By Ankit SinghReviewed by Susha Cheriyedath, M.Sc.Nov 1 2024
Industrial automation has reshaped manufacturing by introducing a level of precision and control that was previously unattainable. Industrial sensors are central to this shift, providing the real-time data needed to monitor, control, and adjust processes, ensuring streamlined operations. The integration of advanced sensors with automated systems creates highly responsive control environments, enhancing productivity, safety, and accuracy across diverse industrial applications.
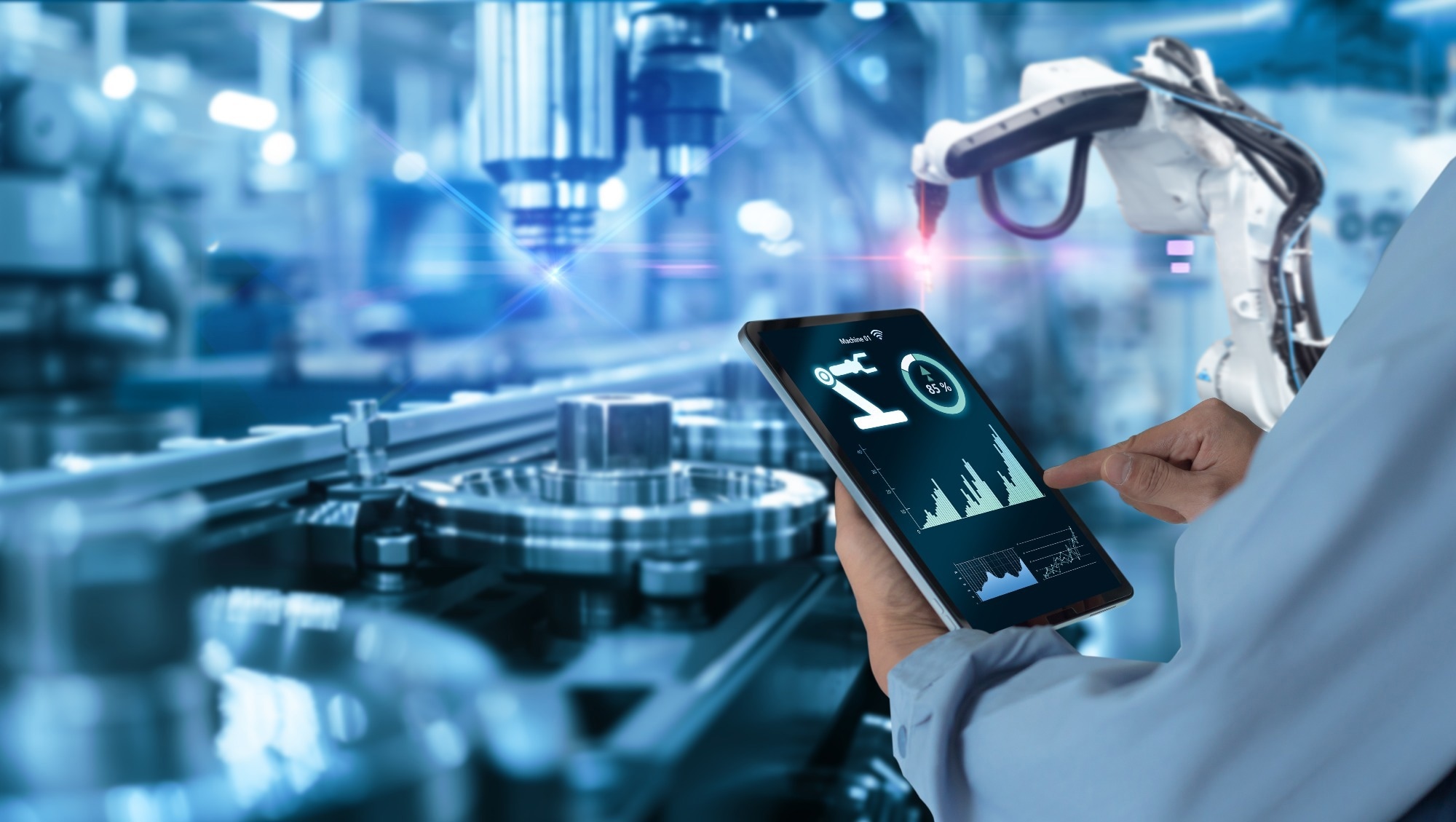
Image Credit: panuwat phimpha/Shutterstock.com
Sensors That Drive Industry: An Introduction
Industrial sensors are the backbone of precision and control across key sectors, each sensor type designed to monitor critical parameters that ensure consistent, high-quality operations.1
- Temperature Sensors: Essential in fields like energy and manufacturing, these sensors stabilize operational environments by maintaining equipment within specified temperature ranges, which safeguards both process efficiency and product integrity.
