Motorsport teams face a variety of challenges every day. A racing car is not just one engineering problem, but a collection of inter-related engineering problems. Some of these problems are well understood while others are somewhat of a mystery. In order to learn and understand these unknown problems, engineers need new modern tools and instrumentation that will allow them to make measurements that cannot be made by conventional data acquisition sensors or systems.
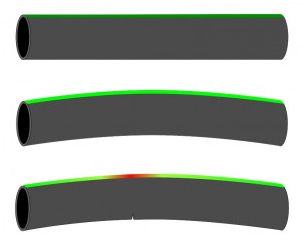
Why different materials need different test technologies?
Material testing in general and mechanical strain measurement in particular is nothing new in this industry and fiber Bragg gratings (FBG’s) as well as electric strain gauges amongst other instrumentation have been used for many years to help in the design, optimisation and validation of critical components. However with modern lightweight materials increasingly being used in these as well as and in mass-production vehicles, a more thorough understanding of material performance is required over the life of the product.
Cracking, fatigue and delamination of composite materials continue to be primary aging mechanisms and given the non-homogenous nature of composite materials, the assumption that strain is uniformly distributed across a test article is no longer valid. As such use of electric strain gauges or FBG’s at a few discrete points is not necessarily a true guide to structural integrity. Real confidence in the structural health of a component over a variety of operating conditions can be achieved only through accessing the full strain (or temperature) profile.
Why use distributed sensing?
To obtain a full strain profile over a component (or complete vehicle chassis), it is necessary to use tens, hundreds or even thousands of closely spaced tiny sensors, which may be impractical or uneconomical using traditional methods. By using an OFDR distributed sensing technique, it is possible to measure the strain or temperature condition at each and every one of those sensor points and this information is used by the software to develop a strain or temperature profile. As the optical fiber is also very small, flexible and extremely lightweight; it is a perfect sensor for high resolution sensing within the weight-conscious motorsports industry.
What measurements are possible?
Within the motorsports industry, the possibilities are limitless but would certainly include:
- Chassis / Monocoque flex or twist
- Temperature distribution inside the engine
- Design optimization of mechanical structures
- Fatigue testing of structures over time
- Integrity of fuel tank enclosures and welds
Below is a basic depiction of the types of measurements that can be performed. The coloured stripe on the top of the tube is an indicator of the strain level. Consider a round tube that has been instrumented with optical fiber on the top of the tube. When a load is applied to the centre of the tube with the ends fixed, the tube will deform (depending on the amount of load applied) and the strain will be measured by the optical fiber. In the unloaded state (top image), the strain is uniform and zero across the full length of the tube. When the load is applied in an upward direction in the centre of the tube, the tube will bend and the strain across the full length will again be uniform, but it will no longer be zero (middle image). However, a defect present in the tube will yield a strain measurement that is much higher around that defect (bottom image). This is an especially important measurement when the defect is so small that it cannot be seen by visual means or once mounted on the vehicle is hidden from view.
Formula One like the automotive industry pushes the boundaries to optimise design and reduce weight. This results in new high-tech materials that promise improved performance as well as increased longevity. To understand these new materials and how they perform in their harsh operating conditions, it is necessary to match these advancements with the appropriate test technologies.
In any test environment there is the potential for either electrical or mechanical influence by another component or sub-system. Unlike electrical strain gauges the optical fiber is passive and contains no electrical power, which means it is unaffected by electromagnetic interference (EMI) from other electrical components or sub-systems in close proximity. Mechanical influence on the test subject is minimal due to the tiny proportions of fiber.
Using sensors made from low-cost optical fiber, with almost no limit to the number of sensor designs available results in a cost-effective and versatile testing platform. With easier implementation, a reduction in integration and test time, reduced complexity and no cumbersome wiring loom to worry about, it is little wonder that the Formula One industry is taking to distributed fiber optic sensing.
Success in motorsports is measured by winning and that requires gaining every possible advantage over the competition. The most expensive car doesn’t always win the race. Rather it is typically the one that is backed by the best people using the best technology