensor signals can be prone to noise or interference from the surrounding environment. Filters are applied to remove this unwanted noise, ensuring that the data received is clean, reliable, and suitable for precise analysis.
-
Analog-to-Digital Conversion (ADC): Many sensors produce analog signals, but most modern systems operate with digital data. An ADC converts the sensor's analog output into a digital format, allowing it to be processed by microcontrollers, computers, or other digital systems.3,4
Applications of Physical Sensors
Physical sensors are foundational to a wide range of industries, enabling precise monitoring and control of processes that are essential for operational efficiency and safety. In industrial automation, sensors regulate temperature, pressure, and fluid levels. For instance, temperature sensors manage heat in high-temperature furnaces, while pressure sensors are critical in hydraulic systems to maintain performance and prevent malfunctions. In more advanced systems, proximity sensors guide the movements of industrial robots with precision, enhancing productivity and reducing the margin for error in automated processes.
Optical Sensors in Food Hygiene Systems
In the automotive sector, sensors play a crucial role in ensuring both vehicle performance and passenger safety. Tire pressure sensors monitor inflation levels to prevent blowouts, while engine sensors track a range of parameters, including fuel efficiency and emissions. In addition, accelerometers and gyroscopes are essential components of airbag systems, detecting rapid deceleration and deploying airbags in a fraction of a second. As the automotive industry shifts towards autonomous vehicles, the reliance on physical sensors continues to grow, with these devices providing real-time data on road conditions, vehicle surroundings, and potential obstacles.
In healthcare, the role of physical sensors is becoming increasingly indispensable. These sensors are integrated into a variety of medical devices and wearable technologies that monitor vital signs such as heart rate, body temperature, and blood oxygen levels. In hospital settings, sensors enable continuous patient monitoring, providing real-time data that is critical for diagnosing and managing acute conditions. Wearable devices, such as fitness trackers and smartwatches, also employ sensors to track biometric data, offering users insights into their health and encouraging preventative care.
Environmental monitoring has similarly benefited from advancements in sensor technology. Physical sensors are deployed to track humidity, soil moisture, and atmospheric conditions, aiding in agriculture, climate research, and disaster prevention. For example, moisture sensors help optimize irrigation in smart agriculture systems, reducing water consumption and improving crop yields. In climate research, sensors provide data that informs models predicting weather patterns and climate change.
Finally, consumer electronics have increasingly integrated physical sensors to enhance user experience and interactivity. Motion sensors and accelerometers are found in devices like smartphones and gaming consoles, enabling intuitive control through gestures and movements. In smart home systems, sensors detect motion, temperature, and light levels to optimize energy usage and enhance security, bringing convenience and efficiency to everyday life.1
Recent Developments in Physical Sensors
The field of physical sensors is continually evolving, with significant breakthroughs enhancing their performance, miniaturization, and integration into advanced systems.
A recent study published in the Chemical Engineering Journal introduced a flexible pressure-temperature dual-parameter sensor designed to mimic human skin for use in wearable devices and intelligent robots. The sensor integrates graphene-coated thermoplastic polyurethane/carbon nanofibers (TPU/CNFs), providing high-pressure sensitivity (0.14/kPa) and temperature sensitivity (30.8 μV/K).
This design minimizes interference between pressure and temperature signals, improving accuracy. Applications include real-time human respiration monitoring in masks and robotic systems for high-temperature alarms and automatic evacuation, with promising potential in healthcare and human-machine interaction (HMI) systems.5
Another notable study published in ACS Nano demonstrated the self-powered integrated nanostructured gas-sensor (SINGOR) system designed for real-time chemical safety and health monitoring. Powered by indoor light via a Si solar cell, SINGOR operates at room temperature and offers ultrahigh sensitivity to gases like hydrogen, formaldehyde, and acetone, with detection limits as low as 1-10 ppb.
This wirelessly connected sensor network supports gas pattern recognition and leakage detection. Its potential applications span smart homes, buildings, and future smart cities, offering precise gas monitoring and safety alerts.6
Sensor Technology: From Basics to Breakthroughs
Key Players in the Field
The physical sensor market is fueled by a handful of leading companies that drive innovation and technological advancements across various industries. Honeywell and Bosch stand at the forefront, specializing in the production of pressure and motion sensors that are critical for automotive and industrial automation. Both companies have established a strong presence by delivering robust, high-precision solutions that enhance safety, performance, and operational efficiency in their respective sectors.
Texas Instruments, a global leader in semiconductor technology, has made significant strides in sensor solutions, particularly in consumer electronics. Its sensors are widely used in devices ranging from smartphones to wearables, where compact size and energy efficiency are paramount.
STMicroelectronics has also become a key player in the development of sensors for the Internet of Things (IoT) and wearable technology. Its innovations focus on miniaturization and integration, making its sensors ideal for next-generation connected devices that require low power consumption and high performance.
Sensirion, a specialist in environmental and flow sensors, serves critical industries like healthcare and environmental monitoring. Their products enable precise measurement of air quality, humidity, and fluid flow, which are essential for applications ranging from medical devices to climate control systems.
These companies continue to push the boundaries of physical sensor technology, focusing on advancements in miniaturization, energy efficiency, and performance to meet the evolving demands of industries such as automotive, healthcare, consumer electronics, and environmental monitoring.
Conclusion
Physical sensors have transformed modern technology by enabling the seamless monitoring and control of physical parameters across diverse industries. From temperature and pressure sensing to motion and proximity detection, these devices form the foundation of today's smart systems. As innovations in nanotechnology, artificial intelligence (AI), and quantum sensing continue to emerge, the future of physical sensors looks bright, with the potential for even greater precision, integration, and sustainability in the years ahead.
Advancements in Sensor Technology: What to Expect by 2030
References and Further Reading
- Javaid, M. et al. (2020). Sensors for daily life: A review. Sensors International, 2, 100121. DOI:10.1016/j.sintl.2021.100121. https://www.sciencedirect.com/science/article/pii/S2666351121000425
- Li, S. et al. (2019). Physical sensors for skin-inspired electronics. InfoMat, 2(1), 184-211. DOI:10.1002/inf2.12060. https://onlinelibrary.wiley.com/doi/full/10.1002/inf2.12060
- Kalaivaani, P. et al. (2020). Design and implementation of low power bio signal sensors for wireless body sensing network applications. Microprocessors and Microsystems, 79, 103271. DOI:10.1016/j.micpro.2020.103271. https://www.sciencedirect.com/science/article/abs/pii/S0141933120304300
- Zhou, F., & Chai, Y. (2020). Near-sensor and in-sensor computing. Nature Electronics, 3(11), 664-671. DOI:10.1038/s41928-020-00501-9. https://www.nature.com/articles/s41928-020-00501-9
- Yin, Y. et al. (2022). A flexible dual parameter sensor with hierarchical porous structure for fully decoupled pressure–temperature sensing. Chemical Engineering Journal, 430, 133158. DOI:10.1016/j.cej.2021.133158. https://www.sciencedirect.com/science/article/abs/pii/S1385894721047343
- Song, Z. et al. (2021). Wireless Self-Powered High-Performance Integrated Nanostructured-Gas-Sensor Network for Future Smart Homes. ACS Nano, 15(4), 7659–7667. DOI:10.1021/acsnano.1c01256. https://pubs.acs.org/doi/full/10.1021/acsnano.1c01256
Disclaimer: The views expressed here are those of the author expressed in their private capacity and do not necessarily represent the views of AZoM.com Limited T/A AZoNetwork the owner and operator of this website. This disclaimer forms part of the Terms and conditions of use of this website.