CAS DataLoggers has supplied a Delphin TopMessage data acquisition system and ProfiSignal software to a magnet producer, who wanted to increase the quality of production and reduce rework.
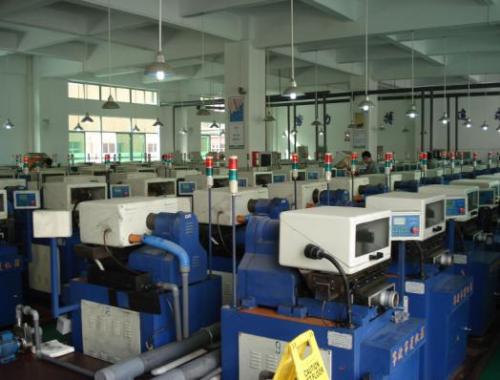
Several processes like powder processing, sintering, pressing and the actual manufacturing processes are required to manufacture magnets. Sintering plays a major part as it can lead to a 25% loss, due to magnet’s density acquired before the sintering process. A uniform green density has to be achieved during the pressing procedure.
The weighing machine used in the process has an RS232 port that is used for transmitting data about the weight. A system for acquiring, monitoring and evaluating various parameters, such as pressing force and weights and which also had PLC compatibility, was required by the magnet manufacturer. The Delphin TopMessage data acquisition system helped in addressing these requirements. It had Profibus DP and RS232 interfaces, universal analog and digital input/outputs and virtual channels for performing process calculations, control and monitoring operations.
The ProfiSignal software provided header data and process parameters to the TopMessage device and also worked as a connecting medium between the equipment and the user. It had OBDC/SQL interfaces that facilitated import and export of external data. The manufacturer was able to simultaneously display and compute densities and record all the data. The data was accessible to the management over the network, allowing evaluation to be performed at any point of time. The ability to respond more quickly led to significant improvement in quality.