When an emergency event takes place at an oil/gas/petrochemical unit that involves fire or leaking gas, the consequences of failing to react appropriately can be devastating. The course of action undertaken within the first few seconds and minutes can make the difference between an successfully avoided accident and a fatal tragedy, where lives and equipment can be lost.
Unfortunately, once an emergency situation occurs it is too late to put in place the safety regime and monitoring equipment that are required to protect a unit and avoid such an accident. Implementing a culture of safety within a company and its operations is the only approach to guarantee that any unit or group of employees will be prepared for the emergency events that can happen in hazardous industries.
Protecting Terminals and Tank Farms
Marine terminal and tank storage operations are no less resistant to accidents than upstream production sites and petrochemical refinery operations. They do, however, pose some different safety challenges that, when managed incorrectly, have the potential for disastrous events.
Such facilities are often large in size, with extremely dense operations involving numerous petroleum products. Transferring refined petroleum products, crude oil, or natural gas from ship to shore for tank storage and then distributing them to the end customer/consumer is a multifaceted process, with plenty of opportunities for fatal leaks and spillage.
The infrastructure at tank farms and terminals is commonly a maze of pumping stations, docks, pipelines, operations centers, rail car terminals and tracks, storage tanks, truck loading stations and more. The scope of varied activity taking place makes safety management both the highest priority and one of the hardest jobs.
Fixed Gas and Flame Detection
The main safety threat at terminal and tank facilities is the potential leak of various combustible or deadly gases and flames. The main sources of these nuisance flames and gases are the products passing through the unit:
- Fuel oil
- Crude oil
- Gasoline
- Diesel
- LNG/LPG
- Jet fuel
- Various chemicals
.jpg)
Hazardous gas leaks and flame incidents can possibly take place almost anywhere throughout the unit and require wide-ranging fixed gas and flame detector monitoring. Equipment types where flames and leaks are typically found include pipelines, valves, pumps, tanks and hoses.
Employees involved in operations and maintenance activities must also regularly carry portable gas detectors. These are potential life saving devices when entering, maintaining or inspecting equipment where fixed gas detection is not essentially practical or desirable.
Multi-Layer Sensory Model
It is unsurprising, with the numerous challenges to reliable gas and flame detection, that a new strategy is emerging to enhance safety in hazardous industries. What if all of the portable and fixed hazard detection sensor technologies were integrated together and then layered where they ideally fit in terms of their reliability in each unique plant layout? (Figure 1)
.jpg)
Figure 1. MSA GM Fixed Gas and Flame Safety System.
Gas and flame detection sensing technologies imitate the senses of people, and the people who created them. For instance, ultrasonic sensors 'hear' gases and catalytic bead sensors ‘sniff’ gases, infrared (IR) and optical type sensors ‘see’ gases and flames. What if these detectors acted more like people, reacting based on their intelligence and remembered past memories?
Layering portable and fixed sensor technologies all over the plant, where they ideally fit in terms of their reliability, accomplishes a human sensory chain of defense against dangerous gases and flames. To better comprehend this new model of human sensory gas and flame detection, each type of sensing technology should be assessed and then deliberated.
Electrochemical Cells
Fixed and portable gas detectors are currently built with very effective electrochemical cells, which measure the concentration of a specific gas by oxidizing it with an electrode and measuring the resultant current. Different types of cells have been created for specific lethal gases, such as chlorine, ammonia, carbon monoxide etc., and combustible gases.
Catalytic Bead (CB)
Catalytic bead gas detectors use catalytic combustion to measure combustible gases in the air at fine concentrations. As combustible gas oxidizes in the presence of a catalyst, it generates heat, while the sensor converts the temperature increase to a change in electrical resistance, which is linearly proportional to gas concentration. A standard Wheatstone bridge circuit converts the raw temperature change into a sensor signal.
Point Infrared (PIR)
In PIR detection, two wavelengths are used: one at the gas absorbing ‘active’ wavelength and the other at a ‘reference’ wavelength not absorbed by the gas. Both wavelengths are not absorbed by other typical atmospheric components such as water vapor, oxygen, nitrogen or carbon dioxide. In PIR detectors, the concentration of hydrocarbon gas is measured via the IR absorption of an optical beam, referred to as the active beam. A second optical beam, referred to as the reference, follows the identical optical path as the active but contains radiation at a wavelength not absorbed by the gas.