- Pressure Sensors: In the oil, gas, and chemical industries, maintaining precise pressure is crucial. Pressure sensors prevent overloads by continually monitoring and adjusting system levels, enhancing both safety and process reliability.
- Proximity Sensors: Frequently used in robotics and automated assembly, proximity sensors detect objects without direct contact, enabling smooth, uninterrupted workflows and minimizing mechanical wear.
- Level Sensors: In pharmaceuticals and food processing, maintaining material levels is critical. Level sensors ensure continuous supply by monitoring ingredient quantities, which prevents costly production delays and maintains product quality.
- Flow Sensors: For industries dependent on fluid dynamics, such as water treatment, flow sensors offer real-time monitoring of fluid movement. By optimizing flow rates, these sensors reduce waste, increase operational efficiency, and contribute to sustainable resource use.1
What Are Automotive Sensors and How Do They Work?
Programmable Logic Controllers (PLCs): The Brains Behind Automation
Programmable Logic Controllers (PLCs) are the nerve center of modern industrial systems, orchestrating complex processes through real-time sensor data and automated control. Engineered for reliability, PLCs are programmed to execute specific, high-stakes tasks, using data directly from sensors to make instantaneous adjustments that optimize production flow and ensure seamless operation.
Most PLCs are programmed with ladder logic, a language familiar to engineers in manufacturing, allowing for precise control over tasks within an industrial setup. In assembly lines, for example, PLCs adjust motor speeds based on proximity sensor inputs, aligning components with precision to avoid misalignment and maintain production momentum. Designed with modular architectures, PLCs adapt to evolving production demands, supporting a diverse array of sensor types to ensure flexible, responsive control.2
Many of today’s advanced PLCs offer seamless integration with industrial IoT networks, simplifying the management of extensive sensor ecosystems and enabling real-time monitoring from centralized locations.
Built to endure, these controllers withstand extreme conditions, maintaining stability in environments where fluctuations in temperature or humidity could compromise weaker systems. Through human-machine interfaces (HMIs), operators can also gain a window into the data gathered by PLCs, with insights into system health and performance that could enhance decision-making and enable proactive maintenance.2
Applications of Industrial Sensors in Automation
Industrial sensors are fundamental to modern automation, supplying real-time data that enhances monitoring, control, and optimization across various sectors, from manufacturing to energy and logistics. This data-centric approach drives applications that boost productivity, improve quality control, and ensure safety, providing a backbone for efficient, resilient operations.
