Companies that manufacture goods are often faced with challenges when it comes to monitoring inventory levels in silos, tanks and bins. Vendors and solution providers that supply raw materials and help companies monitor their inventories, respectively, face a similar challenge in inventory management.
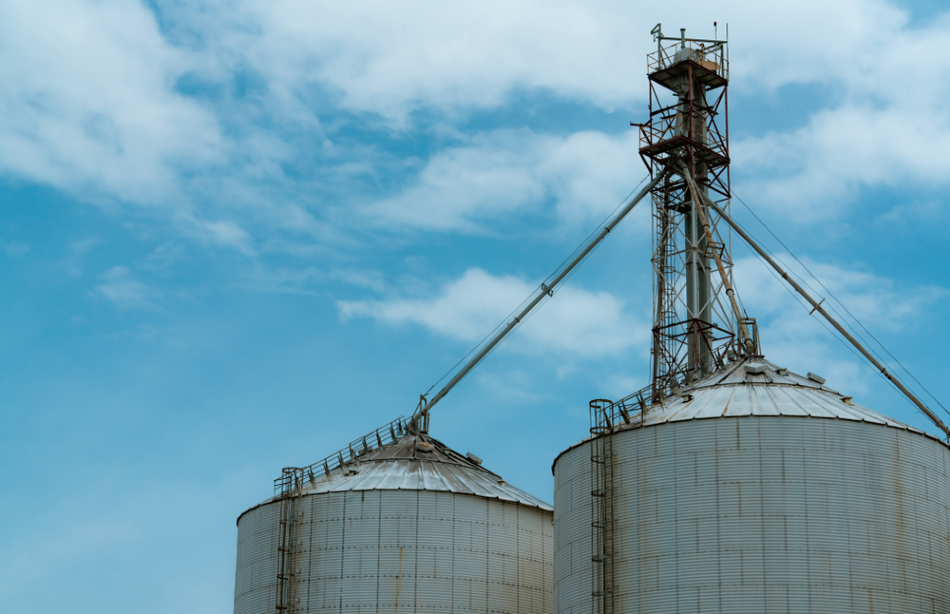
Image Credit: Shutterstock/fahroni
Inventory carrying costs as well as the cost and value of raw materials are starting to rise. Generally, suppliers share the monitoring of material inventories with processing companies and team up to help their customers manage material inventories.
Organizations that develop systems, which aid suppliers and processing firms to manage their inventories, are developing solutions so as to address the growing needs of level sensors, and are also designing sophisticated communications networks and software so that information can be accessed easily and instantly.
Plant personnel often face complex issues when it comes to measuring solids and powders in silos, bins and tanks. For instance, issues like material level and volume, accuracy of inventory, unevenness of the material surface being measured, and build-up of solids and powders in the vessel are often encountered in plants.
.jpg)
3DLevelScanner
In recent years, acoustics-based technology has turned out to be a suitable solution to address these problems. The sensoring device, often known as a 3DLevelScanner, is linked with a set of solutions that are capable of determining virtually all types of solids and powders in extreme conditions. The device provides volume as well as level data using sensitive monitoring software that can be modified to match the requirements of various departments within an organization or can be shared with vendors who manage material inventories.
.jpg)
The 3DLevelScanner is a non-contact, dust-penetrating sensor that sends bin level and volume data to a PC.
In contrast to single-point devices, the 3DLevelScanner maps the material’s surface to account for variations in total volume, level and surface topography. This data is utilized to provide information to users about the material level in the bin and to assess the material volume.
Reports Both Level and Volume
In a majority of applications involving powders, which have uneven material surfaces and tend to build up in sidewalls, there will be points in the vessel that can be either higher or lower than the majority of the contents. The irregularities in the surface of the material can be detected to account for excessive build-up and different topography for volume calculations.
3D Visualization of Irregular Material Surfaces
After taking multiple measurements in the bin and then plotting the topography in the bin, the 3DLevelScanner produces a computerized profile that depicts low and high spots in the vessel, and also the build up of material on the vessel sides. In case of single point devices, a measurement may indicate that the bin is virtually empty even when a large amount of material is left in the bin. Maintenance management can benefit from this visualization feature and clean the bin at the optimal time. In addition, a 3DLevelScanner can accommodate higher temperatures without compromising on measurement accuracy.
.jpg)
The image on the left shows the irregular material surface during the empty cycle; the image on the right is the 3D visual representation created by the software.
Performs in High Levels of Dust
An extremely low frequency acoustical signal is used by the 3DLevelScanner to infiltrate dust and take measurements that are ascertained depending on the time it takes the signal to reach the powder or solid material surface and return to the device. These low frequency acoustical signals can infiltrate suspended dust. Such capability is not provided by other technologies whose signals are not consistent while taking measurements in dusty conditions. Moreover, the 3DLevelScanner is self-cleaning and requires minimum maintenance.
.jpg)
The outside of the sensor is coated with dust. Inside the transducers are clean and fully operational.
Accuracy in Wide Diameter or Large Bins
Processors and suppliers of materials, such as sodium, lime, silica, bentonite and alumina, may keep these materials in large vessels. Single or multiple 3DLevelScanners can be placed on the vessel to get the desired level of accuracy. However, a single scanner can be employed in a large bin if the aim is to get continuous and consistent level indication, instead of volume accuracy.
.jpg)
When two or more sensors are mounted on a single vessel, the software aggregates the data to provide an average level, volume and single 3D image.
Conclusion
.jpg)
The levels of all vessels can be monitored by personnel from various departments from a common database in real time.
Different departments within an organization may require bin level or volume data. Plant personnel use inventory data to do their jobs. Precise and timely data helps them simplify production, procure and supply optimally, and report economically. Data is available instantly and round the clock to help users improve operations and make informed decisions based on opportune and precise data.
.bmp)
This information has been sourced, reviewed and adapted from materials provided by BinMaster.
For more information on this source, please visit BinMaster.