This article shows how LDE differential pressure (Δp) sensors from First Sensor are experimentally compared to other manufacturer’s sensors, which are based on the same (thermal-anemometer-based, non-membrane) sensing principle, where differential pressure is inferred from a gas flow via the sensor. With dust in the air flow, all other sensors having flow impedance 15 Pa/(ml/s) to 300 Pa/(ml/s) went out of calibration or failed entirely, while the LDE sensors having flow impedance >10 kPa/(ml/s) retained their calibrated sensitivity. First Sensor’s DE/LME/LMI Δp sensors need only small flows via their body, and thus have excellent immunity against dust-bearing air.
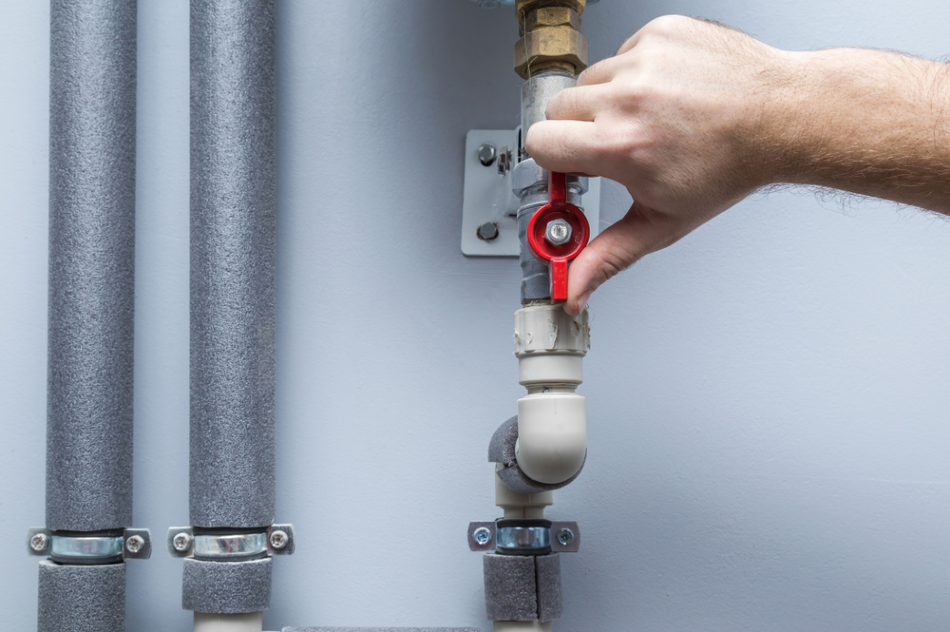
Image Credit: Shutterstock/FotoDuets
Flow-Through Leakage
During operation, nonzero air flow leakage occurs through the sensor due to the sensing mechanism. This holds true for all differential pressure sensors based on the thermal-anemometer sensing principle, (when compared to dead-end sensors such as piezo-resistive membrane-based sensors, whose sensing element does not leak).
Despite this fact, thermal-anemometer-based Δp sensors continue to have significant success in the marketplace, as they allow cost-effective and practical sensing of extremely low Δp, such as a few hundred Pa full-scale and below. The question that arises at this point is how much flow-through leakage is too much? The answer depends on application details, and on how the Δp sensor is linked and used.
Since Δp sensors are capable of measuring differential gas pressures below a few hundred Pa, with resolution better than 0.1 Pa, they may be influenced by other parts of the measurement system such as connecting tubes/pipes and filters as well as by the quality of the gas which may include liquid droplets, humidity or dust.
There are certain manufacturers of thermal-anemometer-based Δp sensors who advise the use of connection tubes with a specific length to ensure that the response of manufacturer-calibrated sensors is not distorted. In addition, manufacturers may propose the use of dust filters or may even use dust-segregation mechanisms/elements as part of their sensors. It must be remembered that such precautions are not necessary for membrane-type sensors, where there is zero gas flow via the connection tubing (in static mode).
