Cavity pressure and cavity temperature sensors in the injection mold are the central components for an all-over process monitoring and process control in injection molding.
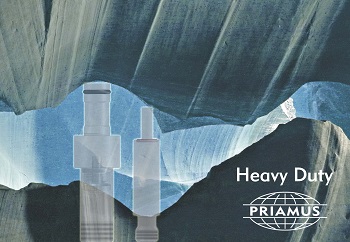
This is because they directly measure the molded part, and whether the quality is within the required limits or not. In many cases however this is precisely the problem because abrasive, highly filled, and chemically corrosive plastic melts gradually damage the sensor front. The life time of the sensors is therefore limited with such applications.
PRIAMUS has therefore developed a new and patent filed procedure in order to manufacture the sensor front from an extreme hard and chemically resistant material which extends life time significantly. Alternative methods such as thin layers of Titanium Nitride or chromed surfaces have not proved themselves in the past. This was because they did not withstand the wear, the surfaces were washed away, or because the outline of the sensor front could not exactly be mapped. The consequence was a visible mark on the molded part.
Cavity temperature sensors with hardened sensor front are successfully being used in these highly abrasive conditions. These applications have proved that even under such extreme conditions a significantly longer life time can be achieved.
Cavity pressure sensors are now also available with hardened sensor front and allow the reliable use e.g. with highly filled materials or with ceramic melts.