In the current era of the Industrial Internet of Things, real-time monitoring of the state of a flow pipe is essential. In contrast to the traditional flow meters, which are connected in line with the flow, ultrasonic liquid flow sensors are non-intrusive alternatives as they are installed externally with no hindrance to the flow.1 This gives them the ability to work with numerous kinds of liquids, making them attractive for wide industrial applications.
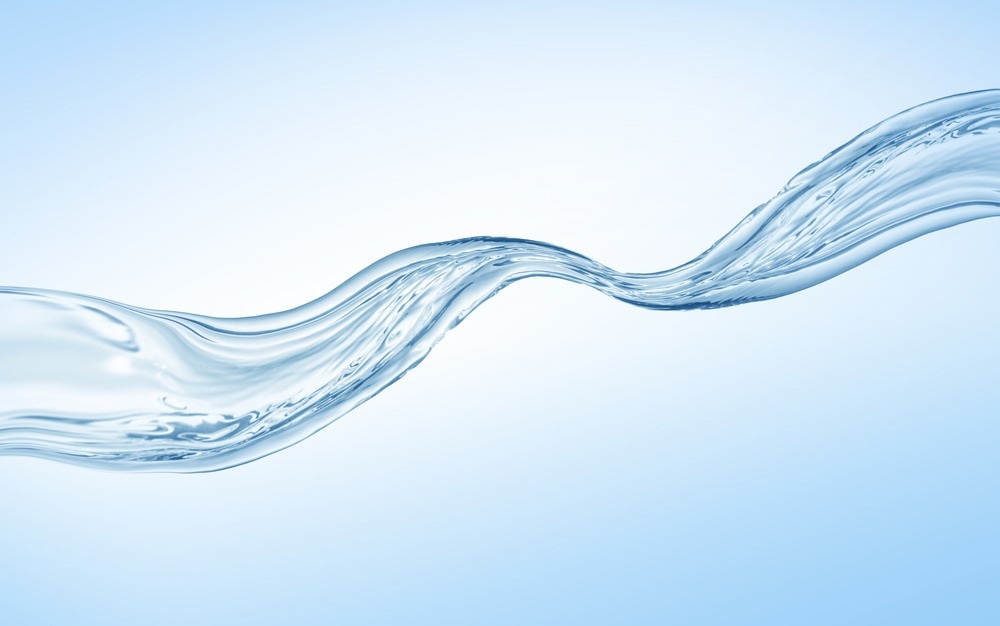
Image Credit: CK Foto/Shutterstock.com
Introduction to Ultrasonic Liquid Flow Sensors
The ultrasonic Doppler method was first developed in the 1950s to study cardiac function and blood flow in the human body.5 Now, it has been advanced in the form of ultrasonic liquid flow sensors, which play a crucial role in numerous industries.
Ultrasonic liquid flow sensors measure the time ultrasonic waves travel from one transducer (sender) to another (receiver). The measured time delay and the distance between the transducers determine the flow rate.4 Ultrasonic liquid flow sensors generally work on one of the two concepts: Doppler effect or transit time.
Doppler effect-based ultrasonic liquid flow sensors measure the fluid velocity by detecting the frequency shift due to the motion of particles.4 Alternatively, transit time ultrasonic liquid flow sensors are based on the time difference between ultrasonic signals traveling along and opposite to the liquid flow.1 Thus, their measurements are influenced by the acoustic properties of the liquid along with its density, viscosity, temperature, and suspended particles.4
Advantages of Ultrasonic Sensors in Liquid Flow Measurement
Ultrasonic sensors offer the advantages of being readily available, easy to install (do not have any moving parts), and contactless operation.1 They do not cause any pressure drop during the flow measurement and work in wide measurement ranges.2 The contactless nature of ultrasonic liquid flow sensors prevents them from general wear and tear, making them low-maintenance and long-lasting.4
Since ultrasonic liquid flow sensors can measure the flow rate from outside the pipe, they are preferred while measuring dangerous or toxic liquids.2 Furthermore, they can identify in situ flow rates outside the pipe without interrupting the process. Bi-directional measurements are also possible using ultrasonic liquid flow sensors, making them suitable when the reverse flow needs to be monitored. 4
Ultrasonic liquid flow sensors based on the Doppler effect are very important in multiphase flows. They can help with understanding fluid dynamics through flow structure measurements, detection of gas-liquid interface position, and multiphase rheology measurements. From an industrial point of view, these functions enhance the scope of investigations and modeling in fluid dynamics.5
Applications Across Various Industries
The most common applications of ultrasonic liquid flow sensors include the measurement of liquid flow in pipes, especially in systems where the flow must not be disturbed. Additionally, they are used to measure liquids like water, wastewater, acids, solvents, oils, hydrocarbons, and other chemicals in potable water applications. Apart from measurements, they can also monitor and control heating and ventilation in air conditioning systems.4
Ultrasonic liquid flow meters can be used with various fluids, even corrosive and abrasive liquids. This makes them suitable for use in harsh industrial environments. For instance, they are widely employed in the mining industry during the transport of slurry before the separation of minerals as the slurry flow rate must be monitored in real-time and optimized for further processing.1
Since ultrasonic liquid flow sensors need not have physical contact with the fluid, they are ideal for application in food and pharmaceutical processing, where inserting a probe into the liquid is undesirable. The high accuracy and stability of the ultrasonic liquid flow sensors make them ideal for critical applications like monitoring of chemicals and fuels in the medical field and space explorations, respectively. 4,6
Doppler effect-based ultrasonic liquid flow sensors facilitate instantaneous velocity measurement in multiphase flow systems. This provides assurance and reliability, process control and optimization, and industry production estimation.5
Key Features and Benefits of Ultrasonic Liquid Flow Sensors
Traditional flow meters are generally calibrated by assuming the pipe is full; thus, measuring the flow rate in partially filled pipes is difficult. In devices like boilers and water desalination plants, remote flow rate measurements are critical to optimize the operating conditions.1 This is where ultrasonic liquid flow sensors prove beneficial, especially in remote and hazardous areas where direct human reach is unsafe and difficult.
