Measuring the pressure between two nip rolls no longer needs to be guesswork. The Nip Pressure Alignment Tool™ (NPAT™) can be used to record nip footprints and the associated pressure distributions. The composition of the band arrangement in the NPAT sensor means that a large surface area can be covered with only one data acquisition (DAQ) handle.
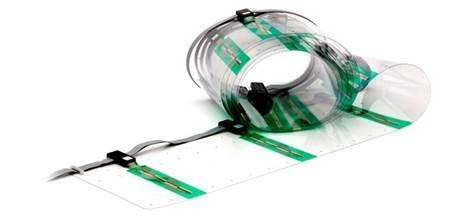
NPAT System Rolled
With access to real-time measurements, the NPAT provides confirmations of uniform pressure and nip contact, measuring and displaying data of nip widths that range from 6.35 mm (0.25 inches) to 215.9 mm (8.5 inches).
How to Use NPAT
In order to get the most out of the NPAT, there are a number of key features users can access:
How to Use NPAT: Verifying Nip Roll Uniformity Made Easy
Key Features
- Carrier to keep the bands/housing properly aligned during use
- Enclosure for the Evolution™ handle that protects electronics in rougher applications
- Bands that can be easily exchanged and serviced in-field
- Configurable array of sensing bands
- Rollers can be easily stored
- Different roll sizes are catered to, with a choice of three sensor model resolutions
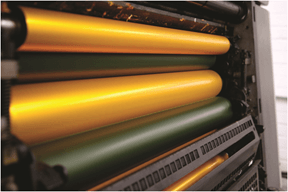
Verify nip pressure
Benefits of Measuring Nip Pressure
There are great benefits in being able to measure Nip pressure accurately, such as:
Having an easy to understand visual representation of pressure distribution, nip width, and cross width, being able to ensure that rolls are aligned correctly; avoiding equipment damage; producing measurable and reliable data; and being able to service and repair an application, without needing to send hardware off to an external site.
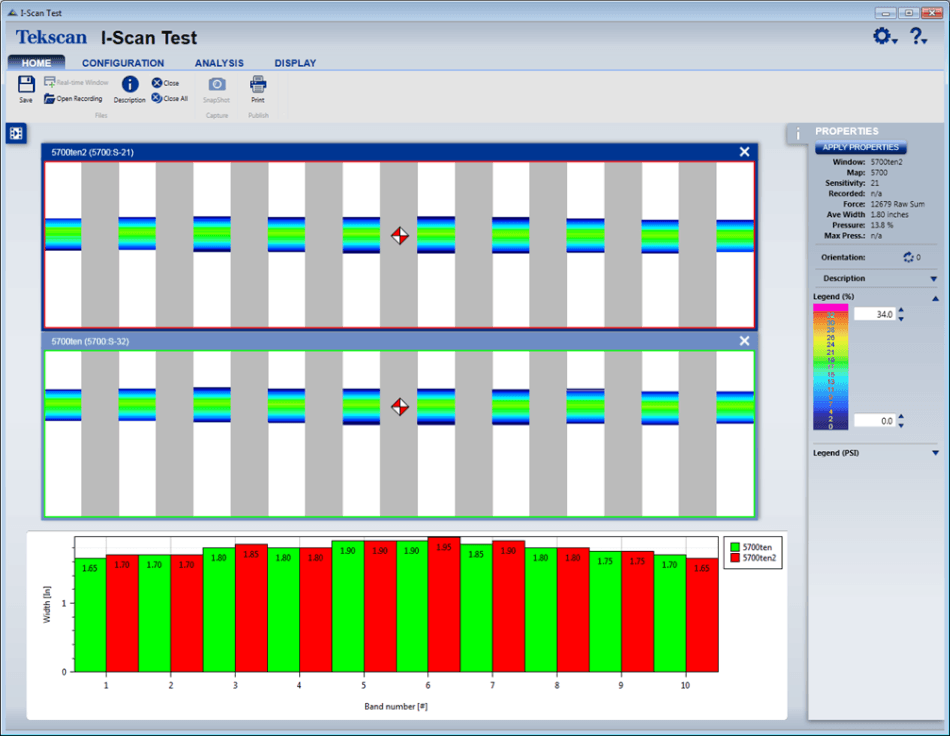
NPAT Software Output
Configurations
The NPAT™ uses a sensor containing an array of thin and flexible pressure sensitive bands that are setup according to the size of a given roll. The results produced by the NPAT ensures accurate configuration and roll alignment, enabling users to achieve a greater production yield.
Tekscan’s range consists of nine standard systems that users can choose from, each with their own spacing. Each system has a nip sensing width between 44.45 mm (1.75”) and 223.5 mm (8.80”) and can record pressures of a maximum of 4,500 psi.
