Printed sensors have emerged in recent years as attractive technologies in several innovative fields, such as wearable tech and health monitoring. This article will provide an overview of this innovative technology.
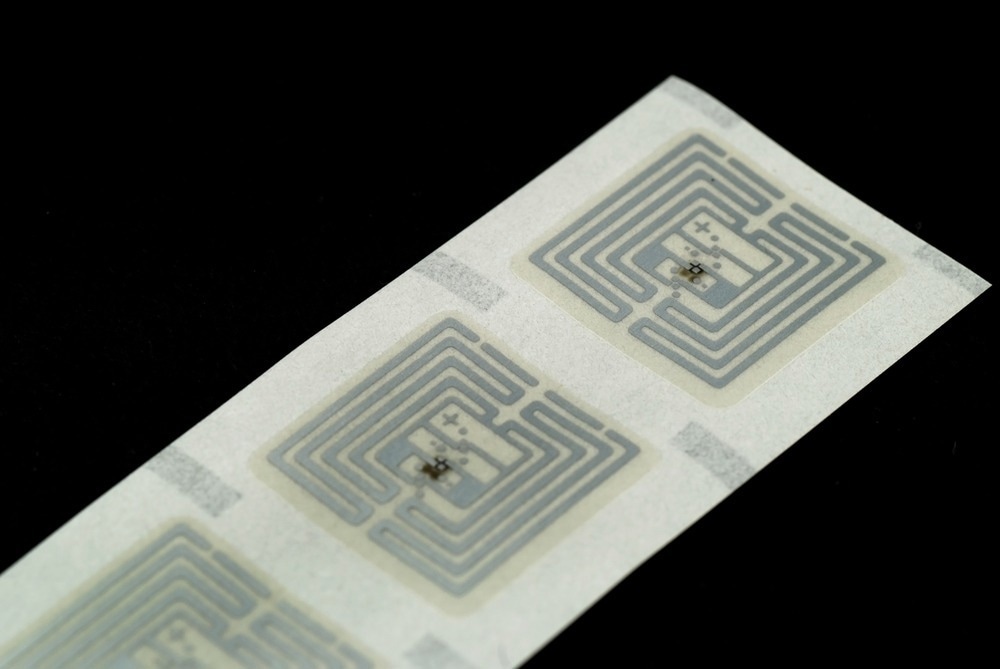
Image Credit: Albert Lozano/Shutterstock.com
Introduction to Printed Sensing Technology
Since the 1960s, microelectromechanical systems (MEMs) have been a central technology in multiple industries and scientific fields to provide sensing capabilities for various critical applications. However, in recent years, these handy and reliable technologies have been increasingly replaced by printed flexible sensors.1
Developments are largely due to the emergence of wearable technologies in fields such as health monitoring, telecommunication, and biological energy harvesting. A flexible sensor can cope with much more mechanical deformation than conventional MEMS devices without experiencing any damage or critical failure.
Recent advances in inkjet printing and related technologies have significantly expanded the capabilities of the flexible sensor market. Printed electronics themselves are not new: the field emerged in the 1950s with groundbreaking research by Nippon Telegraph and Telephone. 2
Types of printed flexible sensors include printed biosensors, touch sensors, pressure sensors, force sensors, temperature sensors, biometric sensors, humidity sensors, gas sensors, and chemical sensors. 3 The printed sensor components, which are composed of specialty inks and polymers, are integrated into substrates such as textiles, paper, foil, or plastic.
Advantages of Printed Sensing Technology
In the emerging world of Industry 4.0, many everyday objects have been getting smarter, and this is largely due to developments in the printed sensor field. Additionally, the capabilities of wearable, flexible technologies have evolved at a rapid pace due to advantages conferred by printed sensors.
Conventional MEMS-based sensors, while the technology is mature and offers good performance for a number of applications, are generally rigid, inflexible, expensive, and bulky. They are manufactured using materials such as glass, silicon, and ceramics and are prone to damage under deformation.
Printed flexible sensors have a number of advantages over conventional sensing technologies, such as cost-efficient production, large-area sensor capabilities, fast stimuli response, and the possibility of further reducing material costs by integrating them with other printed electronic components.3 Furthermore, printing gives infinite design freedom for flexible sensors.
Compared to conventional circuit board and sensor manufacture, printing is a high-throughput process, offering significant savings in terms of time, high volume production, and materials across all stages of the manufacturing process.