Other non-invasive sensors commonly used in the medical field are based on X-rays, gamma rays, and neutrons, which have the major drawback of being radioactive but are still used for their highly reliable measurements. Ultrasonic liquid flow sensors prove to be equally reliable non-radioactive alternatives.3
Ultrasonic liquid flow sensors are preferable for measuring opaque or non-transparent fluids, which is generally true in multiphase flows such as water-oil two-phase flow. With machine learning, the sensors can reveal information about flow turbulence, phase fraction, velocity distribution, and rheological evolution in such flow systems.5
Case Studies Demonstrating the Effectiveness of Ultrasonic Sensors
The semiconductor industry uses toxic liquids with very small flow rates. These cannot be measured by the traditional flowmeters based on temperature or pressure gradients, as they are neither very stable nor capable of measuring sufficiently low flow rates. Since semiconductors form the backbone of the latest technological advancements, ultrasonic liquid flow sensors are crucial in the semiconductor industry. Ultrasonic liquid flow sensors with the capability to measure a flow rate below 1 ml/min have been developed using appropriate ultrasonic transducers.2
Using appropriate machine learning approaches, ultrasonic liquid flow sensors have also been successfully employed to characterize two-phase gas-liquid flow systems.3 Such multiphase flow regimes are common in key industrial operations like nuclear power plant steam generators, metallurgy, bioengineering, chemical engineering, and petrol transportation.5
Space explorations require urgent and accurate measurements of on-orbit liquid propellant flow, fuel tank level, and mixture ratio of bi-propellant systems. Most of the satellite liquid propellants are poisonous and corrosive. Thus, conventional intrusive flow measurement techniques are unsuitable as the sensors may corrode and ultimately be destroyed in space during long-term explorations. Ultrasonic liquid flow sensors were successfully employed by the European Space Agency for satellite propulsion systems in the early 21st century.6
References and Further Reading
- Munasinghe, N., & Paul, G. (2020). Ultrasonic-Based Sensor Fusion Approach to Measure Flow Rate in Partially Filled Pipes. IEEE Sensors Journal, 20(11), pp. 6083–6090. doi.org/10.1109/jsen.2020.2972376
- Takamoto, M., et al. (2001). New measurement method for very low liquid flow rates using ultrasound. Flow Measurement and Instrumentation, 12(4), pp. 267–273. doi.org/10.1016/s0955-5986(01)00023-1
- Nnabuife, S. G., et al. (2019). Identification of gas-liquid flow regimes using a non-intrusive Doppler ultrasonic sensor and virtual flow regime maps. Flow Measurement and Instrumentation, 68, p. 101568. doi.org/10.1016/j.flowmeasinst.2019.05.002
- Ultrasonic Flow Meters | Advantages of Ultrasonic Flow Meters. (n.d.). Micronics. Available at: https://micronicsflowmeters.com/ultrasonic-flow-meters/
- Tan, C., et al. (2021). Ultrasonic Doppler Technique for Application to Multiphase Flows: A Review. International Journal of Multiphase Flow, 144, p. 103811. doi.org/10.1016/j.ijmultiphaseflow.2021.103811
- Chen, Y., et al. (2021). Continuous ultrasonic flow measurement for aerospace small pipelines. Ultrasonics, 109, p. 106260. doi.org/10.1016/j.ultras.2020.106260
Disclaimer: The views expressed here are those of the author expressed in their private capacity and do not necessarily represent the views of AZoM.com Limited T/A AZoNetwork the owner and operator of this website. This disclaimer forms part of the Terms and conditions of use of this website.