The table below compares three sensor types (5700, 5707 and 5705) and their systems:
Standard Options
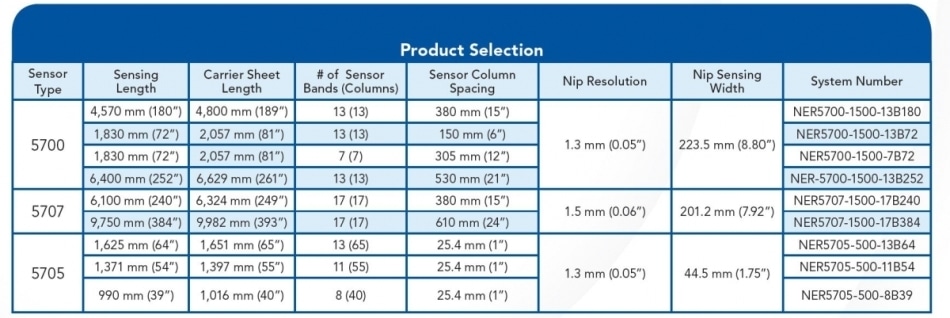
System Configuration - NER5700 & NER5707
The 5700* and 5707** systems have one column per band. These systems are well-suited for larger rolls in the printing industry.
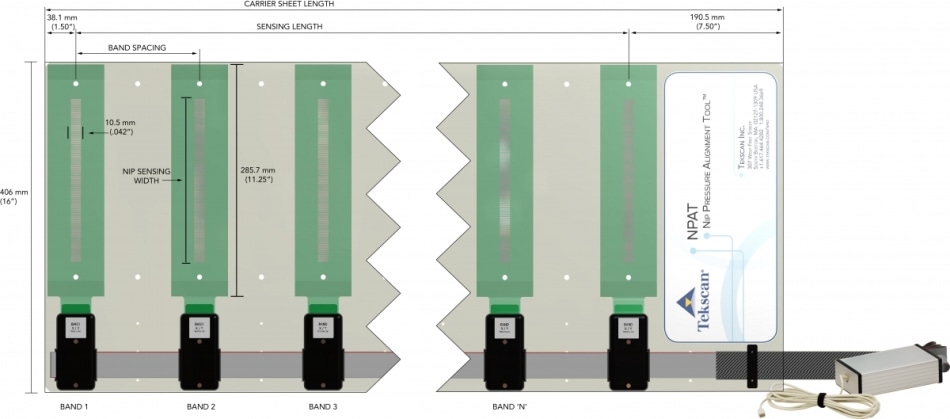
* 5700 Sensing Band (1 column per band; MAX 13 bands/13 columns) is used to make sensors between 457.2 mm (18”) and 6,400.8 mm (252”).
** 5707 Sensing Band (1 column per band; MAX 17 bands/17 columns) is used to make sensors between 1,524 mm (60”) and 10,000 mm (396”).
System Configuration - NER5705
The 5705*** system has 5 columns per band and the spacing of the columns is locked at 25.4 mm (1"). This system is perfect for smaller rolls in the film and converting industry.
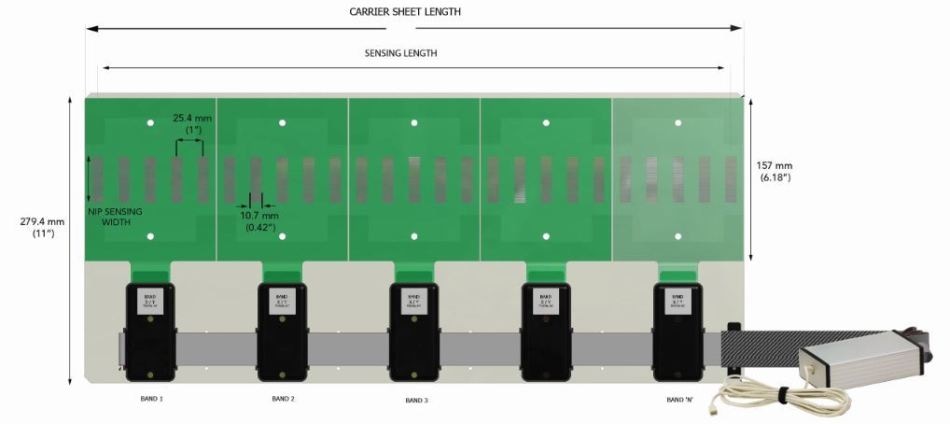
*** 5705 Sensing Band (5 columns per band; MAX 13 bands /65 columns) is used to make sensors between 355.6 mm
(14”) and 1,625.6 mm (64”).
Software
The display screen of the software is simple and easy for the user to navigate, meaning that the machine set-up process is quick and efficient. There are a range of features that enhance usability and makes the identification of nip uniformity easy.