In order to provide reliable long-term operation, designers of a flow-measurement system using a thermal-anemometer-based differential pressure sensor should consider a number of factors caused by non-zero gas flow via the sensor. However, no standard test/certification processes are available and no detailed technical information is there to deal with these issues. The tests described below were preformed with thermal-anemometer-based sensors from different manufacturers, to demonstrate the principle importance of the flow-through leakage (pneumatic impedance, or flow impedance) of the sensors, for reliable operation in practical applications.
Note: The pneumatic impedance Rpn of the sensor, measured in [kPa/(ml/s)], determines the flow of gas through the sensor at a certain pressure drop, Δps across the sensor:
Flow-through leakage = Δps / Rpn
Flow Measurement Using Differential Pressure Sensors
Normally, micro-flow-based differential pressure sensors are used to determine the differential pressure generated by the gas flowing through a “flow tube” or air-flow duct. Some examples include respiratory flow measurement in medical ventilators and filter control or air flow measurement in HVAC applications.
For instance, consider the sensor used in a shunt configuration to detect differential pressure Δp = p1 – p2 across a flow-restrictive element in an air duct, thus inferring measurement of air flow in the duct (Figure 1). These conversion elements are developed for various applications and include baffles, orifices, calibrated diaphragms, Venturi tubes, Pitot tubes and specialized flow-to-pressure converters that are used in respiration equipment such as Lilly or Fleisch tubes.
The differential pressure sensors, LDE/LME/LMI, are characterized by extremely high flow-through impedance, which is up to hundreds of kPa/(ml/s) for higher full-scale ranges and higher than 10 kPa per (ml/s) for the most-sensitive models. When compared to other sensors with lower flow impedance, differential pressure sensors with high flow impedance require less parasitic flow to make a measurement, and hence, cause fewer disturbances to the main flow. This makes the latter almost equivalent to dead-end type or membrane-type differential pressure sensors with regard to this critical aspect of performance for many different applications.
.jpg)
Figure 1. Typical volumetric flow measurement set-up with differential pressure sensor. Image Credit: First Sensor
Risk from Dust Contamination
In HVAC applications, dust particles may be present in the main air flow. This raises a question whether such dust particles pose a reliability hazard to thermal-anemometer-based sensors. During the normal function of sensor, the air flows through the flow-channel which means that such air flow may also carry dust particles to the flow channel of the sensor. Therefore, the hypothetical hazards from dust particles are that they could enter the flow channel of the sensor, causing:
- A change (increase) in the internal flow-impedance of the sensor and thus a change (decrease) in the calibrated sensitivity of the sensor. This would be viewed as a loss of calibration, and a reduction in the sensor’s output voltage, for a given applied Δp
- A complete blockage of the sensor’s internal flow channel (functional failure)
- Dust may stick on or close to the sensitive microstructures that constitute the sensing element within the channel, causing a change in calibration
In principle, the presence of dust may pose a reliability hazard, but the extent of the hazard is mainly governed by the flow-through impedance (pneumatic impedance) of the sensor.
Risk Factors
Dust Quantity and Air Velocity
The amount of dust particles which the air flow transfers to the sensor depends both on the amount of air passing through the sensor and the velocity of air flow. In addition, the amount of dust particles induced to travel into the air flow channel of the sensor depends on the amount of dust particles present at its input as well as on the velocity of air flow into the channel.
Another important effect is caused by the velocity of air flow toward the sensor, beyond the simple volume of air transported to and into the sensor. If the velocity of the air flow is slow enough that the dust does not remain airborne, then this can further improve the sensor’s immunity to dust contamination. If the velocity of air flow toward the sensor is great enough that the dust remains in suspension, then this may reduce the sensor’s immunity to dust contamination.
Note: The flow-impedance of the sensor directly affects the velocity of approaching airflow. Therefore, high flow impedance in the sensor not only reduces the volume of air traveling through the sensor’s channel, but also reduces the velocity of the approaching air, possibly enabling airborne dust to settle out and also reducing the force on particles that are already present at the sensor input.