Predictive Maintenance
Predictive maintenance relies heavily on sensors to monitor equipment health and forecast maintenance needs. Vibration and temperature sensors are particularly effective in detecting early signs of wear, such as unusual vibrations in motor components, which may signal misalignment or other developing issues. By alerting operators to potential failures, sensors enable targeted, condition-based maintenance that extends equipment life, lowers costs, and minimizes unplanned downtime.3
Quality Control
In manufacturing, high product quality is essential, and industrial sensors ensure consistency by closely monitoring process parameters. Temperature and pressure sensors, for instance, provide live feedback on processing conditions, helping maintain strict quality thresholds. Automated systems can halt production at the first sign of deviation, minimizing waste and rework. In food processing, level sensors confirm precise ingredient measurements, while flow sensors ensure that each step in a production recipe is accurately followed.1
Energy Management
Energy efficiency is a priority across industries, and industrial sensors are central to identifying and addressing excessive energy use. By monitoring electricity, fuel, and water consumption, sensors reveal inefficiencies that smart factories can automatically correct, such as adjusting motor speeds or shutting down idle machinery. For example, sensors detect underutilized conveyor belts and signal PLCs to reduce speeds, cutting power consumption without disrupting productivity.4
Safety Monitoring
Industrial sensors are indispensable for safety, particularly in high-risk environments. Gas sensors monitor the air for harmful chemicals, while temperature sensors prevent overheating by flagging equipment operating outside safe ranges. In sectors like chemical manufacturing and oil refining, sensor networks trigger alarms or activate shutdowns in response to hazardous conditions, isolating affected areas to protect workers.1
Inventory and Resource Management
In automated warehouses and production facilities, level and proximity sensors help maintain efficient material flow. Proximity sensors track item positions in storage, guiding robots and AGVs (automated guided vehicles) for precise navigation and retrieval. Level sensors monitor supply levels in production lines, sending alerts to restock or reorder as necessary, ensuring that workflows remain uninterrupted and minimizing waste from overstock or shortage.1,4
Emerging Sensor Technologies in Industrial Automation
Continuous advancements in sensor technology and computational power are driving a new era in industrial automation, making systems more adaptable, efficient, and scalable. These developments allow industries to gain deeper insights and achieve higher precision in complex environments. Below are the key emerging technologies transforming the future of industrial sensors.
Wireless Sensors and IoT Integration
Wireless sensors connected via the Internet of Things (IoT) enable seamless data transmission across industrial environments, eliminating the need for wiring and allowing flexible sensor deployment. This connectivity allows centralized monitoring of complex systems from remote locations, which is valuable in industries that operate over large areas, like mining or agriculture. Wireless IoT sensors also support predictive analytics, facilitating real-time adjustments and preventive actions before disruptions occur.5
Edge Computing and Real-Time Data Processing
Edge computing localizes data processing, reducing latency and minimizing reliance on distant data centers. This capability is essential for real-time applications, such as autonomous robotics and high-speed assembly lines, where even a minor delay can disrupt workflow. In manufacturing, for example, edge computing can instantly identify and correct quality defects, adjusting operations on the spot to maintain consistent output. This localized processing is especially beneficial in environments where network instability might otherwise impede decision-making speed, ensuring that critical adjustments happen without interruption.5
AI and ML Integration
By integrating artificial intelligence (AI) with sensor networks, industrial systems can leverage machine learning (ML) algorithms to interpret vast amounts of data, identify patterns, and make predictive adjustments autonomously. AI-driven sensor data analytics are useful in optimizing equipment performance, predicting failures, and adjusting processes based on dynamic conditions. AI capabilities extend to visual inspection sensors, which enhance quality control by detecting minute defects in products, further improving overall product quality.6
Multi-Sensor Fusion
Multi-sensor fusion combines data from different types of sensors to create a unified view of industrial processes. For instance, in a smart factory, combining data from temperature, pressure, and vibration sensors provides a comprehensive perspective on machinery health. By combining insights across multiple dimensions, multi-sensor fusion improves the accuracy of predictions, reducing the risk of unplanned equipment failures and extending asset life through more precise maintenance scheduling.7
Sensor Challenges in Automation: What Lies Ahead?
Despite their benefits, integrating sensors into automation systems presents several challenges. Issues such as data security, sensor accuracy, and compatibility with legacy systems can hinder seamless implementation, highlighting the need for effective strategies to address these obstacles and ensure reliable, optimized automation.