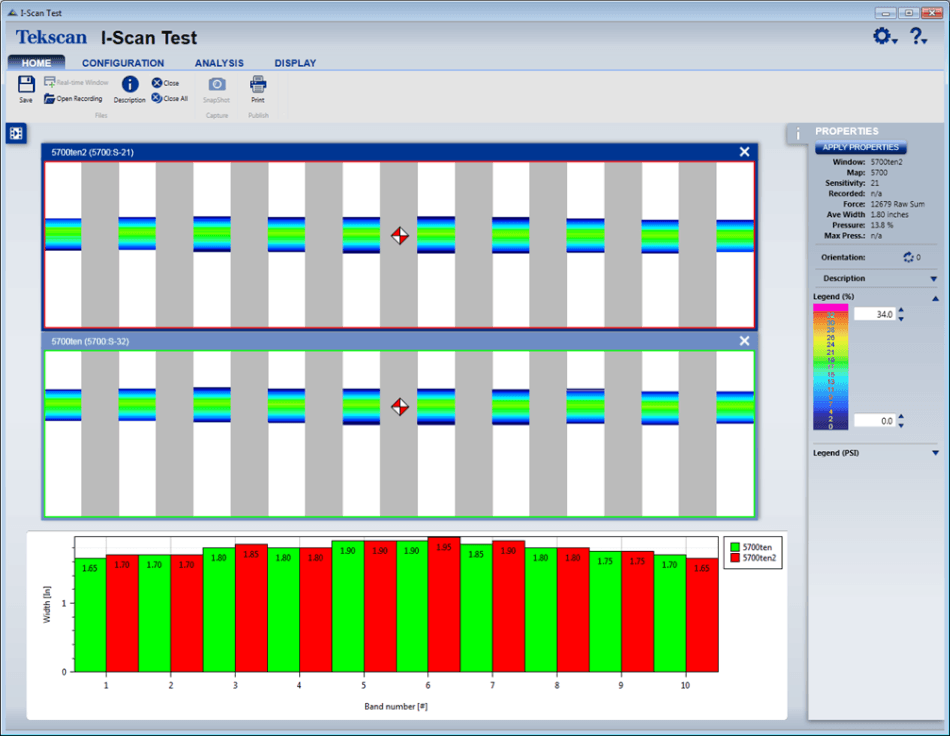
Compare previous reference snapshot
Images of the measured pressure distribution from each band can be saved. Other software features include: live display of pressure profile on bands across roll; graph nip width & relative force of each sensing band; center of force - cursor verification of equal load from bearings; color scale of pressure values; comparison of real-time data with reference measurements; and ability to use with existing Evolution handle.
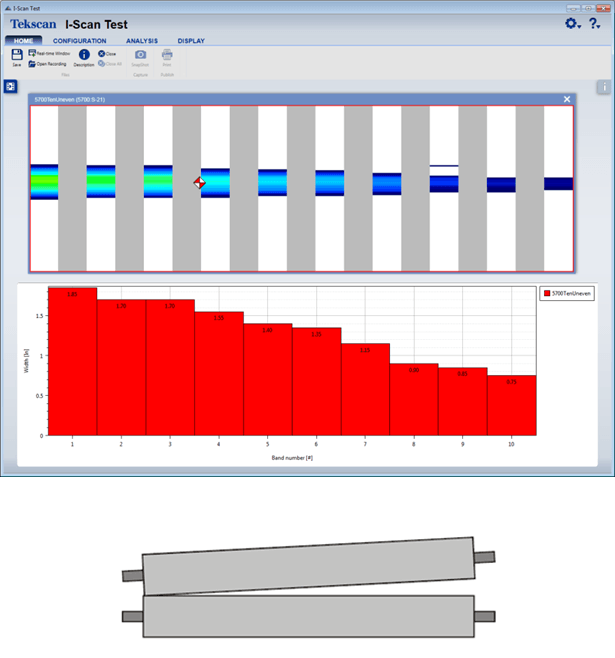
Software showing roll misalignment
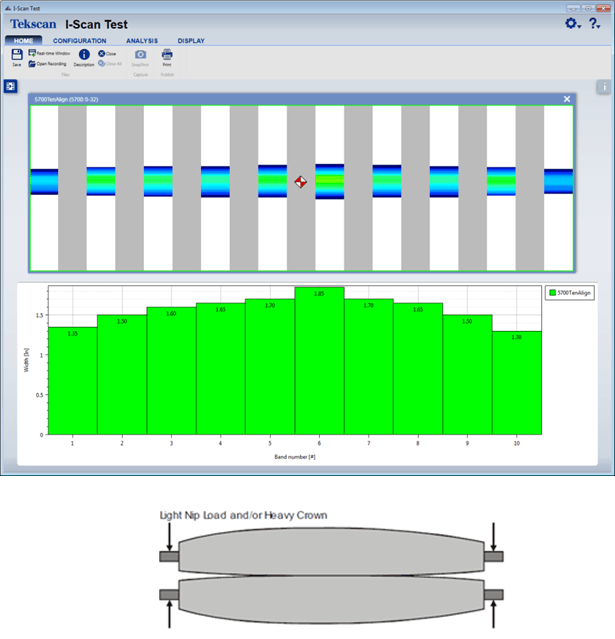
Software showing heavy crown or misalignment
Applications
There are many industry applications that already reap the benefits of using the NPAT, including iron and steel works, printing, mills, laminators, film, coaters, die press, converting and packaging.