Type of Dust
For instance, compared to small/light particles, large and heavy dust particles have less chance to be transported via the tubing to the sensor. Further, the dust particle size affects whether the dust can physically obstruct the air flow into the flow channel of the sensor, and whether the dust can physically reach the flow channel of the sensor.
Dust Particle Concentration in the Main Flow
The concentration of dust approaching the sensor is directly proportional to the concentration of dust present in the main gas flow.
Connection of the Sensor to Main Flow Duct
Referring to Figure 1, if the inner diameter of the connection tubing is larger, the linear velocity of the gas flow of dust-bearing air toward the sensor input will be lower. Moreover, if the connection tubing is longer, the flow impedance contributed by that connection tubing will be greater, which, in turn, can impact the linear velocity of the gas flow of dust-bearing air toward the input of the sensor. The presence of dust filters and dust collectors (such as gravity traps) can, to some extent, protect the sensor from dust.
Note: The aim of this experiment is to estimate and compare the sensor’s immunity to dust contamination. Any improvement related to dust filtering and other extra protection of the sensors is beyond the scope of the present investigations.
Experimental Investigation of Dust Contamination
Comparative experimental studies were performed to examine the risk posed by dust. Therefore, the experimental setup was designed and developed to provide controllable and reproducible conditions for the tested sensors as well as to facilitate a fair comparative analysis of various sensors. Keeping this target in mind, sets of Δp sensors based on the thermal-anemometer sensing principle were exposed to applied differential pressures. In all the experiments, two or more sensor samples, usually having different flow impedances, were linked in parallel so that all sensors have a common differential pressure.
Test #1
In the initial test, the following sensors,
- Sensor 2-1
- LDES250UF6S (# 2)
- LDES050UF6S
were connected in parallel to the dust chamber, as shown in the first configuration in Figure 2 (with the sensors organized in a horizontal way at the same level as the dust chamber). The test was then run for a period of 20 hours at a constant differential pressure Δp = 200 Pa (0.8 in H2O).
.jpg)
Figure 2. Schematic diagram of horizontal configuration. Image Credit: First Sensor
.jpg)
Figure 3. Schematic diagram of vertical configuration. Image Credit: First Sensor
Figure 4 shows the coarse-characterization results for Sensor 2-1. For the two LDE sensors, the before and after fine-characterization results are illustrated later in Figures 11 and 12. From Figure 4, it is apparent that Sensor 2-1 has considerably changed its calibration (output dropped by over 50%), following 219 minutes and has fully failed towards the end of the 20 hours of dust exposure.
From Figures 11 and 12, it is also apparent that the response curves of both LDE sensors remain unchanged even after 20 hours at 200 Pa. As expected, there was a significant difference between the LDE sensors and the Sensor 2-1 because the difference in flow impedance is a factor of at least 1000x. This means over thousand times more volume of air went through Sensor 2-1, and that the flow velocity of dust-bearing air toward Sensor 2-1 was also more than 1000 times faster.
.jpg)
Figure 4. Test #1 results for sensor 2-1 (horizontal orientation of the sensor). Image Credit: First Sensor
It must be noted that far less dust residue was observed within the connection hoses to the LDE sensors, while a significant amount of dust residue was observed within the few inches of transparent connection hoses to Sensor 2-1.
Auxiliary Test #1a
To verify this type of test, an additional 20-hour test was run on Sensor 2-3, together with another LDES250UF6S sample, the same type as the one employed above in Test #1.
It was observed that the graphical results were quite similar to those illustrated above (see Figures 4 and 11). After a few hours, the output of Sensor 2-3 was considerably reduced and dropped almost to zero following 20 hours of dust exposure. Again, the output of the LDE sample remained effectively unchanged even after the entire 20 hours.
