Self-calibrating sensors are advanced devices that automatically adjust their output to maintain accuracy, even in changing environmental conditions. By eliminating the need for manual calibration, these sensors improve efficiency and reliability in real-time applications. Their capabilities make them invaluable across industries like industrial automation, healthcare, and environmental monitoring.
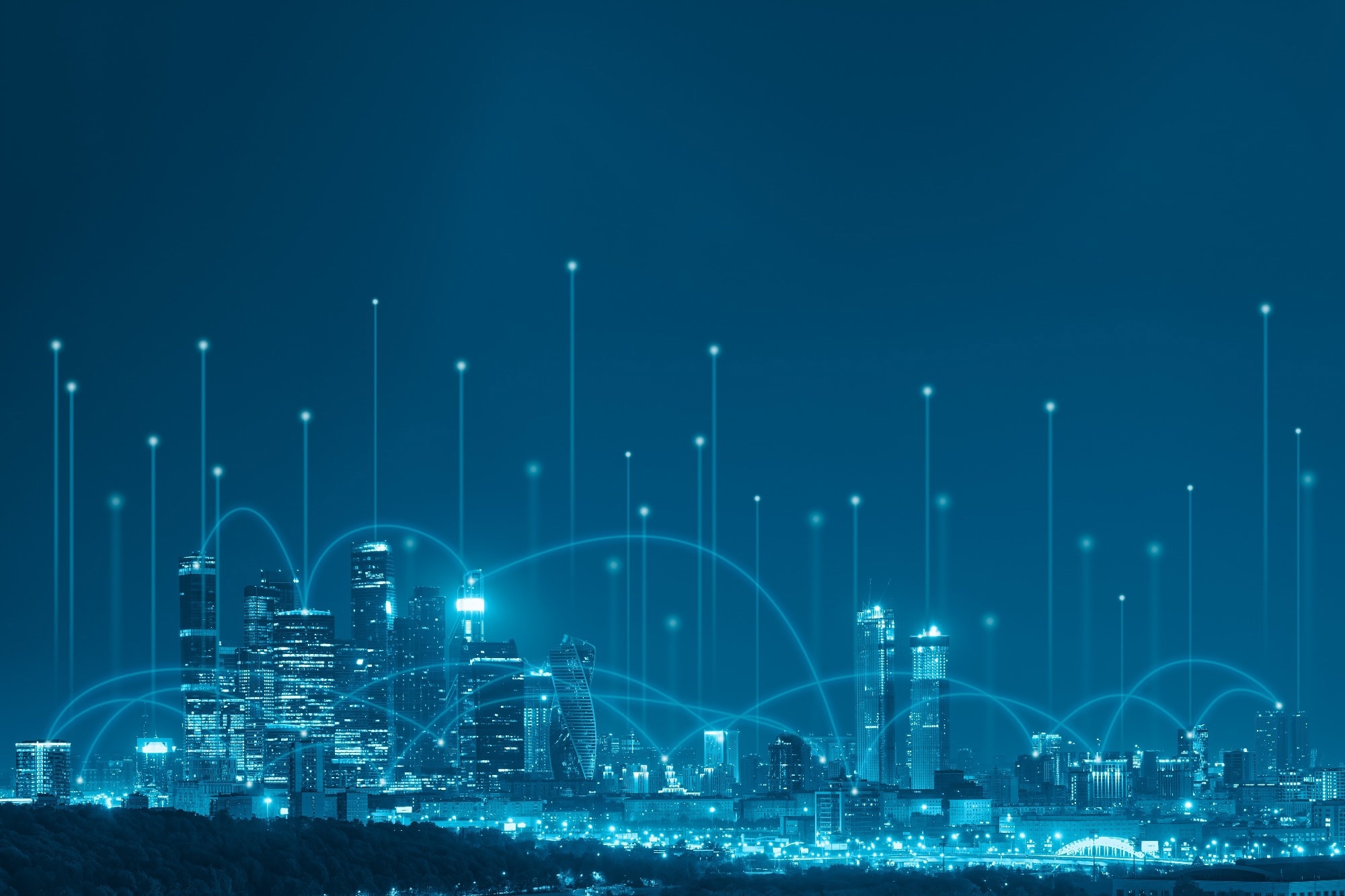
Image Credit: Viktollio/Shutterstock.com
This guide explores the key principles of self-calibrating sensors, their methodologies, and how they are shaping sensor applications. Along the way, we’ll address:
- The role of self-calibration in addressing sensor drift and environmental noise
- Common models and techniques used for self-calibration
- Innovations and future directions for these technologies
Why Self-Calibrating Sensors Are Necessary
Self-calibrating sensors are changing the way we approach data collection by offering a smarter and more flexible alternative to traditional sensors. Unlike older models, which rely on factory-set calibrations, these advanced systems can adjust and optimize themselves as needed. They’re designed to address some of the biggest challenges with traditional sensors, like accuracy issues caused by environmental changes or aging components.
A major limitation of conventional sensors is their tendency to drift over time, leading to less accurate readings. Fixing that drift typically requires manual recalibration, which is time-consuming and especially difficult when sensors are deployed in remote or hard-to-reach areas. Self-calibrating sensors tackle this problem by continuously monitoring their own performance and making adjustments automatically—no human intervention is needed.