The NPAT™ tool can be used to set-up machines, compare the performances of different machines and identify problems such as crowns, misalignment, deflections and diameter variations during operation.
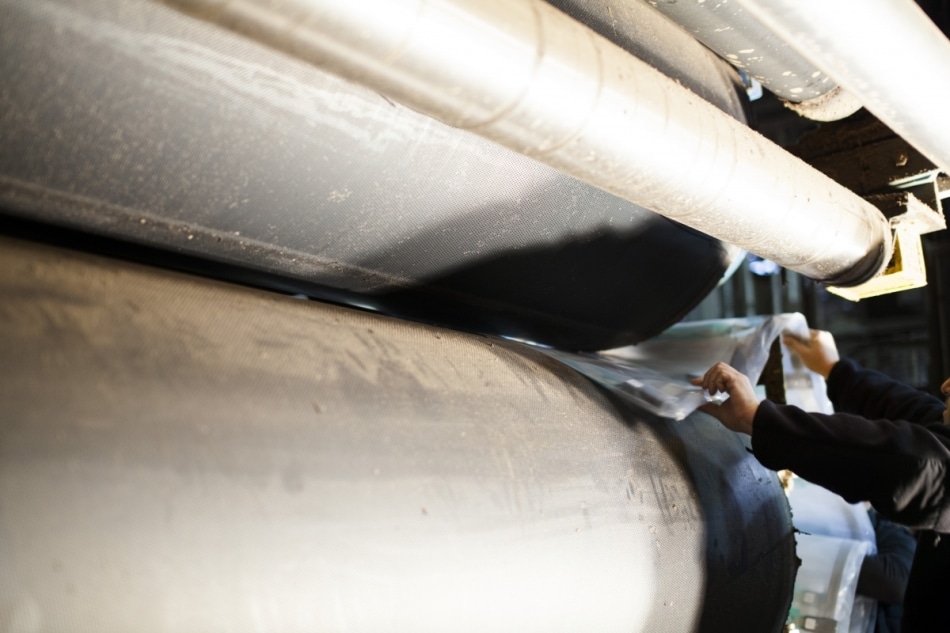
Nip Roller
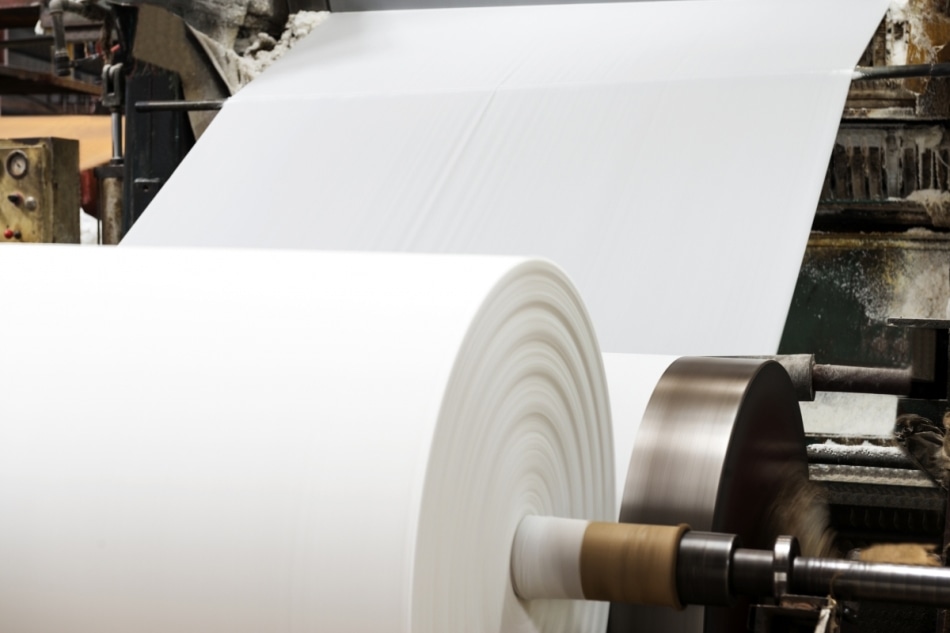
Paper Mill