Subsequent to this 20-hour test, both samples were opened up (dissected) to identify the failure mechanism in Sensor 2-3. Large amounts of agglomerated dust particles were present within the Sensor 2-3 housing, including a considerable quantity just within the air inlet point. Further, the tested LDE sensor housing was opened up, but there was no evidence of dust at the input port through which the air flowed prior to reaching the sensing element.
Test #2
In the second test, the following sensors,
- Sensor 1-1
- Sensor 3-1
- LDES050UF6S
- LDES250UF6S (# 1)
were connected in parallel to the dust chamber, as shown in the first configuration in Figure 2 (with the sensors organized in a horizontal way at the same level as the dust chamber). The test was then run for a period of 18 hours at a steady differential pressure Δp=450 Pa (1.6 in H2O). The pressure applied was close to the full-scale of Sensor 3-1, and was also above the full-scale of all the other three sensors used in the test, such that the output voltage of the sensors was saturated during the test.
Figures 5 to 7 show the coarse-characterization results, and Figures 10 and 12 show the before and after signal-pressure characteristics for LDE samples.
From the results shown in Figure 5, it is obvious that Sensor 1-1 has already changed its calibration after a period of 1 hour, and its output has also dropped by over 50% following 2 hours of exposure to dust-bearing air. It must be remembered that the zero-offset also changes after 2 hours. From the results shown in Figure 6, it is clear that Sensor 3-1 has entirely failed between 2 hours and 18 hours of dust exposure.
Figure 7 shows that the coarse response curve of the LDES250UF6S (# 1) sensor remains unchanged after a period of 1 hour, 2 hours and 18 hours. The characterized before and after comparison (Figure 10) also shows that the response of this sensor indeed remains unchanged after the entire 18 hours of dust exposure.
.jpg)
Figure 5. Test #2 results for sensor 1-1 (horizontal orientation of the sensor). Image Credit: First Sensor
.jpg)
Figure 6. Test #2 results for sensor 3-1 (horizontal orientation of the sensor). Image Credit: First Sensor
Results for the LDES050UF6S sensor are shown in Figure 12. This sensor is the same sample used in the initial comparison test described in test #1 earlier in this article. The before and after measurements again show that the response of the sensor definitely remains unchanged even after 18 hours of dust exposure, in addition to the precious 20 hours of dust exposure.
As expected, there was a major difference between the LDE sensors and sensors 1-1 and 3-1 because once again the difference in flow impedance is two orders of magnitude or beyond. Again, much more volume of air flowed through sensors 3-1 and 1-1, and once again the flow velocity of dust-bearing air toward sensors 3-1 and 1-1 was many times faster.
Again, far less dust residue was observed inside the connection hoses to the LDE sensor, while a significant amount of dust residue was observed within the few inches of transparent connection hoses to sensors 3-1 and 1-1.
.jpg)
Figure 7. Test #2 results for LDES250UF6S (# 1) (horizontal orientation of the sensor) 9. Image Credit: First Sensor
Test #3
In the third test, a couple of LDE sensors were used that were also used in the above-described tests above; sensor samples,
- Sensor 2-2
- Sensor 3-2
- LDES050UF6S
- LDES250UF6S (# 2)
were connected in parallel to the dust chamber, as shown in the second configuration in Figure 3 (with the sensors organized in a vertical fashion above the dust chamber). The test was then run for 27 hours at a steady differential pressure Δp=250 Pa (1 in H2O). The pressure applied was within the sensing range of sensor 3-2, close to the full-scale of LDES250UF6S and also above the full-scale of the remaining two sensors used in the test, so that the output voltage of these sensors was saturated during the test.
Figures 8 and 9 show the coarse-characterization results, and Figures 11 and 12 show the before-and-after fine characterization results for LDE samples.
Note: The two LDE sensors are the same sensor samples that were previously subjected to many hours of dust-bearing air pressure in TEST #1 and TEST #2 above.