The benefits are significant, particularly in fields like healthcare and environmental monitoring. In medical diagnostics, for example, even a small error in sensor readings could mean missing an early warning sign of a disease. In environmental science, precise, real-time measurements of pollution levels or climate conditions are critical for understanding and responding to global challenges.
What makes these sensors stand out is the technology behind them. They use embedded machine learning to detect patterns in their own performance and make real-time corrections. Essentially, they learn from their experiences and get better at what they do over time. This is similar to how biological systems adapt to changes to maintain balance, which adds a layer of sophistication to their design.
Another game-changer is how these sensors bring high-quality data collection to places that traditionally couldn’t access it. Whether it’s a remote research station, a developing region, or a resource-limited area, self-calibrating sensors make it possible to deploy advanced systems without needing a team of experts to keep them running smoothly.
This shift to dynamic, adaptive sensors marks a new way of thinking about data collection. Rather than being simple recording devices, sensors are now becoming intelligent systems that can learn, adapt, and improve. It’s an exciting development that’s likely to have a lasting impact on everything from science and engineering to everyday applications.2
The Complexity of Sensor Response and Calibration Models
Sensors are intricate devices that rely on response functions to convert measured parameters into output values. These response functions can range from straightforward linear models—where output values scale directly with input measurements—to more complex nonlinear relationships, such as logarithmic or exponential models, where changes in output vary depending on the input.
While linear responses dominate many applications due to their simplicity, nonlinear models provide the flexibility to capture more sophisticated relationships in certain sensing environments.
Choosing the right self-calibration model involves balancing critical factors, such as the type of measurement being performed, the sensor's inherent properties, and the computational resources available at each sensor node.
For instance, low-cost wireless sensors often operate under significant computational constraints, limiting the ability to deploy advanced calibration techniques. In such cases, simpler approaches like gradient descent or linear regression are preferred because they offer a balance of efficiency and effectiveness. On the other hand, more powerful sensor nodes can handle advanced methods such as support vector regression or artificial neural networks, which require greater computational capacity but deliver superior precision and adaptability.
The type of sensor being calibrated also heavily influences the chosen method. Temperature sensors often exhibit linear response patterns, making them well-suited for straightforward calibration techniques like Bayesian inference for modeling drift or linear regression for accuracy adjustments. In contrast, light point sensors typically involve nonlinearities, requiring more sophisticated methods like spline-based modeling or support vector regression. Meanwhile, sensors used for measuring relative humidity, vibration, or acceleration may benefit from tailored approaches, such as distributed consensus algorithms, hidden Markov models, or other specialized techniques.
At its core, the goal of self-calibration is to ensure that sensors maintain accurate and reliable performance over time, even in changing or unpredictable environments.
This can be achieved through techniques like cross-sensitivity compensation—where additional sensors measure and correct for interfering variables—or differential sensing, which uses paired sensors to cancel out systematic errors. These methods enable sensors to remain robust in the face of environmental fluctuations, aging components, or operational wear and tear.
One of the most cutting-edge advancements in this space is the integration of sensors with actuators, often referred to as "sensactors." These systems generate internal calibration signals, allowing real-time error correction and significant performance optimization. By actively comparing expected responses to actual measurements, sensactors can fine-tune their outputs, achieving levels of precision that would otherwise be unattainable with conventional approaches.
Evaluating the effectiveness of self-calibration models requires a variety of performance metrics. Researchers often rely on statistical tools such as mean error, root mean squared error (RMSE), Kullback-Leibler (K-L) divergence, and recognition accuracy to analyze calibration outcomes. These metrics provide detailed insights into how well a model performs under different conditions, offering a comprehensive understanding of its reliability, precision, and adaptability.2,3
Applications of Self-Calibrating Sensors
Self-calibrating sensors have become essential in many industries, offering higher levels of accuracy, reliability, and efficiency. By automating the calibration process, these sensors address common challenges such as drift and manual errors, making them indispensable for both critical applications and everyday operations.
Self-calibrating sensors have become essential across a wide range of industries, addressing critical challenges like sensor drift, manual errors, and the need for frequent recalibration. By automating these processes, they improve accuracy, reliability, and operational efficiency in both high-stakes and everyday applications.
- Healthcare and Hygienic Applications: In industries where hygiene and precision are paramount, self-calibrating sensors are game-changers. For example, Endress+Hauser’s TrustSens probe has been widely adopted in the food and beverage industry as well as life sciences. By automatically verifying its accuracy during sterilization cycles, it ensures compliance with regulatory standards while reducing downtime. This ability to maintain precision in sensitive environments makes it invaluable for applications like sterilization, aseptic manufacturing, and medical diagnostics.
- Manufacturing: High-temperature processes demand absolute control, and self-calibrating sensors are stepping up to the challenge. An EMPIR project introduced integrated self-validation methods for high-temperature thermometry, ensuring precise measurements critical for maintaining product quality in industrial settings.