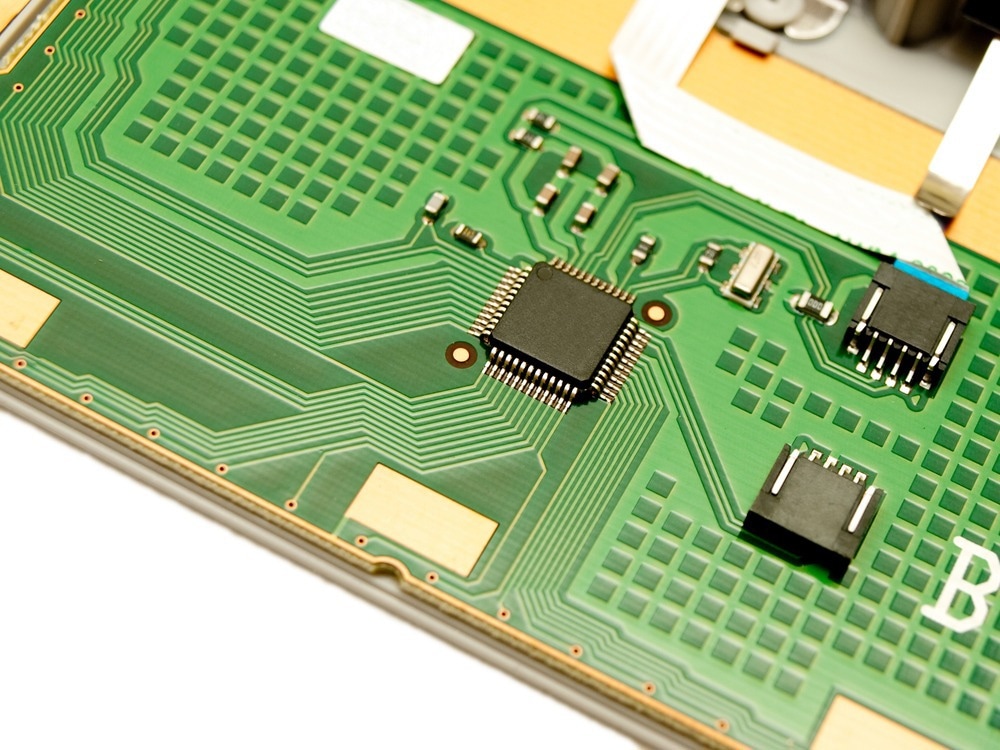
Image Credit: Smart7/Shutterstock.com
Applications of Printed Sensing Technology
Printed sensors are largely used in the life sciences, automotive industry, energy sector, aviation, and electronics. Biofunctionalized printed sensors possess good selectivity and sensitivity, which make them advantageous choices for monitoring and controlling gas mixtures, and detecting even the smallest trace amounts of potentially toxic substances.4
Printed piezo sensors are commonly used to detect pressure in a number of sectors, such as smartphones and flexible electronics. Printed thermocouples can be used to provide temperature monitoring and control in a number of industrial machines and smart textiles. Strain gauges can be printed directly onto industrial parts in specific locations to monitor stress in multiple industries.
Smart textiles are revolutionizing fields such as athletics and physical therapy. Printed flexible sensors are a central technology in this emerging technology, able to monitor body movements without risk of damage to sensitive components due to deformation.
The field of robotics has benefited greatly from flexible printed sensors, which improve precise control and feedback in robotic arms as well as enhance safety and responsiveness. Additionally, printed sensors have found application in the food industry, where they can be integrated into color-changing smart packaging, which can monitor gas levels and freshness, improving food safety. 4
Case Studies of Successful Implementation
There are a number of notable advances in the printed sensor field, with a plethora of research papers in recent years demonstrating how the technology is maturing.
Canadian company e2ip technologies has drawn on 30 years of experience in printing to produce flexible, high-precision and cost-effective printed sensors. The company produces screen-printed electrodes for applications such as blood glucose monitors and electrocardiograms, force sensors, and clear conductive sensors fabricated out of PEDOT ink on flexible substrates. 5
Thin Film is another company that utilizes printed sensors for package tracking. This sophisticated technological solution monitors the humidity and temperature levels of products such as medicines, which is vital for ensuring their quality and safety during transportation. 1
Tekscan has developed FlexiForce, a flexible, printed force sensor that can measure relative changes in applied load or force and feedback to the user using LEDs, improving real-time monitoring in industries such as manufacturing. 1
Future Trends and Growth Potential
According to Flexible Market Insights, the printed and flexible sensors market was worth around $8.8 billion in 2022. It is predicted that the market will grow to around $18.8 billion by 2033, a CAGR of 7.1% over a ten year period. 6
There are a number of key factors that are shaping the future direction of the market, including increased point-of-care diagnostic applications, increasing demand for wearable technologies, rapid growth in the consumer electronics market, and emerging applications in industries such as the automotive and healthcare sectors.
Furthermore, technological advances in additive manufacturing and printing are playing a key role in market growth, with increasing investment by key players in multiple industries accelerating research, development, and innovation in this emerging Industry 4.0 technological sector.
References and Further Reading
Tekscan, Inc. (2023) Understanding the Limitless Potential of Printed Force Sensors [online] azosensors.com. Available at: https://www.azosensors.com/article.aspx?ArticleID=2703
Wu, W. (2022) Printed Electronics Technologies Chapter 1: Introduction to Printed Electronics [online] books.rsc.org. Available at: https://books.rsc.org/books/monograph/2018/chapter/4608186/Introduction-to-Printed-Electronics
Cephas, C. (2022) Benefits and uses of flexible printed sensors [online] tapecon.com. Available at: https://www.tapecon.com/blog/benefits-and-uses-of-flexible-printed-sensors
Fraunhofer IFAM (website) Customized functionalization of parts using printed sensors [online] ifam.fraunhofer.de. Available at: https://www.ifam.fraunhofer.de/content/dam/ifam/en/documents/Shaping_Functional_Materials/functional_structures/Printed%20Sensors.pdf
E2ip (website) Printed Electronics Sensors [online] e2ip.com. Available at: https://e2ip.com/essentials/printed-sensors/
Future Market Insights (website) Printed and Flexible Sensors Market [online] futuremarketinsights.com. Available at: https://www.futuremarketinsights.com/reports/printed-and-flexible-sensors-market
Disclaimer: The views expressed here are those of the author expressed in their private capacity and do not necessarily represent the views of AZoM.com Limited T/A AZoNetwork the owner and operator of this website. This disclaimer forms part of the Terms and conditions of use of this website.