- Data Security: With the rise of IoT-enabled sensors, data security has become a significant concern. Ensuring secure data transfer and storage is crucial, especially in sectors dealing with sensitive data like pharmaceuticals and aerospace.1
- Calibration and Accuracy: Sensor calibration is critical for maintaining accuracy. Regular maintenance and recalibration are required to ensure reliable performance, particularly in environments with fluctuating conditions.1
- Integration with Legacy Systems: Many industrial setups still use legacy systems that may not support new sensor technologies, posing integration challenges. Upgrading or retrofitting these systems requires careful planning and investment.1
The Path Forward: Automation’s Role in a Sustainable Future
As sustainability becomes a priority across industries, automation and sensor technologies are emerging as critical tools for achieving environmental and operational efficiency targets. Modern automation systems are engineered to actively monitor and reduce emissions, optimize energy usage, and minimize resource consumption, aligning closely with green manufacturing objectives. In automotive manufacturing, for instance, advanced sensors continuously monitor emissions and chemical processes, ensuring strict adherence to environmental regulations and supporting a reduced carbon footprint.8
Incorporating sustainability metrics into industrial automation will allow companies to comply with regulatory standards and realize significant cost efficiencies. With advances in sensor technology, the ability to track and manage resource use has become both more precise and more affordable, allowing businesses to implement data-driven sustainability measures across production lines. As the cost and accessibility of these technologies improve, automation will be able to become even more widespread, encouraging responsible production practices and making sustainability goals achievable across diverse sectors.8
Advancements in Sensor Technology: What to Expect by 2030
Conclusion
Industrial sensors and automation are at the heart of today’s manufacturing, pushing the boundaries of what’s possible in precision, safety, and efficiency. With advancements like AI, edge computing, and IoT, sensor-based automation gives operators greater control over complex processes, helping to boost productivity and maintain high safety and quality standards. As the push for sustainable and cost-effective operations grows, adopting these technologies is becoming essential for manufacturers aiming to achieve smarter, more environmentally responsible production.
References and Further Reading
- Javaid, M. et al. (2020). Significance of sensors for industry 4.0: Roles, capabilities, and applications. Sensors International, 2, 100110. DOI:10.1016/j.sintl.2021.100110. https://www.sciencedirect.com/science/article/pii/S2666351121000310
- Sehr, M. A. et al. (2020). Programmable Logic Controllers in the Context of Industry 4.0. IEEE Transactions on Industrial Informatics. DOI:10.1109/tii.2020.3007764. https://ieeexplore.ieee.org/abstract/document/9134804
- Pech, M. et al. (2020). Predictive Maintenance and Intelligent Sensors in Smart Factory: Review. Sensors, 21(4), 1470. DOI:10.3390/s21041470. https://www.mdpi.com/1424-8220/21/4/1470
- Alarcón, M. et al. (2021). Energy and maintenance management systems in the context of industry 4.0. Implementation in a real case. Renewable and Sustainable Energy Reviews, 142, 110841. DOI:10.1016/j.rser.2021.110841. https://www.sciencedirect.com/science/article/abs/pii/S1364032121001350
- Qiu, T. et al. (2020). Edge Computing in Industrial Internet of Things: Architecture, Advances and Challenges. IEEE Communications Surveys & Tutorials, 22(4), 2462–2488. DOI:10.1109/comst.2020.3009103. https://ieeexplore.ieee.org/abstract/document/9139976
- Kalsoom, T. et al. (2019). Advances in Sensor Technologies in the Era of Smart Factory and Industry 4.0. Sensors, 20(23), 6783. DOI:10.3390/s20236783. https://www.mdpi.com/1424-8220/20/23/6783
- Sharma, D. et al. (2024). Towards intelligent industrial systems: A comprehensive survey of sensor fusion techniques in IIoT. Measurement: Sensors, 32, 100944. DOI:10.1016/j.measen.2023.100944. https://www.sciencedirect.com/science/article/pii/S2665917423002805
- Jamwal, A. et al. (2020). Industry 4.0 Technologies for Manufacturing Sustainability: A Systematic Review and Future Research Directions. Applied Sciences, 11(12), 5725. DOI:10.3390/app11125725. https://www.mdpi.com/2076-3417/11/12/5725
Disclaimer: The views expressed here are those of the author expressed in their private capacity and do not necessarily represent the views of AZoM.com Limited T/A AZoNetwork the owner and operator of this website. This disclaimer forms part of the Terms and conditions of use of this website.