- Wearable Technology: Fitness trackers and health monitors integrate self-calibrating sensors to maintain consistent performance, regardless of dynamic user activity. This reliability ensures accurate health metrics and enhances user trust in wearable devices.
- Industrial Process Control: In systems where downtime can result in costly losses, self-calibrating sensors are invaluable. They seamlessly integrate into process control environments, providing continuous, automated calibration and reducing the risk of production halts.
So, what makes self-calibrating sensors so compelling? Across the board, they bring benefits that solve real-world problems:
- Minimized Downtime: Inline self-calibration eliminates the need for manual recalibration, keeping operations running smoothly.
- Improved Safety and Compliance: Automatic calibration ensures consistent accuracy, meeting stringent safety and regulatory standards.
- Cost Savings: Reduced manual intervention and long-term reliability lower overall costs while boosting operational efficiency.
- Enhanced Data Quality: Self-calibrating sensors maintain stable, accurate measurements over time, building trust in data for critical applications.
- Streamlined Documentation: Automated digital calibration certificates simplify audits and regulatory compliance.
Self-calibrating sensors may not grab headlines, but their behind-the-scenes contributions are transforming the way industries monitor, measure, and manage critical processes. Whether it’s in a lab, a factory, or even on your wrist, these sensors are quietly making precision more accessible than ever.
New Developments
Self-calibrating sensors are advancing at an impressive pace, with exciting innovations reshaping industries and addressing long-standing challenges.
Take the construction industry, for instance. Giatec Scientific’s SmartRock Pro isn’t just a sensor—it’s rethinking how we monitor concrete strength. By using Concrete Electro-Mechanical Microstructure Analysis (CEMMA) technology, this sensor measures in-situ without requiring manual calibration. This innovation allows construction professionals to track curing processes and structural integrity in real-time, eliminating disruptions while boosting operational efficiency and accuracy.
In photonics, the future is becoming smaller and smarter. A groundbreaking EMPIR project has introduced the 'NMI-on-a-chip,' a silicon photodiode sensor that integrates self-calibration with ultra-precise measurements. Designed to support Europe’s photonics industry, this tiny yet powerful device reduces dependence on human intervention, hinting at a future where optical sensors maintain their own accuracy autonomously.
Gas sensing technology has also seen remarkable progress, thanks to eLichens' ultra-low-power sensors. These devices can run for over five years on a single battery without drifting from their calibration. By addressing the problem of constant recalibration, these sensors are redefining reliability standards in applications like air quality monitoring, industrial safety, and environmental research.
In the world of IMUs, researchers are turning their focus to intelligence. Advanced meta-learning algorithms are enabling these sensors to self-calibrate with minimal input, paving the way for smarter, more adaptive wearables and mobile devices. Imagine motion trackers or health monitors that fine-tune themselves automatically to maintain accuracy, no matter the conditions—offering exciting possibilities for applications like stress monitoring and motion tracking.
Meanwhile, in temperature sensing, Endress+Hauser’s iTHERM TrustSens TM372 sets the benchmark for hygienic applications. Using the Curie method and an internal traceable reference, this sensor performs seamless self-calibrations, ensuring precise, reliable readings in critical environments like food and beverage processing, where safety and consistency are essential.
Want to Learn More?
Self-calibrating sensors are changing the game in so many areas, and there’s so much more to dive into if you’re curious. Here are some ideas to explore further:
Whether you’re a tech enthusiast, a professional, or just someone who likes knowing how things work, there’s so much to discover about self-calibrating sensors. These smart devices are only getting smarter, and their potential is only just beginning to unfold.
References and Further Reading
- Kang, Y., Mouring, S., de Clerck, A., Mao, S., Ng, W., Ruan, H. (2022). Development of a Flexible Integrated Self-Calibrating MEMS Pressure Sensor Using a Liquid-to-Vapor Phase Change. Sensors, 22(24), 9737. DOI: 10.3390/s22249737, https://www.mdpi.com/1424-8220/22/24/9737
- Barcelo-Ordinas, J. M., Doudou, M., Garcia-Vidal, J., Badache, N. (2019). Self-calibration methods for uncontrolled environments in sensor networks: A reference survey. Ad Hoc Networks, 88, 142-159. DOI: 10.1016/j.adhoc.2019.01.008, https://www.sciencedirect.com/science/article/abs/pii/S1570870518306115
- Pertijs, M. (2014). Calibration and Self‐Calibration of Smart Sensors. Smart Sensor Systems: Emerging Technologies and Applications, 17-41. DOI: 10.1002/9781118701508.ch2, https://onlinelibrary.wiley.com/doi/abs/10.1002/9781118701508.ch2
- Suo, C., Huang, R., Zhou, G., Zhang, W., Wang, Y., & He, M. (2023). Self-calibration sensor for contactless voltage measurement based on dynamic capacitance. Sensors, 23(8), 3851. DOI: 10.3390/s23083851, https://doi.org/10.3390/s23083851
Disclaimer: The views expressed here are those of the author expressed in their private capacity and do not necessarily represent the views of AZoM.com Limited T/A AZoNetwork the owner and operator of this website. This disclaimer forms part of the Terms and conditions of use of this website.