In many non-contact level measurement technologies, build-up on vessel walls and continuous profile changes pose real challenges. Such vessel changes alter the way beams emitted by the instruments are detected. This usually mandates another mapping of the vessel, which is expensive and time-intensive.
ABB laser level measurement products are not affected by such challenges. They deliver extremely narrow laser beam that does not interfere with vessel walls. Despite vessel changes or build-up, they do not interfere with the laser, which points at the surface for performing measurement. This reduces operator intervention and considerably increases reliability.
Dealing with Build-up for Solids
A typical example of this problem is a wood chip silo, in which the wood chips stick to the vessel walls and the shape is always changed by the build-up. The changing shape has an impact on any measurement method that is dependent on a wide beam, requiring constant echo mapping and reconfiguration.
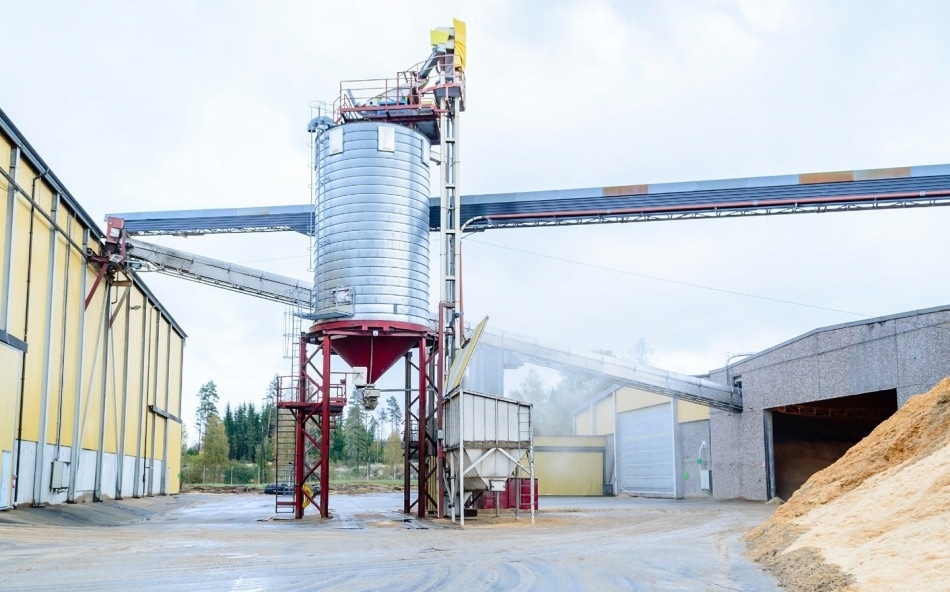
Wood chip silo
A LLT100 laser level transmitter fitted on top of the silo, on the other hand, will aim in the middle of the silo and does not interact with the build-up or the walls. This avoids the need for silo mapping. The LLT100 has the ability to automatically detect the real surface due to the low divergence properties of its laser.
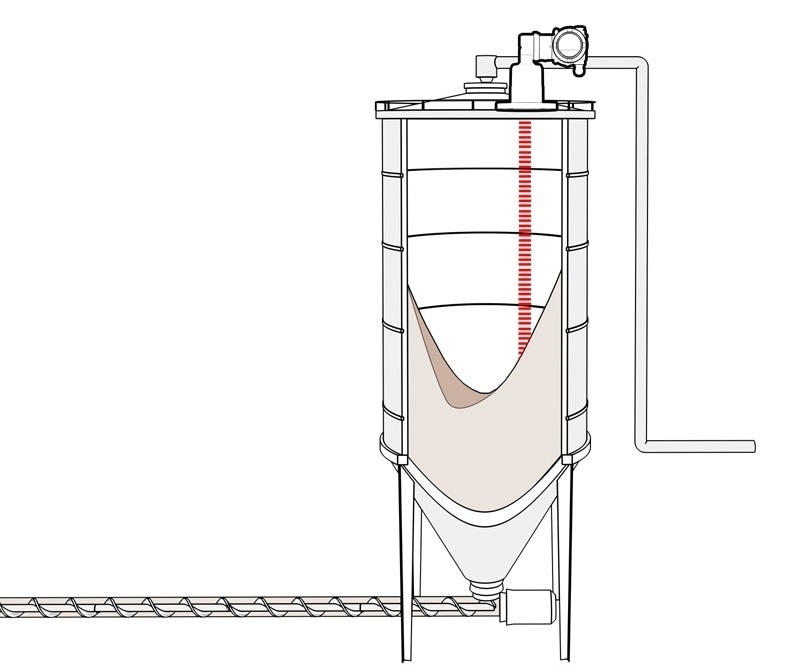
Narrow LLT100 laser beam not affected by build-up
Dealing with Build-up for Liquids
Build-up all poses challenges in stilling wells, a typical condition in which the liquid inside can accumulate on the well sides and form a solid residue if it is sticky or dirty.
For example, in a wastewater surge tank application, the build-up was intense and interfered with all previous measurement methods. For performing contact measurements, the well had to be cleaned every week. Conventional non-contact techniques cannot be applied since they would latch on the build-up almost instantly.
Laser level provided a considerable reduction in maintenance as it operates to the point at which the well is fully filled up by residues. The time between the cleaning periods increased from once in a week to once in six weeks, which led to considerable cost and time savings.
Although only two examples have been discussed, such conditions are very common in industrial applications. Vessel build-ups are often formed by sticky or humid bulk solids. Various liquids can also lead to build-up of materials on vessel sides. This can be the case even with sludge and slurries. Laser levels are another way in which users can carry out non-contact level measurement. As has been observed, in many instances, it results in considerable reductions in cost. It simplifies the measurement process.
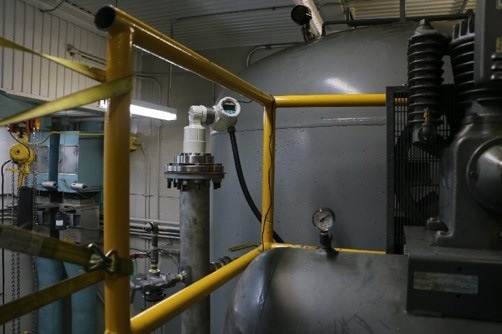
Level measurement in stilling well
Conclusion
Constant profile changes and vessel build-ups that happen within silo walls pose challenges for various level measurement technologies.
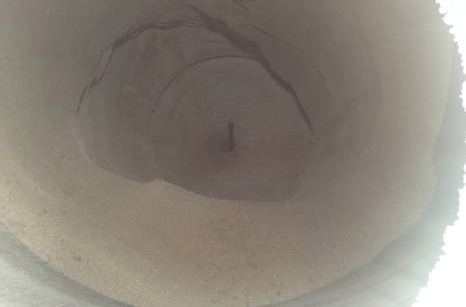
Vessel build-up in silo
ABB lasers have the ability to read silo levels without being influenced by these factors, enabling process control or inventory measurement without the need for maintenance or adjustment.
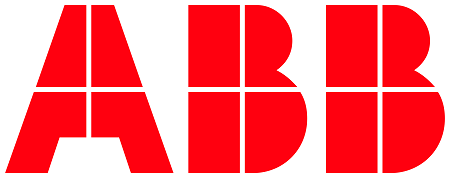
This information has been sourced, reviewed and adapted from materials provided by ABB Analytical Measurements.
For more information on this source, please visit ABB Analytical Measurements.