Figures 8 and 9 show the results, which indicate that when the sensors are vertically oriented above the dust chamber, it takes relatively longer for the sensors under test to be affected. Sensors 2-2 and 3-2 have both considerably lost calibration after a period of 25 hours, and have continued to lose calibration more significantly after a period of 2 more hours (it takes a total of 27 hours of dust exposure for each sensor). This is expected because the effect of gravity acts to either reduce or delay the flow of dust particles upward toward the inputs of the sensors.
.jpg)
Figure 8. Test #3 results for Sensor 2-2 (vertical orientation of the sensor).Image Credit: First Sensor
.jpg)
Figure 9. Test #3 results for Sensor 3-2 (vertical orientation of the sensor). Image Credit: First Sensor
.jpg)
Figure 10. Characteristic of LDES250UF6S (# 1). Image Credit: First Sensor
.jpg)
Figure 11. Characteristic of LDES250UF6S (# 2). Image Credit: First Sensor
.jpg)
Figure 12. Characteristic of LDES050UF6S. Image Credit: First Sensor
In Figure 11, it is seen that the characteristic curve of the LDES250UF6S (# 2) sensor remains unchanged after these extra 25+2=27 hours of dust exposure, ahead of the original 20 hours of dust exposure from TEST #1.
In Figure 12, it is observed that the LDES050UF6S sensor may be at last changing its calibration by just a few percent, following these extra 25+2=27 hours of dust exposure, ahead of the original 20+18=38 hours of dust exposure from both TEST #1 and TEST #2.
The LDES050UF6S sensor has a lower flow-impedance of ~30 kPa/(ml/s) versus ~80 kPa/ (ml/s), and hence, it would be affected before its neighbor LDES250UF6S, as expected.
Again, there is a major difference between the LDE sensors and the sensors 2-2 and 3-2 as expected, because once again the difference in flow impedance is two orders of magnitude or beyond. Again, much more volume of air flows through the 2-2 and 3-2 sensors, and the flow velocity of dust-bearing air toward the 2-2 and 3-2 sensors was again many times faster.
Once again, far less residue was seen within the connection hoses to the LDE sensors, while significant amount of dust residue was observed within the few inches of transparent connection hoses to 2-2 and 3-2 sensors, even when oriented vertically. Again, this is consistent with the idea that the air-flow volume and velocity are limited by the high flow-impedance of LDE sensors to such an extent that almost all the dust has fallen out of suspension before approaching the LDE sensor.
Conclusions
With regard to differential pressure sensors that are based on the thermal-anemometer sensing principle, which involves small leakage through the air flow channel of the sensor. The flow impedance of that air flow channel is a crucial factor for determining both the ease of use and immunity of sensor to dust-contamination.
Using the same sensing principle and with dust in the air flow, First Sensor’s LDE sensors with a flow impedance of >10 kPa/(ml/s) were directly compared with other manufacturers’ sensors having flow impedances of 15 Pa/(ml/s) to 300 Pa/(ml/s).
In all the cases, it was observed that sensors with lower flow impedance lost calibration and/or failed entirely after hours to tens of hours of standard operation. The LDE sensors, by contrast, did not display any major change in calibration.
The high flow impedance causes several effects:
- It reduces the volume of dust-bearing air which can reach the input of the sensor
- It reduces the velocity of air flow toward the input of the sensor, enabling more dust to drop out of the flow before it approaches the input of the sensor
- It reduces the force on dust particles at the input of the sensor’s flow channel
When the air flow connection to the sensor is oriented vertically such that the flow of dust-bearing air must rise toward the sensor input, the effect of dust exposure is reduced.
The less air flow the sensor needs through its body to make its measurement, the more ideal the behavior of the sensor is, and the better the immunity to dust-bearing air. First Sensor’s LDE/LME/LMI Δp sensors provide extremely high flow impedance and thus considerable benefits.
Potential users of thermal-anemometer-based Δp sensors can repeat the same or similar dust tests to confirm suitability for use within the conditions of their own specific applications.

This information has been sourced, reviewed and adapted from materials provided by First Sensor AG.
For more information on this source, please visit First Sensor AG.