Open PIR (OPIR)
In OPIR detection, the path of the IR beam is extended from less than 10 cm, common of PIR detectors, to greater than 100 m. These devices use individual IR transmitters and receivers that are contained in different enclosures. There are OPIR detectors available that monitor in both the lower explosive limit-meter (LEL-m) and parts per million-meter (ppm-m) ranges to detect both large and small leaks. They cover large open areas, along a line of several probable leak sources such as a row of pumps or valves and also for perimeter monitoring of leaks.
Ultrasonic (UGLD)
When deliberated in comparison to conventional gas detectors that measure %LEL, advanced ultrasonic gas leak detectors with neural network technology (NNT) include a pattern recognition capability that reacts to the ultrasonic noise produced by a pressurized gas leak. This ultrasonic noise offers a measurement of the leak rate and fixes warning and alarm thresholds. Gas does not have to reach the sensing element because the detector ‘hears’ the gas leak. They are best suited for indoor spaces with high ventilation rates and outdoor installations.
Ultraviolet/Infrared (UV/IR)
By integrating a UV sensor with an IR sensor, a dual band optical flame detector is formed that is sensitive to the IR and UV radiation discharged by a flame. The resulting UV/IR flame detector offers better immunity over a UV-only detector, works at moderate speeds of response and is suited for both outdoor and indoor use.
Multispectral Infrared (MSIR)
The advanced design of MSIR flame detectors operates with an IR-based sensing array integrated with NNT intelligence. This NNT intelligence offers pattern recognition features that help train the detector to distinguish between real threats and normal events, thus minimizing false alarms. MSIR technology permits area coverage up to six times greater than that of more conventional UV/IR flame detectors.
Integrated Emergency Response
An integrated approach to process and plant safety at tank farms and terminals, which includes emergency response, offers many advantages. The unit operations and process engineering teams are brought together to review possible hazards across the whole unit.
What is presently in place, including fixed gas and flame monitoring systems, respiratory apparatus, portable gas detectors, fall protection and safety gear (e.g. gloves, goggles, hats, and more) are then reviewed. The needs of onsite emergency fire departments that handle accidents when all else fails must be carefully deliberated.
For instance, when unit safety teams are not aware of the total effects of probable hazards, they need to ensure that they are using a suitable portable gas detector (Figure 2) or sensing technology for the potential threat. Some compounds can signify both a toxic and combustible threat. Although a combustible/LEL sensor may sense explosive levels at the % LEL or % volume levels, toxicity may take place at much smaller levels, measured in ppm, so a different technology or sensor may be required; a good example of this is benzene.
.jpg)
Figure 2. MSA ALTAIR 5X portable gas detector.
New 3D facility mapping software tools as seen in Figure 3 can help process and plant Engineers to enhance flame and gas detector resources without speculation, so as to maximize system accuracy while reducing cost. For gas mapping, the software’s algorithms incorporate numerous gas release and dispersion scenarios that could happen and gas detector sensitivity.
.jpg)
Figure 3. 3D gas and flame safety mapping software.
To map flame dangers, the software’s algorithms take into consideration the flame detector’s field of vision (FOV), the radiant heat output (RHO) of the target flame, its sensitivity settings, its obstructions and obstructed flame plumes. The software’s modeling results are shown in graphical color-coded coverage maps, which specify the extent of flame and gas coverage.
The software’s multi-stage mapping process mainly exhibits a plant map with 0% protection, and then exhibits the incremental placement of detectors to attain 60, 90 and 99% coverage. The final result is a comprehensive 3D rendering of the plant, enhanced with all detectors in place for better safety and reliability.
Conclusion
Protecting terminals and tank farms from the potential consequences of the dangerous gas leaks and fires of today, requires a combined approach to safety and emergency response. Once an accident event occurs, it is too late to put in place a safety regime; safety is a constant process that needs total personnel participation to guarantee success.
Establishing a culture of safety through evaluation and training is the primary step. Completing a united review of unit safety, with both the unit and the process teams, will identify possible problems before accidents happen. Partnering with safety professionals who offer 3D facility gas and flame mapping, with the next generation of very intelligent multi-sensory detectors, provides the ‘state of the art’ in safety monitoring.
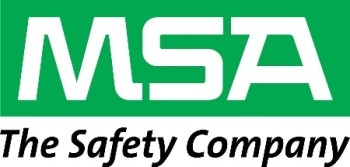
This information has been sourced, reviewed and adapted from materials provided by MSA - The Safety Company.
For more information on this source, please visit MSA - The Safety Company.